Subhashish Dasgupta ABB Corporate Research, Process Automation Bangalore, India, subhashish.dasgupta@in.abb.com; Oliver YongWei-Gu, Rock RenDong-Li ABB Process Automation Shanghai, China, oliver-yongwei.gu@cn.abb.com, rock-rendong.li@cn.abb.com; Carsten Habersetzer ABB Process Automation Göttingen, Germany, carsten.habersetzer@de.abb.com
A key enabler of effective process monitoring is the ability to measure and hence, monitor physical parameters like flowrate, pressure and temperature. ABB, with over a century of experience in flow measurement and control technology, meets measurement requirements across industries such as oil and gas, chemical processing and power generation. Here, the vortex flowmeter is an invaluable member of ABB’s flowmeter portfolio.
The global demand for the vortex flowmeter, stems from its unique capability to measure flowrates of diverse fluids, eg, clean gases, steams and liquids, with high accuracy while being relatively simplistic in construction. These attributes ensure that industries such as oil, gas and chemical (OGC) as well as power generation have access to a cost-effective, low maintenance, and reliable method to measure flow in pipelines, tanks, and industrial chambers, etc. ABB’s vortex flowmeter varieties like VortexMaster flowmeters (FSV 430, FSV 450) are ideal for use on petrochemical raw materials, demineralized water and for direct, cost-effective steam mass flow measurement under diverse conditions →01. While these flowmeters promise the customer high quality performance, there is still scope to push the performance standards beyond current limits. Why is this so? Because measuring flow accurately with vortex flowmeters at low flow velocities is a well-known challenge.
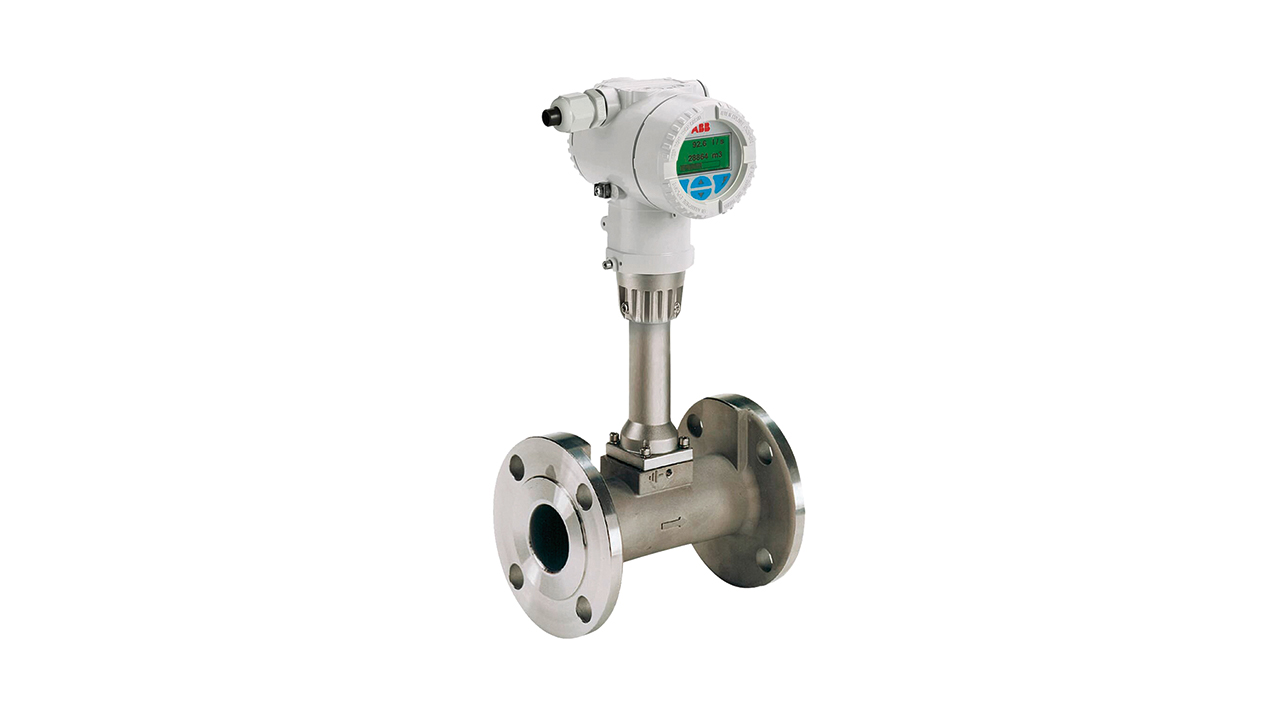
Marrying their experience and expertise in measurement technology with their ability to drive digital innovation, ABB researchers embarked on a journey to develop a high-fidelity multi-physics model of the vortex flowmeter: a tool to evaluate new design ideas for improvement in performance.
