Yauheni Veryha ABB AG Heidelberg, Germany, yauheni.veryha@de.abb.com
The standard PLC is a familiar and essential component in most automation settings. When functional safety is of particular concern, a special type of PLC is deployed: the safety PLC. A safety PLC can be integrated with a standard PLC. Integrated safety PLCs perform safety functions that control machines and processes in a highly deterministic manner. These PLCs constantly protect against failures in plants that could harm people or equipment or cause environmental damage. If incipient hazards are detected, the safety PLC puts the appropriate equipment into a safe state.
Advantages of functional safety systems
Beneficiaries of functional safety systems are, for instance, material-handling operations, such as distribution warehouses, cranes, industrial lifts and mine hoists, collaborative robots and mobile robot platforms, and scenarios where automated guided vehicles (AGVs) are used.
A well-conceived safety system will allow an enterprise to improve productivity, reduce downtime and optimize costs. The standardized, comprehensive and integrated safety systems provided by ABB also cut automation solution development time and allow the establishment of an environmentally friendly operation. The ABB AC500-S safety PLC lies at the heart of ABB’s industrial safety controller philosophy [1].
The ABB AC500-S safety PLC
ABB’s AC500 controller family is found in many industries. The AC500-S is ABB’s solution for situations where safety is of particular importance →01.
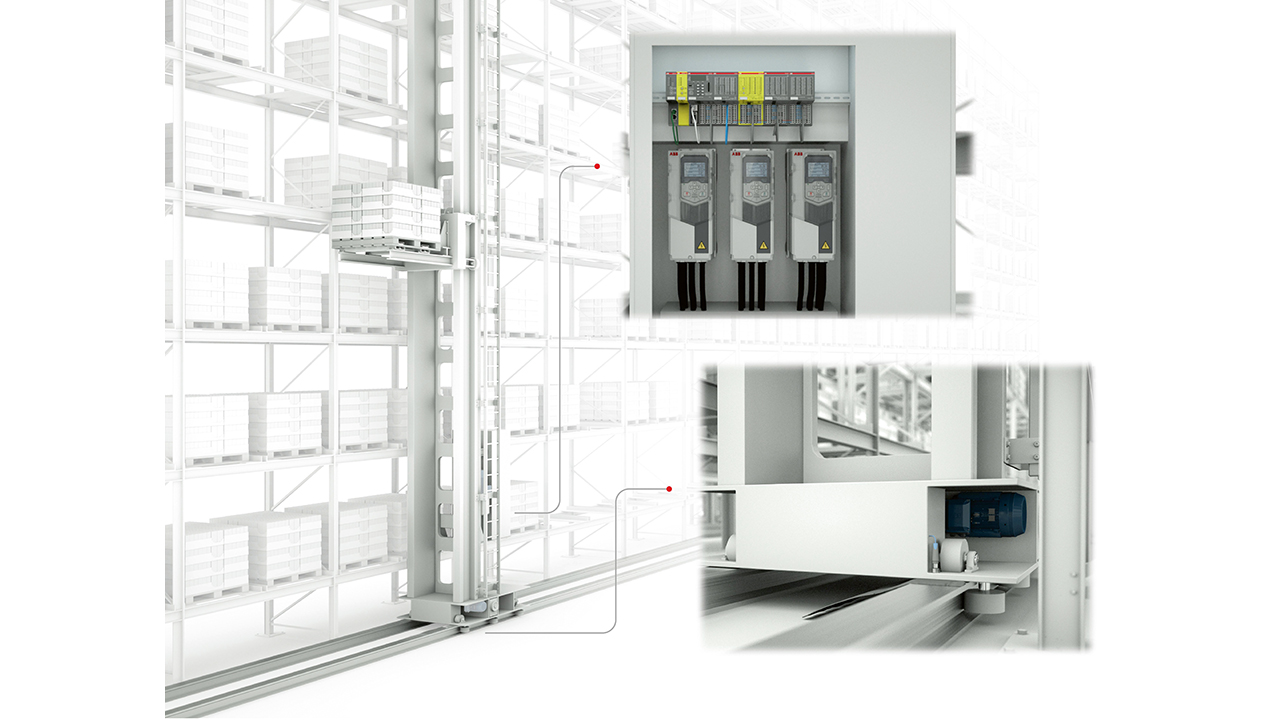
In addition to material-handling situations, the AC500-S is ideal for monitoring and controlling hydrogen filling stations →02, entertainment parks, wind turbines and many other applications.
