When Hutchison Ports Stockholm established their new container terminal to the south of the Swedish capital, as part of their strategy to ‘build for the future’ they installed two of the world’s biggest quay cranes equipped with automation and remote operations technology from ABB. The technology provides the reliability, predictability, and consistency terminal operators are looking for in a fiercely competitive market.
Hutchison Ports is an international ports operator with 52 container terminals in 26 countries. Its new Stockholm Norvik Port in Sweden features a natural deep-water draught right on the Baltic coast, with its proximity to the fastest-growing area in Scandinavia providing huge business opportunities.
“Compared to many of Hutchison Ports’ container terminals around the world, today’s operation in Stockholm is a bit smaller, but at the same time we are building for the future with capacity to grow,” says Lawrence Yam, CEO of Hutchison Ports Stockholm.
Image currently unavailable
Image currently unavailable
Image currently unavailable
Image currently unavailable
Image currently unavailable
Image currently unavailable
Lawrence Yam, CEO of Hutchison Ports Stockholm: “I think the demand and needs of customers are pretty consistent. Whether you’re a small port or big port, everyone is looking for reliability and speed in operations, and they want the biggest crane to serve them easily. That’s why we went for the best solution going.” The terminal in Norvik, south of Stockholm, has natural deep-water draught and easy access to the Baltic sea
The Norvik terminal currently has capacity of 250,000 TEU, with potential to double that to 500,000 TEU. Quay operations are carried out by two of the world’s biggest quay cranes featuring automation and remote-control technology that provides optimal efficiency for customers. Being a greenfield development, Hutchison Ports was able to design the entire workflow from ship to gate, including on-dock rail services for handover to the onward supply chain.
“The terminal has now been operational for about two years and is progressing towards being the first fully automated terminal in Sweden,” says Andy Lewis, Head of Operations, Engineering and Automation at Hutchison Ports Stockholm.
Automation brings big benefits
Ports of Stockholm and Hutchison Ports Stockholm set out to create a state-of-the-art terminal with technology and equipment designed for superior reliability and low carbon footprint. ‘Machine-friendly’ automation is part and parcel of this ambition and ideally suited to a terminal of this size, enabling smoother operations with less risk of damage to equipment and goods. While load and discharge processes are pretty much identical regardless of terminal size, smaller terminals generally require more operational flexibility given the many different sizes of vessels they accommodate. At Norvik the quay cranes serve vessels ranging from small barges up to ships 22 wide.
Workplace experience is another important factor in addition to flexibility. At Norvik, Hutchison Ports Stockholm’s highly competent stevedores are rotated through all parts of the container flow, acting as multifunctional operatives handling the full spectrum of terminal equipment.
Under such conditions, automation helps turn challenges into opportunities.
“With the assistance crane operators get from automation, we are able to achieve both operational stability and consistency, which makes operations more predictable,” says Lewis.
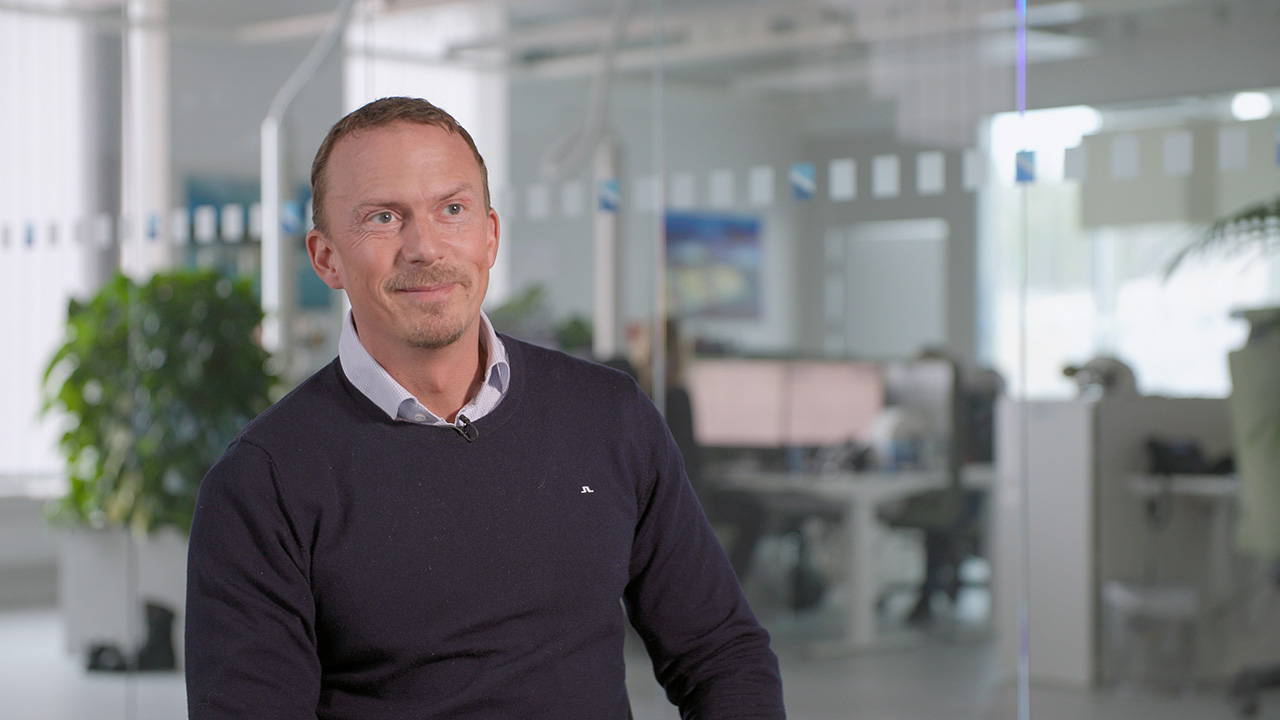
Remote operations boost efficiency, safety, and operator wellbeing