Vortex flowmeter ideation and planning
ABB’s existing range of vortex flowmeters are built to allow an excellent flow signal detection and provide measurement immunity from the effects of hydraulic noise and pipeline vibration [1].
Despite the market success of these products, beginning in 2019 and continuing throughout 2020, ABB’s researchers leveraged their commitment, experience and expertise to develop multi-physics models of vortex flowmeters with a clear purpose: improvise existing designs and offer flowmeters with a high degree of measurement accuracy at low flow velocity (lower than 0.2 m/s). The idea was to employ computational fluid dynamics (CFD) in conjunction with structural mechanics analysis, to evolve models that could resolve the complicated flow and structural dynamic events within the flowmeter. And, this would allow for an optimal design, thereby promising quality measurement at low flowrates.
Anticipating the results of rigorous testing of a multi-physics model of the vortex flowmeter, ABB posed the next question, so relevant for innovating: Could such a modeling approach be used as a predictive tool or digital twin for other flowmeters in the future? If so, then this innovative modeling platform would be an invaluable asset to ABB’s flow measurement portfolio and a gamechanger for customers.
Vortex flowmeter from the ground up
The vortex flowmeter functions according to the Karman vortex shedding principle. In short, when a fluid flows through a pipe provided with an obstructing bluff body – a non-streamlined object, vortices are shed on either side of the obstruction, and the pulsating disturbance is recorded by a downstream sensor →02a. The fundamental frequency of the pulsations, f, calculated by the processing unit, is proportional to the velocity, and is hence used to estimate the velocity. The Strouhal number, which characterizes flowmeter performance and is related to its calibration factor, is given by the product of pulsation frequency and bluff body characteristic dimensions divided by the corresponding velocity. Ideally, the Strouhal number, should be independent of fluid velocity, thereby ensuring linearity in performance across a wide range of velocities.
Image currently unavailable
Image currently unavailable
Image currently unavailable
Image currently unavailable
Image currently unavailable
Image currently unavailable
Image currently unavailable
Image currently unavailable
Image currently unavailable
02a This schematic illustrates how vortices are generated as fluids pass through a pipe. 02b The strength or amplitude of the raw vortex signal varies over time and should be strong enough for easy detection. 02c The dominant vortex frequency is shown.
02 Schematics indicating vortices origin and characteristics during flow.
In addition to linearity in performance, strength or amplitude of the raw vortex signal should be adequate for detection under low velocity conditions →02b – c. This is crucial because low velocities are associated with weak signals, and prone to noise adulteration that could result in measurement inaccuracy – a possibly disastrous scenario. Hence, the need to improvise flowmeter designs.
The aim is to generate sufficiently strong vortex signals, so that low flowrate detectability is enhanced. At a given flow rate, the signal strength primarily depends on design features of the flowmeter components. Conventional use of experimental approaches to perform parametric studies on design features to optimize design is cost-intensive and time-consuming due to hardware requirements, availability of resources, etc. Further, complicated physical events are extremely difficult to resolve using experimental studies alone. Models capture a holistic view of critical physical parameters like flow and pressure, whereas experimental studies can only provide a superficial picture of complex physical events. With hesitancy justified, how can accurate, cost-efficient and easy-to-engineer flow meters be designed? Enter ABB’s innovative model-based approach to flow meter design. By adopting this approach to perform a series of parametric studies, ABB creates the optimal design to improve flowmeter performance standards, thereby minimizing the time-to-market and obviating the need for arduous experimental procedures.
CFD model and physics-based digital twin
A CFD model was developed to simulate the complicated fluid dynamics within the vortex flowmeter using the finite volume analysis scheme and leading edge mathematical techniques, such as advanced turbulent wall formulations, to solve the fluid flow conservation equations of mass and momentum, in a 3-dimensional space within the flowmeter domain →03a. Complex time-varying velocity patterns that could be well-resolved by the model contributed to an understanding of the intricacies inherent in the flow process and ultimately led to an ability to predict performance →03b.