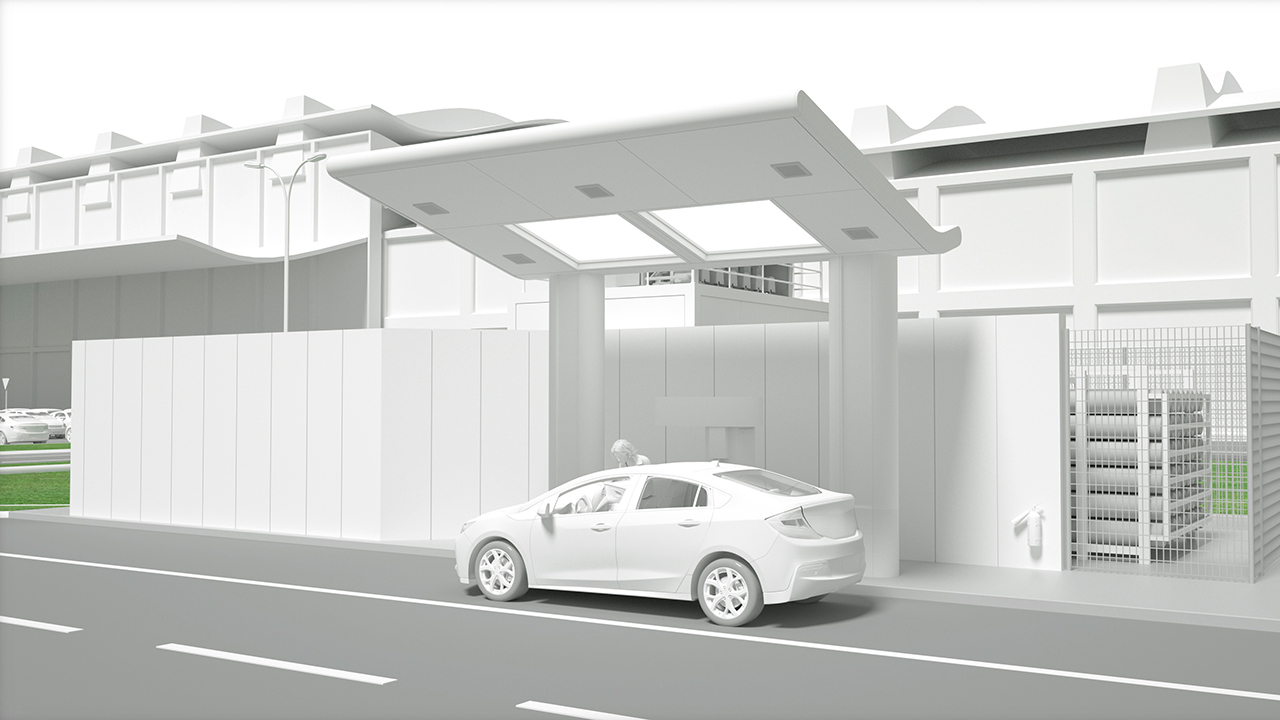
The scalable AC500-S PLC is based on a modular design that incorporates a CPU, AC500-S functional safety, communication modules and I/O modules. The system can be easily expanded when required and includes advanced safety functionality, such as fail-safe condition monitoring, trigonometric functions and floating-point calculations.
