Domtar, part of the Paper Excellence Group, designs and manufactures a wide variety of communication, specialty and packaging papers, market pulp and airlaid nonwovens. The company’s Marlboro paper mill, located in Bennettsville, South Carolina, USA, has been in operation since 1990 and became part of Domtar in 2007. The mill supports 300 jobs as one of the largest employers in Marlboro County, South Carolina, producing pulp and paper for a wide product range including copy, tablet, receipt and lottery paper. As the last greenfield mill built in the U.S., the facility generates enough green power to supply renewable energy to 30,000 homes in the state. Domtar’s Marlboro mill has been recognized by the Forest Stewardship Council and the Sustainability Forestry Initiative and has received a Programme for the Endorsement of Forest Certification. With one fiber line and one paper line, the mill has 320,000 air dry metric tons annual capacity and 274,000 short tons paper production annual capacity.
Image currently unavailable
Image currently unavailable
Image currently unavailable
Image currently unavailable
Image currently unavailable
Image currently unavailable
Baldor-Reliance® V*S Master inverter duty and vector duty AC motors are designed to provide full load torque continuously from zero to base speed making them ideal for variable speed applications. The motors are built in NEMA frames for drop-in replacement and new applications.
Shortly after becoming a part of Domtar, mill officials determined that they needed to invest in new technology to move the mill forward to stay abreast of emerging environmental regulations and application processes. This decision meant converting existing DC motors and drives to AC technology. The cost of rebuilding DC motors and the ongoing cost of motor brush maintenance also contributed to the decision to make the switch.
Domtar’s engineers researched several motor manufacturers, and selected ABB’s Baldor-Reliance motors because of their reputation for quality and the level of support provided by ABB’s sales and engineering teams. ABB’s engineers worked closely with mill engineers to understand the facility’s needs and provide details about the options available prior to any purchase commitments being made. The ABB team visited the mill on several occasions, studied the application requirements and made recommendations for an engineered solution.
With the decision made to purchase Baldor-Reliance motors, ABB design engineers worked with Marlboro mill engineers throughout the specification and build process to ensure the needs of the customer were met every step of the way. ABB provided engineering drawings early in the process so Domtar could make any adjustments to machinery well in advance of the delivery of the motors.
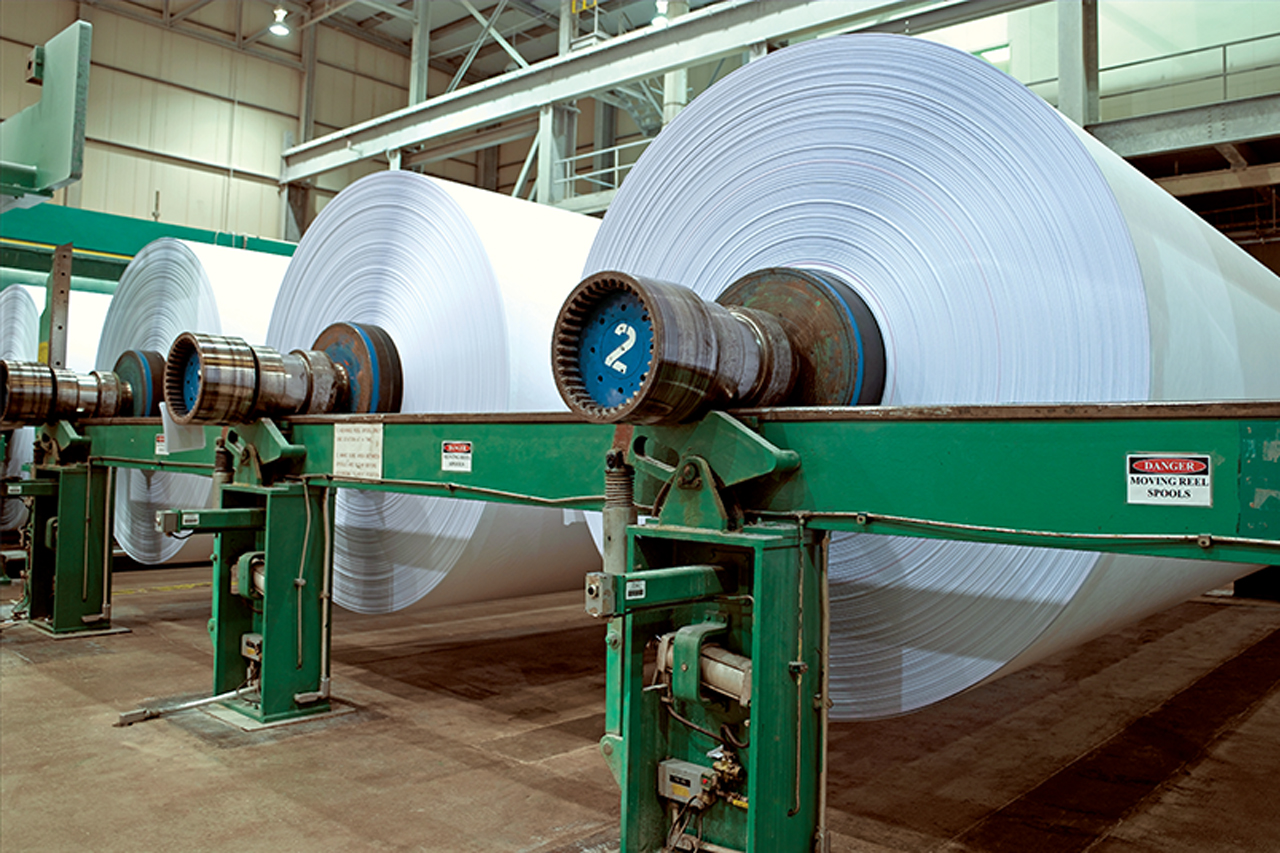
Among the 12 Baldor-Reliance motors purchased by the Marlboro mill were eight V*S Master AC motors, from 20 to 800 horsepower, which were installed on the dryer section of the paper machine. These motors power critical applications, and any motor failure would stop the paper-making process, costing the mill a significant amount in lost production. Domtar representatives have stated that the mill has gotten the results they expected from ABB’s Baldor-Reliance motors, with no start-up, performance or reliability issues.