Optimak is a leading Turkish machinery manufacturer with headquarters located in the city of Sakarya, which is about 150 km east of Istanbul. The company was founded in 2012 and now has grown to include over 160 employees. The rate of growth has been fast, and especially remarkable during the past three years, with turnover rising by an impressive 800% during this period.
Optimak is specialized in making end-of-line packaged food handling machinery, mainly for the food and beverage industry, with its product line including conveyors, palletizers, stretch wrappers, vertical elevating lifts and turnkey packing and filling solutions. These are used for conveying and handling products such as sunflower oil, canned goods, juice, bottled water, packaged pasta, and many others. About 80% of the company’s machines are sold within Turkey, with the remaining 20% being exported.
According to Mr. Tansel Cavit Kulak, the founder and owner of Optimak, “superior reliability, productivity and safety are the main factors that we at Optimak focus on when designing and building our equipment. To achieve this, a major difference we have compared to our competitors is our R&D Department that has 60 engineers, who are all seeking to provide the best technology to our customers.”
ABB drive was interesting to us
One of those technologies that fits very well into Optimak’s philosophy of finding the best is the ABB ACS380 machinery drive, which Optimak first began using a couple of years ago. Mr. Kulak explains that although the company and the engineers were relatively happy with the old drive that was then being used in the Optimak machinery, they were curious when ABB wanted to present new drives technology that had the possibility to provide some important benefits.
“So in 2019 we met with the ABB drives people, as they visited us a couple times and introduced their solutions,” explains Mr. Kulak. “We really were not planning to change our automation systems since they were pretty well fixed and most of our customer specifications did not require ABB. However, after some discussions and pilot trials in our R&D facility we realized that there could be significant benefits, due to features like adaptive programming and the wide range of fieldbus communications possibilities.”
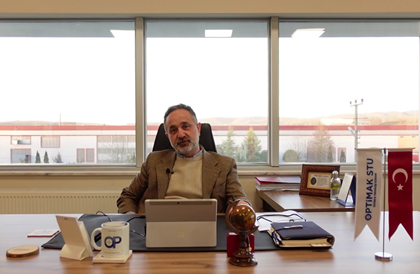
Further talks were undertaken with the Optimak commissioning team, to get their input. They too liked the idea of adopting the ABB ACS380 drives. “The commissioning team found them to be easy to use, and it was simple to make the transition from the previous equipment we were using. Since we started installing these drives, everything has worked well, so we are very thankful to the ABB team for introducing them to us. And from our customers’ viewpoint, we are quite happy about the positive feedback we have received from them as well.”
ABB drive was interesting to us
Samet Zengin, ABB’s sales specialist in Turkey, presents some additional background about the change. “Compared to the variable speed drive (VSD) technology they were previously using, the ABB ACS380 machinery drives are more fit-for-purpose. The other drive was overengineered for this kind of application. The compact ACS380 features excellent vertical axis performance which is very important, and it has the exact built-in application functionalities needed, including mechanical brake control, limit switching and Safe Torque Off (STO) to help meet safety design standards. In addition, it connects seamlessly via Modbus RTU, Profinet or Profibus to the automation systems at the food and beverage customer’s sites.”
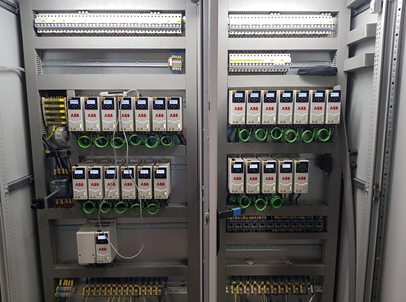
The local ABB Value Provider, ADS, delivered a turnkey solution to Optimak that included the mounting of the ACS380 machinery drive compactly inside the cabinet and all the related electrification solutions.