The standard AC500 with an integrated AC500-S safety PLC benefits from high-performance CPUs and facilities such as IEC 61131 programming editors, object-oriented programming, multi-user engineering, versioning, a virtual controller, etc. These features improve system flexibility and thus make engineering simpler. The PLC supports communications over PROFINET, EtherCAT, OPC UA, Ethernet/IP, CANopen, CAN J1939, BACnet, etc. and these can be configured in a few simple steps.
The AC500-S is realized as 1oo2 (one-out-of-two) system (in both safety CPU and safety I/O modules). A 1oo2 system includes two microprocessors, each of which executes the safety logic in its own memory area. The results are then compared. If a mismatch in the execution or an error is detected, the system goes to a safe state, which is described for each of the safety modules separately.
The integrated AC500-S safety PLC achieves a safety integrity level (SIL) of up to SIL 3 (IEC 62061 and IEC 61511) and complies with ISO 13849-1 Performance Level (PL) e (the highest of five levels). To qualify as approved to SIL 3 – a rigorous standard that includes resilience against corrupt software injection – a safety PLC must detect over 99 percent of potential failures.
PROFIsafe
The AC500-S makes use of multiple controller to controller communications via PROFINET/PROFIsafe. PROFIsafe enables functionally safe communication between a safe controller and safe end-devices (eg, emergency stop buttons or drives with safety functions). PROFIsafe is a software layer that sits on top of PROFINET to provide functional safety in PROFINET or PROFIBUS networks →03.
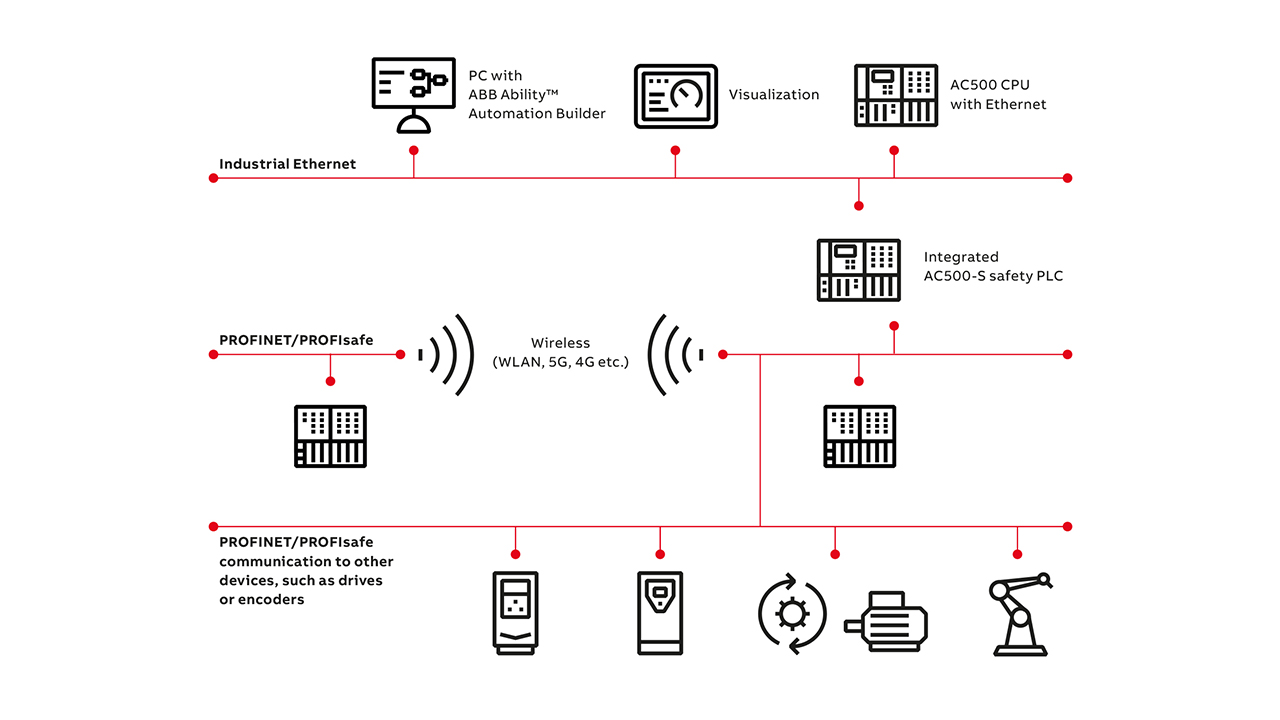
A recent development is that the AC500-S supports PROFIsafe V2.6 (all data types) and long frames (up to 123 bytes of safety data in one frame) for data exchange. PROFIsafe long frames allow the exchange of large amounts of fail-safe data in addition to small frames (up to 13 bytes of safety data in one frame). This advance represents an addition to existing controller-to-controller communication and shortens safety CPU cycle time due to fewer PROFIsafe instances in the safety program for failsafe data exchange. In the future, OPC UA Safety will be supported in addition to PROFIsafe →04. OPC UA Safety is an independent standard for safe communication between controllers, especially those made by different manufacturers. PROFIsafe long frames and OPC UA Safety are of particular advantage to modular machines, AGVs →05, 06, autonomous moving robots (AMRs) or tool changers.