Image currently unavailable
Image currently unavailable
Image currently unavailable
Image currently unavailable
Image currently unavailable
Image currently unavailable
Image currently unavailable
Image currently unavailable
Image currently unavailable
03a CFD model: Fine spatial and temporal resolution is shown. 03b The image shows the distribution of predicted complex flow. 03c The model calculates the coefficient of rift over time.
03 CFD model simulated the complicated fluid dynamics within the vortex flowmeter as shown.
The model calculated the coefficient of lift acting on the sensor as a function of time or the signal profile →03c. A fast Fourier Transform of the signal yielded the dominant frequency at the given flowrate. This was possible because a Fourier Transform decomposes functions dependent on space or time into functions dependent on spatial or temporal frequency.
Testing and validating the model
The model was initially validated by comparing the computed results with measurement data gathered from previous tests run on a standard flowmeter, a close agreement between the computed and measured vortex frequencies across the selected range of fluid velocities was realized; this included velocities below 0.2 m/s →04. These results established confidence in the modeling approach.
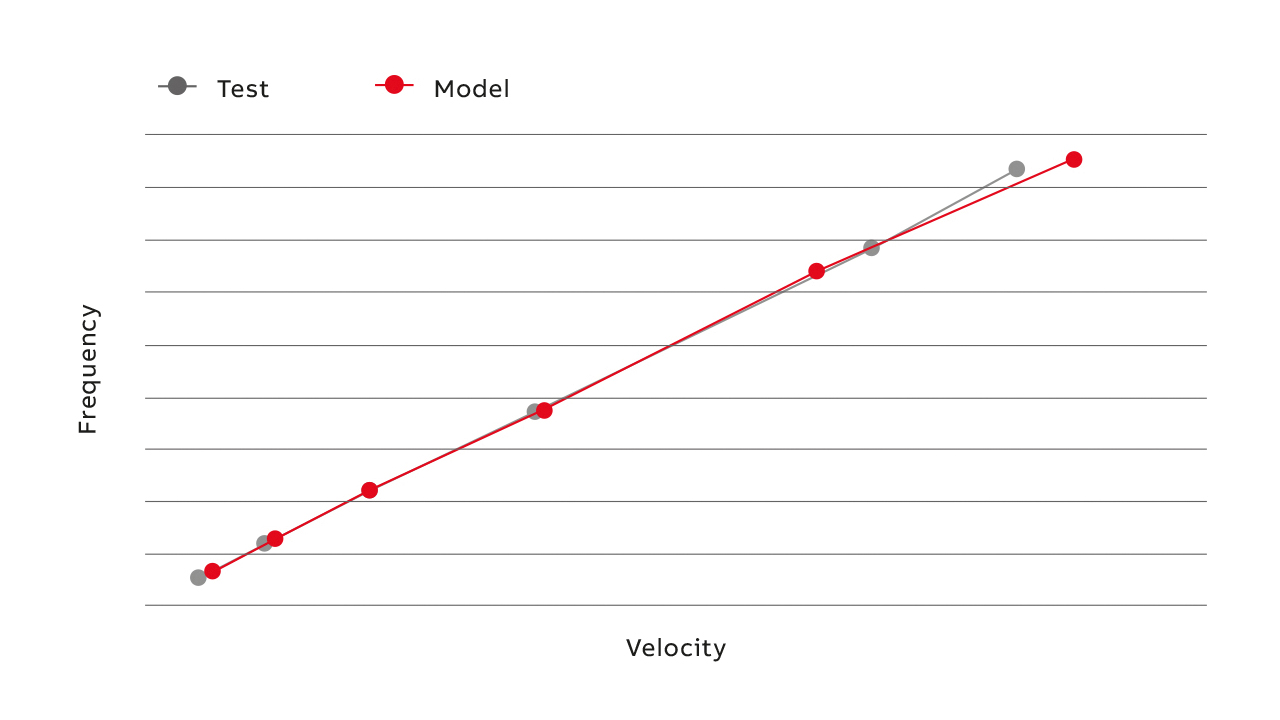
Linearity in performance
In addition to achieving adequate signal strength, it was essential to ensure a high degree of linearity in flowmeter performance. In this way, the device calibration factor obtained at high flowrate will also hold true at low flowrates. For this purpose, the dimensionless Strouhal numbers were calculated and compared with selected Reynolds numbers. Reynold’s numbers for a flow are a measure of the ratio of the inertial force to viscous forces in the flow of fluid bound to a body or channel; it is a non-dimensional parameter of the speed of fluid flow used for flow prediction. Used to describe oscillating flow mechanisms, Strouhal numbers, which are proportional to the pulsation frequency and the buff dimensions and inversely proportional to said velocity; were calculated from the computed and measured vortex shedding frequencies. The Strouhal numbers were found to be independent of the fluid velocities or Reynolds numbers selected in the studies →05, thus ensuring linearity in performance across the selected flow range.