Implementing the latest technology can be a huge benefit for container terminals given the current strain on supply chains due to labor shortages, bottlenecks, and low predictability in liner services. Regardless of the experience and proficiency of individual operators, automation combined with remote operations capability means cranes can perform consistently, running faster with shorter cycle and ramp times.
Remote operations improve overall operator performance primarily through extending visibility with multiple camera views. As container ships have become bigger so have ship-to-shore (STS) cranes, and especially on larger cranes the ability of the human eye is limited by the physical distance between the cabin and the target.
“The biggest difference is the camera angles. They zoom in on the container and we can see big angles all around the ship, and the screens show us everything we need to see around the quay crane. It helps me as a driver to do the work more efficiently as well as enhance the safety of my co-workers,” says Linus Gellborn, a crane operator at Norvik.
Remote operations also serve to improve the working environment for crane operators by physically removing them off the giant machines into the safety and comfort of a control room. The control room also enables a more versatile workplace.
Image currently unavailable
Image currently unavailable
Image currently unavailable
Image currently unavailable
Image currently unavailable
Image currently unavailable
Image currently unavailable
Image currently unavailable
Image currently unavailable
Linus Gellborn, crane operator at Hutchison Ports Stockholm: “I enjoy driving with remote control much more than I thought I would. It’s better for my body and I see the benefit in having my colleagues near me whenever I need them.” Remote crane operator in the comfort of a control room with easy access to colleagues The remote operator workplace with camera views and process panel
“It’s much easier to take a longer run when you drive the crane with remote operation because it isn’t so exhausting. Being physically in the crane cabin can be uncomfortable and you can’t move around in the same way as you can when operating the crane remotely,” says Gellborn.
“The switch to remote control has been much easier than we thought given that a lot of our operators previously worked with conventional container cranes. Using top-of-the-line technology and automation really makes the job more interesting,” Lewis adds.
Proven concepts for fast commissioning
ABB has been developing crane automation solutions for decades and has been a pioneer in remote operations for container handling in pursuit of greater reliability and efficiency. Although every new project is unique, ABB's combined experience from hundreds of terminal installations means projects are started off with a robust base of technology solutions and setups that can be adapted to customers’ specific needs.
This was especially relevant for Hutchison Ports Stockholm when it set about building a brand-new terminal.
“ABB brings a lot of pre-made, proven solutions to the table, which made the fast commissioning and integration of automation here at Norvik possible,” Lewis concludes.
About Hutchison Ports Stockholm
The Hutchison Ports container terminal in Norvik, south of Stockholm, is a completely new container terminal established in the Baltic Sea. It’s the only deep-water container terminal on Sweden’s east coast with fast connections to all important harbors in the Baltic Sea and with close access to the greater Stockholm area. It opened for operations in 2020.