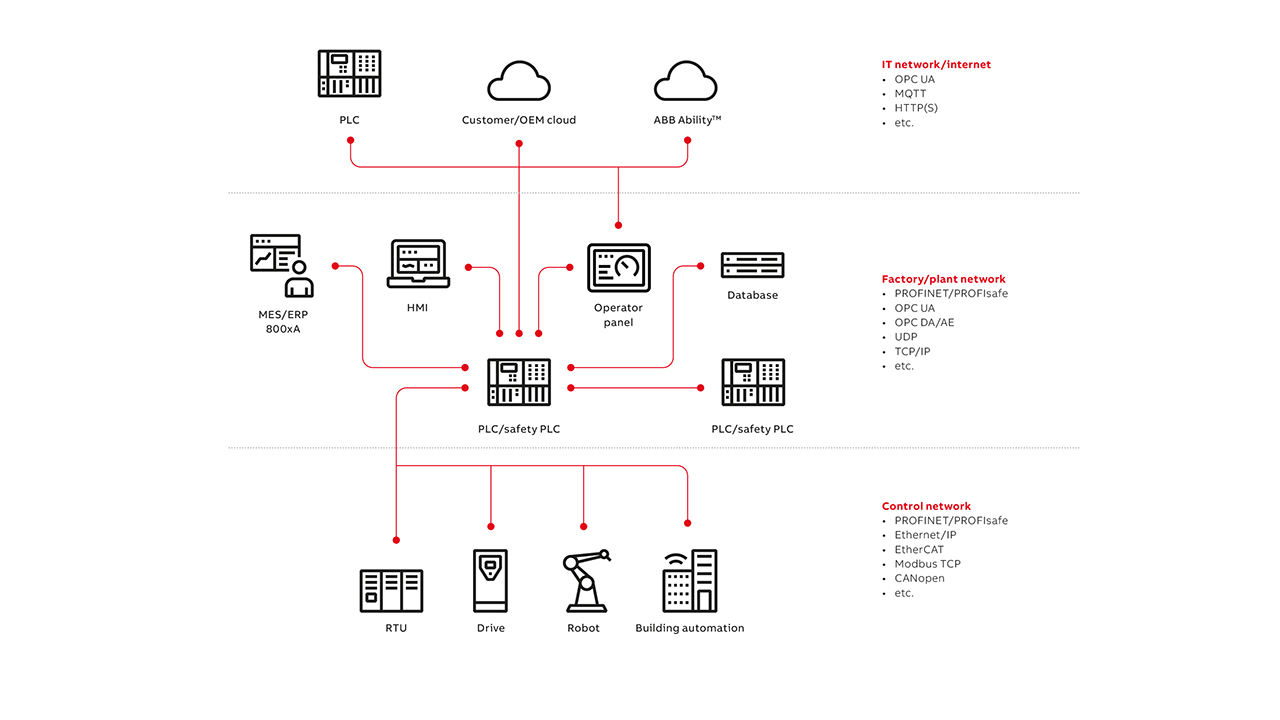
ABB Ability™ Automation Builder
Interconnectivity such as that shown in →03 is supported by one common engineering platform – Automation Builder. Automation Builder is an integrated software suite for machine builders and system integrators to automate their machines and systems in a productive way. Combining the tools required for configuring, programming, debugging and maintaining automation projects, Automation Builder addresses the most significant single cost element of most of today’s industrial automation projects: time spent working with software.