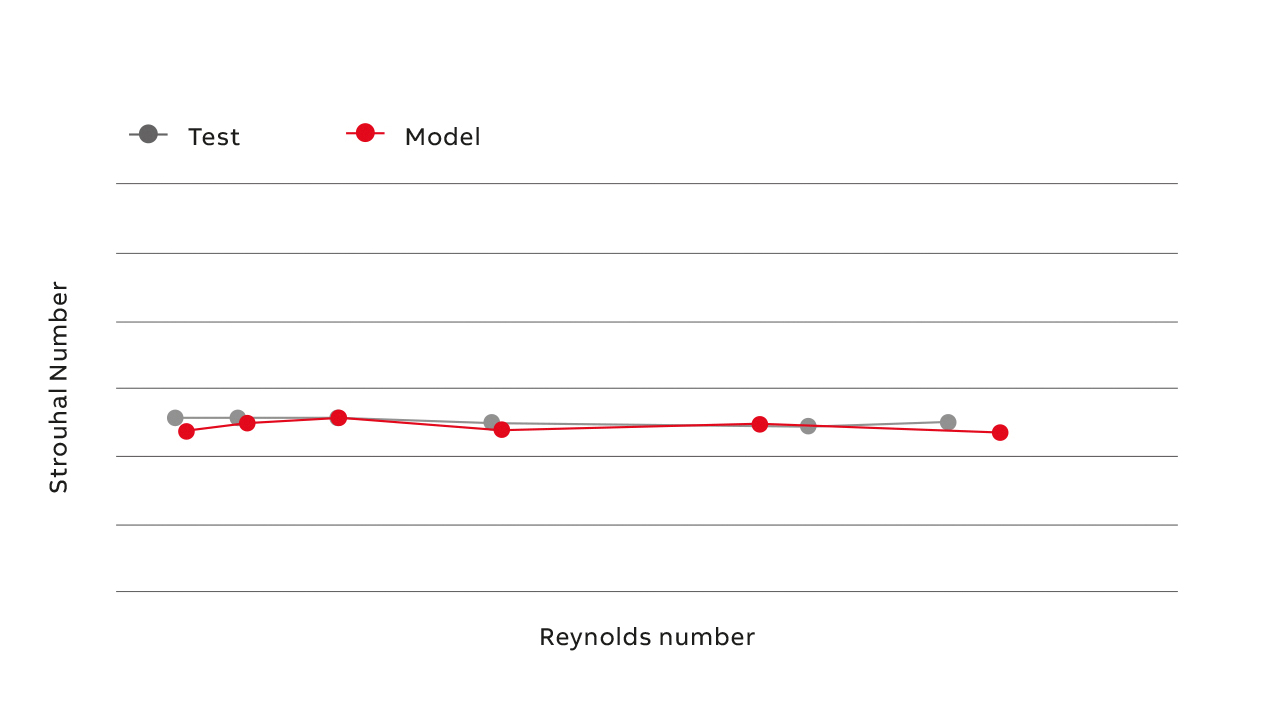
Model-based design optimization
Once the model was validated, several flowmeter design modifications were evaluated. These design modifications were simulated to arrive at the optimum design; one that yields the best signal strength →06.
