ABB overcame multiple challenges while upgrading the System 800xA, the process control system in one of the largest Uniper power stations in Europe, Maasvlakte Power Plant 3 (MPP3) in Rotterdam, Netherlands.
The power station is located in a major industrial and port area that was built as an artificial peninsula to expand the Port of Rotterdam. MPP3 has a total net capacity of 1,070 MW and is part of the Uniper Energy Hub, which will play a key role in supplying energy to the Netherlands in the future. MPP3 covers approximately 5% of the total energy demand in the Netherlands.
Image currently unavailable
Image currently unavailable
Image currently unavailable
Image currently unavailable
Image currently unavailable
Image currently unavailable
Port of Rotterdam Maasvlakte Power Plant 3
COVID-19 brought standards for managing demanding service projects to a new level. Working from home instead of the office, accessing systems remotely instead of working on them on site, video conferences instead of in-person meetings – these are just a few of the challenges that needed to be organized and coordinated in a structured way. Technical collaboration and communication with the project team and on-site contact at the power station in Maasvlakte changed, so new solutions had to be found.
"On the one hand, we realized that we were able to organize and structure many tasks remotely. On the other hand, we also saw very clearly how valuable it is to have personal contact with the customer on site – whether discussing ideas at the coffee machine or going out and testing the solution we just discussed on the equipment on site,” says Jörg Rottmann – Head of Service Export Minden.
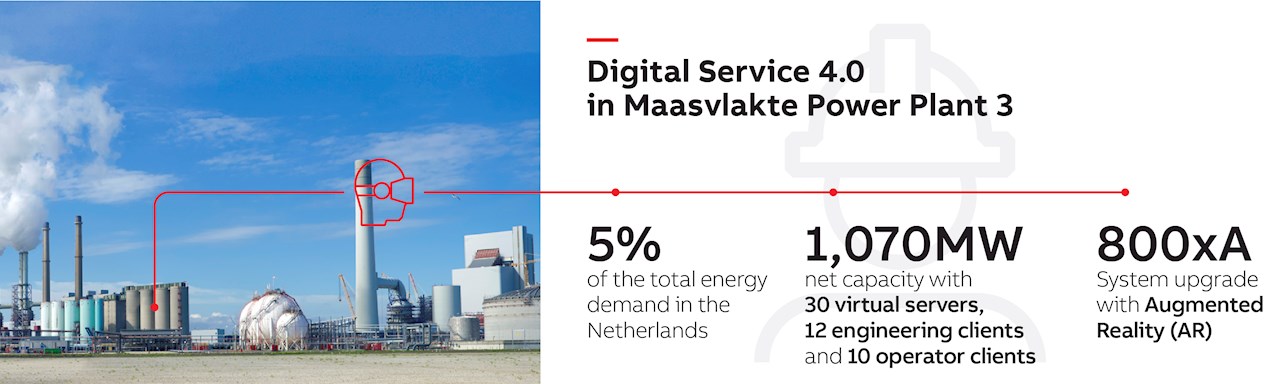
Planning, installation and engineering for the new System 800xA were run from the virtual environment at the test field in Minden over a period of four months. The experts updated together the entire System 800xA with more than 30 virtual servers, 12 engineering clients and 10 operator clients to the next version.
“Thanks for all the care and effort you put into ensuring all of this technology would work together seamlessly to conduct a successful FAT (Factory Acceptance Test). It was completely different from an “in-person” FAT, but as this project proved, it was effective,” says Timothy Kleijn, Uniper’s Project Manager for the System 800xA upgrade.
The upgrade of the System 800xA currently in use includes:
- Operating and monitoring system
- Boiler protection system engineering
- Symphony Plus Historian and information system
- BoilerMax and BoilerLife optimization
- Upgrade of process quality monitoring
- Conversion and optimization of over 1,000 process graphics
- Commissioning in four weeks
Mission impossible
COVID-19 travel restrictions also endangered plans to conduct the scheduled FAT. The only way to avoid postponing the date, which would have delayed the project, was to perform the test remotely.
The use of Augmented Reality (AR) and Virtual Reality (VR) headsets in this practical project clearly demonstrated the added value this technology has to offer. The VR headset enables engineers to move in the customer’s system and view the system together virtually. This made it possible for ABB’s FAT to be presented in the direct environment thanks to a user interface displayed as an interactive 3D project.
“Ultimately, we had even more milestones ahead of us, the FAT was performed remotely and it was possible to partially commission the system from Minden – not on the system itself as is usually the case,” says ABB’s Lead Engineer, Eike Schmitt – HSI Expert ABB Minden.
Image currently unavailable
Image currently unavailable
Image currently unavailable
Image currently unavailable
Image currently unavailable
Image currently unavailable
Image currently unavailable
Image currently unavailable
Image currently unavailable
Image currently unavailable
Image currently unavailable
Image currently unavailable
Eike Schmitt at the Minden test field View of the Quad Monitor Operator Client OC0006 using an AR headset Customer view of the mixed reality image Remote desktop view of the SAS image via video conference
Virtual commissioning
Security specifications between the Netherlands and Germany had been expanded and were even more stringent during the commissioning period due to COVID-19, which made it necessary to perform some of the test procedures and complete a special set of documentation in the system on site (COVID-19 tests, masks, safety protocols, etc.) Uniper accepted a high degree of responsibility for ensuring the safety of everyone involved with everything from excellent crisis communication all the way to advanced safety training sessions.
Of the four weeks that were originally planned for commissioning, only two took place on site. The remaining tasks were performed remotely from Minden in close collaboration with the on-site project team.
“The system was successfully recommissioned on time. This example clearly illustrated that it’s also possible to achieve project goals even under extraordinary circumstances. Uniper praised the fast, high-quality work performed by ABB,” said Silvia Torrico Muñoz, Sales & Project Manager Export Minden.