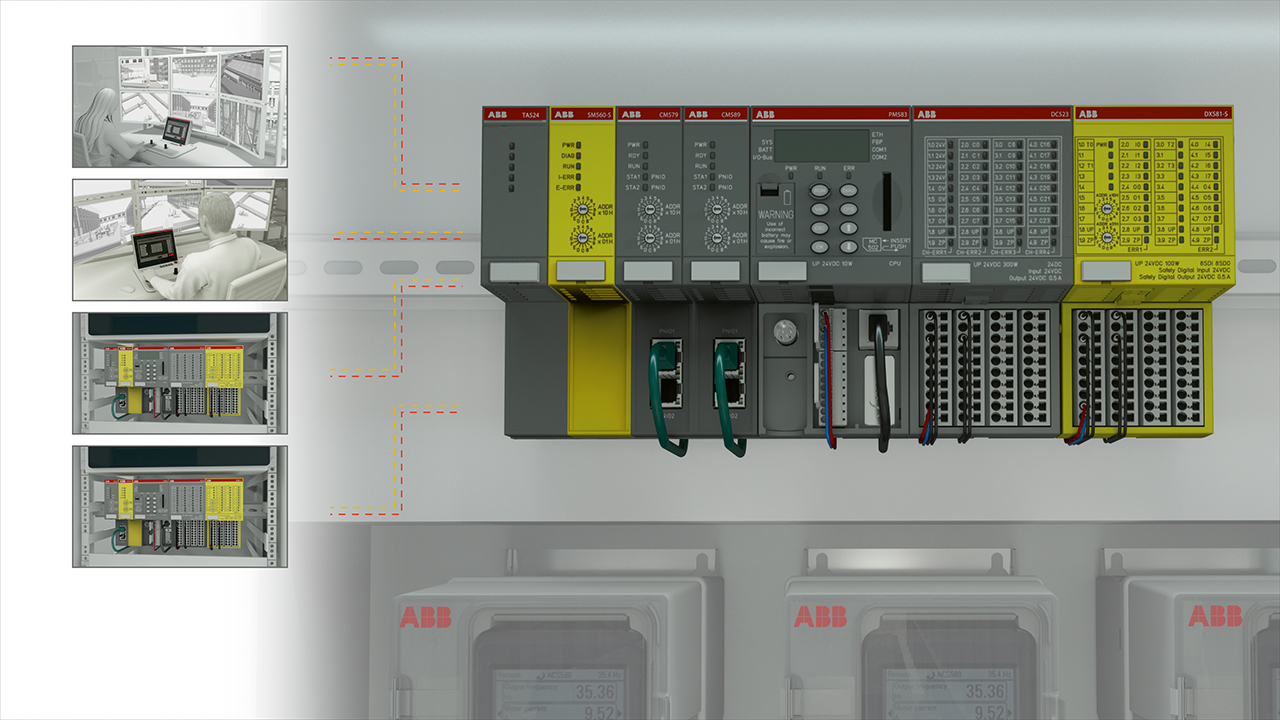
A project using wireless connectivity with 5G is shown in →06. The many advantages of 5G, such as fast reaction times and high device density, can be leveraged to allow real-time PROFINET communication with mobile machines.
PROFINET names and PROFIsafe addresses on the machine and operator levels in →06 can be changed using hardware address switches on PLC modules. Thus, the same PLC boot project can be used for similar machines and operator control setups, significantly reducing development and maintenance engineering effort.