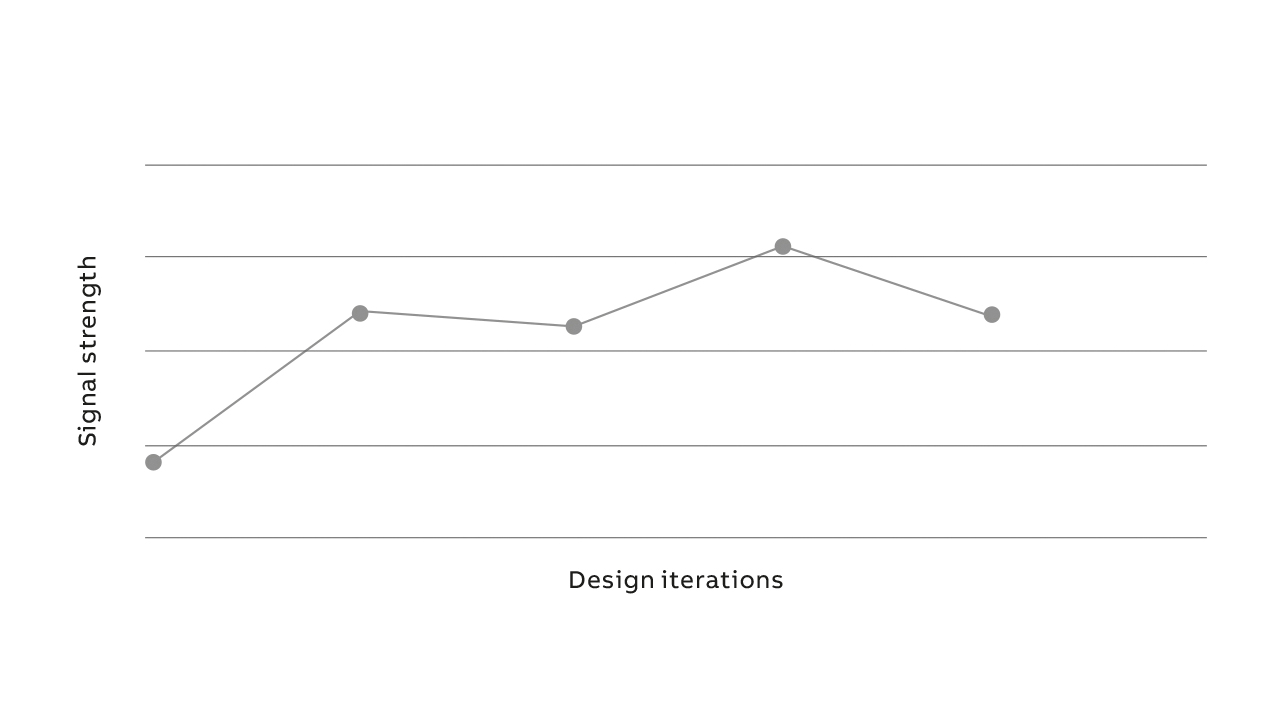
Structural issues
The story would be finished here but for the possibility of disadvantageous structural issues. One possible source of noise that could impair the accuracy of vortex flowmeters is structural vibration of the sensor assembly. Such impulsive forces can negatively affect the output signal. Complimenting the CFD model, a finite element, structural dynamics model was developed that is capable of evaluating vibrational characteristics of the sensor to rectify this affect. Significantly, model results revealed minimum interference between the vortex frequencies and the sensor’s natural frequency →07; thereby providing assurance of the absence of vibration-related artifacts in the flowmeter output signal.
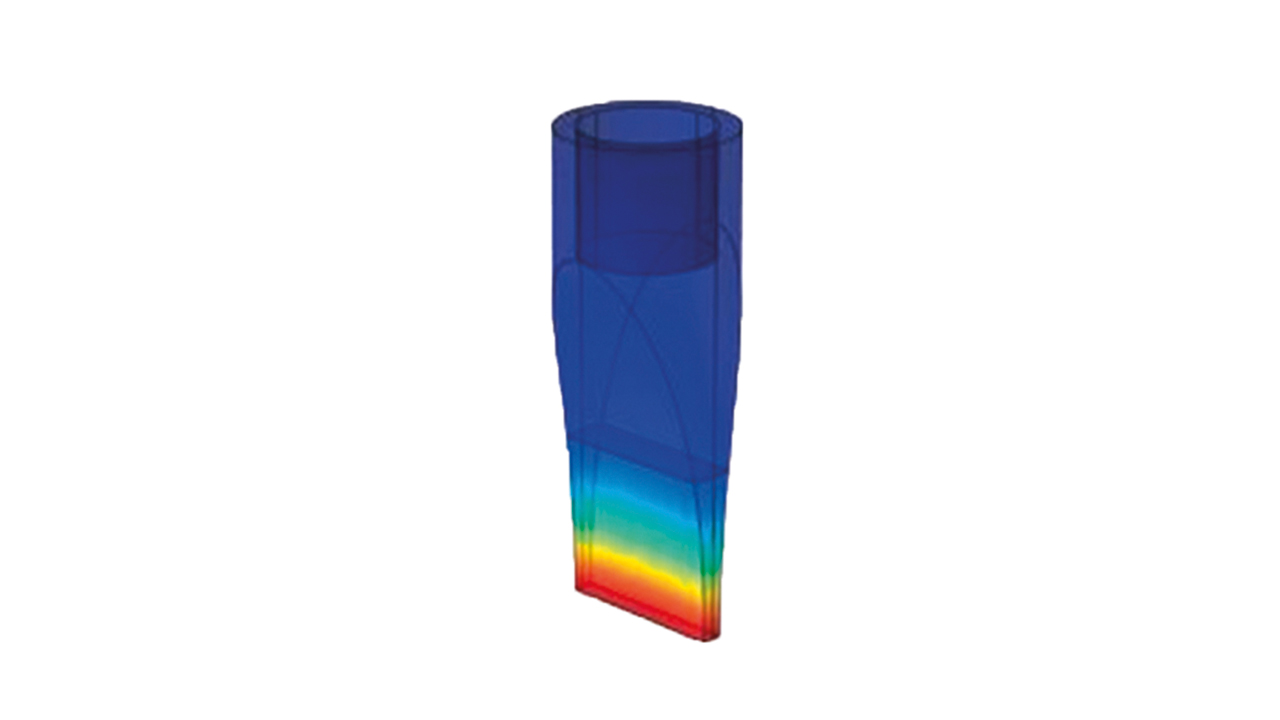
Manufacturing modified flowmeters and subsequent testing
Based on the guidelines from the CFD model, the vortex flowmeter was re-designed and prototyped using the additive manufacturing 3D printing method →08a at an ABB PAMA facility in Shanghai, China. Subsequently, the modified flowmeter was installed in the test rig at ABB’s business testing center →08b, tested to measure the signal strength; this was then compared with the signal strength of the existing conventional flowmeter designs in current use.
Image currently unavailable
Image currently unavailable
Image currently unavailable
Image currently unavailable
Image currently unavailable
Image currently unavailable
08a 3-D printing set up used for the prototype production is shown. 08b The test rig used to measure signal strength, etc. is shown.
08 Prototype production and test rig.
As per the findings in the CFD modeling studies, the preliminary test results showed a significant increase in signal strength of the modified flowmeter with respect to that of the existing flowmeter – under constant, yet, low velocity conditions. Thus, ABB’s primary goal, to improve vortex flowmeter capability by measuring accurately at low flowrates was achieved.
Future flows
The promising success of the model-based approach to improvise the vortex flowmeter has encouraged ABB’s modelling and physics experts to develop extensive prototypes and conduct further testing of modified designs. One important possible application currently under investigation is the expansion of the modeling-approach to evaluate possible design modification benefits in other flowmeters eg, ABB’s swirl flowmeter. Operating according to the same shedding vortex principle, swirl flowmeters are important for measuring volume flow where piping requirements are tight, eg, petrochemical raw material flow. Unlike vortex flowmeters, swirl flowmeters create their own flow profile within the meter, they require only a 3 diameter upstream straight pipe run after a pipe reduction and a 5 diameter after a control valve plus 1 diameter downstream. By expanding this modeling approach to other flowmeter types, ABB addresses the diverse needs of the oil, gas and chemical sectors.
By iterating the vortex flowmeter model approach to other flowmeter applications ABB takes another step to enable innovation.
Through invention, testing and validation, learning, and applying their knowledge and success elsewhere, ABB drives technical innovation in an expanding digital world. For flowmeter customers, this innovation results in optimal performance and cost-effective solutions.
Photo p. 63: ©Chrionny/stock.adobe.com