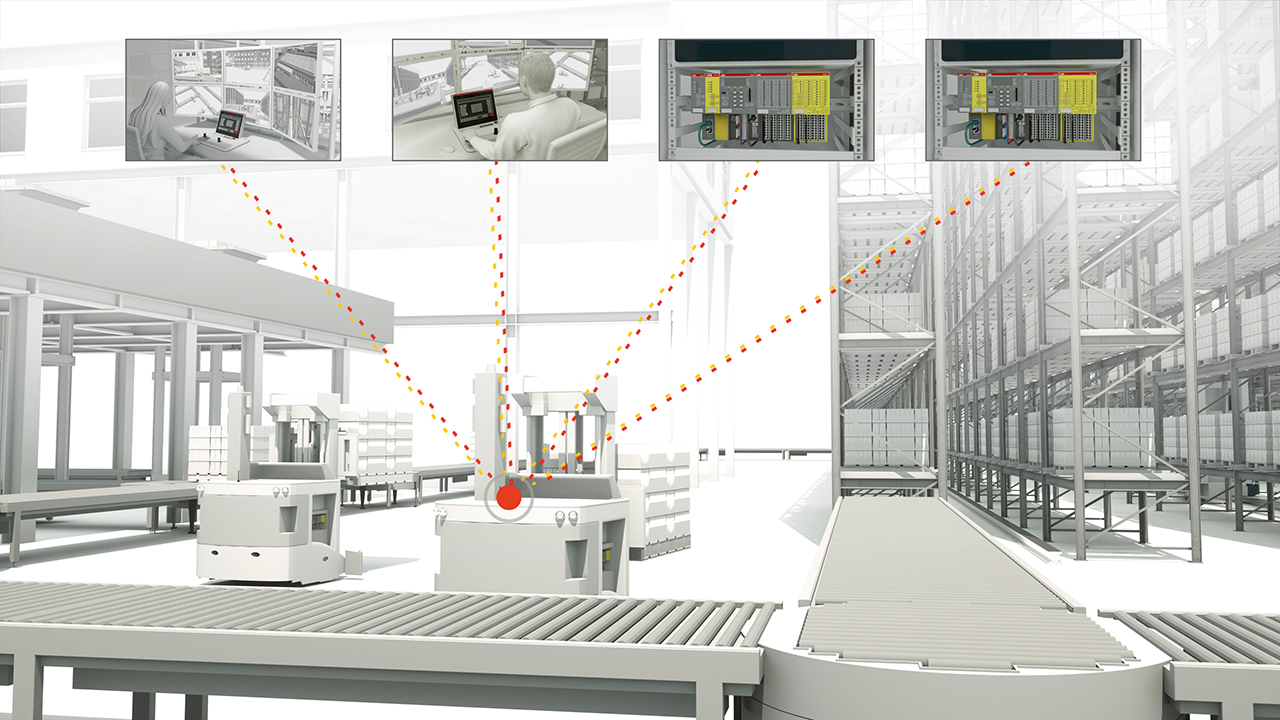
ABB drives offer integrated safety
The flexibility and capability of the AC500-S are reinforced by industrial drives, general-purpose drives and machinery drives that can be fitted with optional safety function modules that achieve up to SIL 3 / PL e. These modules make PROFIsafe communication between the drive and the AC500-S possible via PROFINET. All drives have hardwired Safe Torque Off (STO) built-in as standard.
The FSPS-21 PROFIsafe safety functions module, for instance, is ideal for applications where only STO or Safe Stop 1 Time Controlled (SS1-t) safety functions are required. The FSPS-21 removes the need for cabling for hardwired STO as the functionality can be requested from the AC500-S over PROFIsafe. Setting up the FSPS-21 is simple due to the functionality of the module (only STO and SS1-t functions are available).
The FSO-12 safety functions module enables speed-based safety functions like Safely Limited Speed (SLS), including variable SLS, Safe Maximum Speed (SMS) and Safe Stop 1 Ramp Monitored (SS1-r). Additionally, the FSO-12 module reports the failsafe speed value over PROFIsafe for use in the AC500-S safety program. The FSO-12 safety functionality is implemented without the need to attach an external encoder for applications without external active loads (eg, hanging loads). For hanging loads – for instance, in hoisting operations – FSO-21 and FSE-31 modules, together with a safety encoder, are required.
Safer, greener and more productive with the AC500-S
The AC500-S safety PLC fulfills the highest performance requirements in machinery and process safety and delivers quality and conformity with TÜV-certified components and tools.
With its advanced functional safety solutions for safe position detection (eg, for collision avoidance) and variable safely limited speed, acceleration, deceleration, etc., the PLC keeps the process running at optimal speed instead of stopping or slowing it and opens the door to significant throughput and productivity improvements.
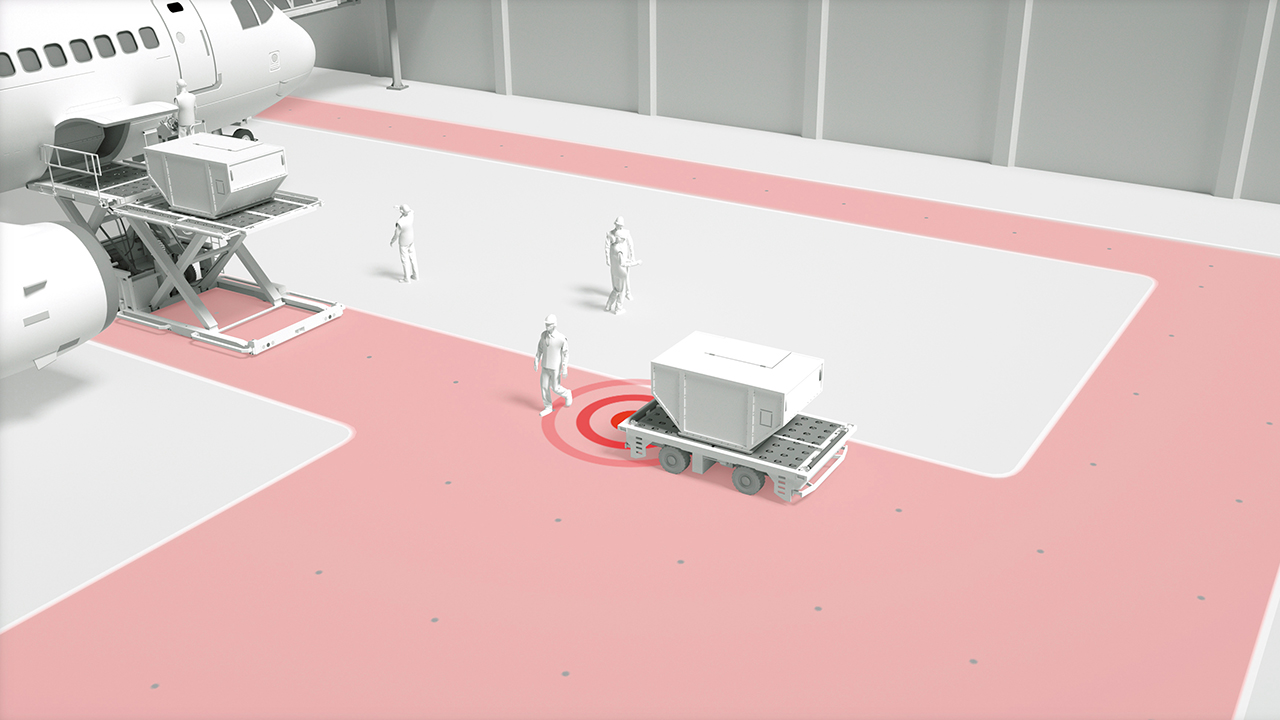
The AC500-S enables safe communication between machines, AGVs and other objects – such as gates, robots, or electrical charging equipment – in shared working areas and thus reduces downtimes →07 – 08. The PLC’s safe remote control ability – coupled with a safety human-machine interface (HMI) and advanced security properties – is convenient for renewable installations, for instance, as many of these are in remote locations.
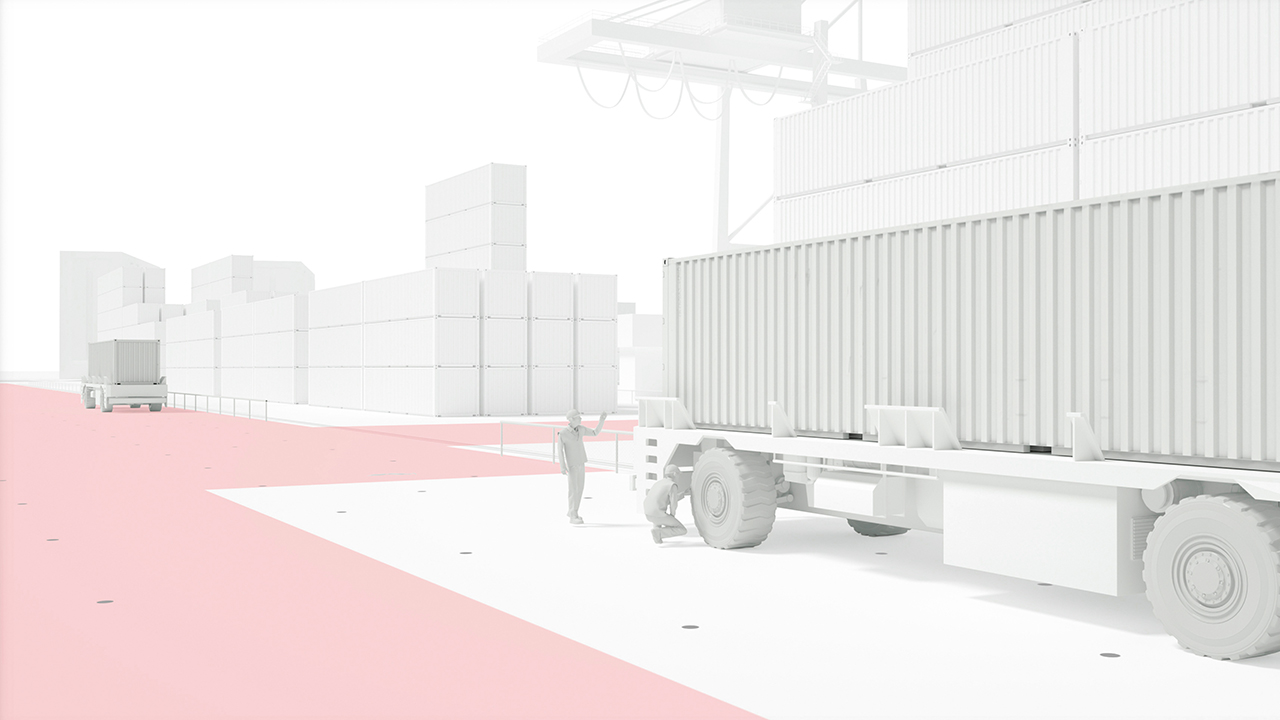
With a design that is flexible, modular and scalable, development times are short and the AC500 can be quickly configured or dynamically adapted to new production demands, such as a change in the number of machines. Teamed with PROFINET/PROFIsafe communications, the comprehensive capabilities of the ABB AC500-S safety PLC provide operators with the best tool to reduce automation solution development time, maximize productivity and optimize costs.
References
[1] ABB, “Safer, greener and more productive with AC500-S safety PLC.” Available: https://new.abb.com/plc/plc-technology/ac500-plc-applications/safer-greener-and-more-productive-with-ac500-s-safety-plc [Accessed February 16, 2022].
Title photo: ©VanderWolf Images/stock.adobe.com