Richard Daumas ABB Food and Beverage Beynost, France, richard.daumas@fr.abb.com
The investments in production equipment made each year by food and beverage producers are substantial. Often, these acquisitions have to be customized to suit the particular requirements of a production line, which can further increase cost and complexity. However, for production lines large or small, complex or simple, two important factors influence the choice of equipment: safety and the need to comply with increasingly strict regulatory requirements that apply across the entire value chain, from the raw material to the finished product. These factors can be successfully addressed by ABB smart manufacturing solutions – for instance, an integrated control system that covers the entire production process, combined with ABB low-voltage components and B&R X20 programmable logic controllers (PLCs) →01 – 02.
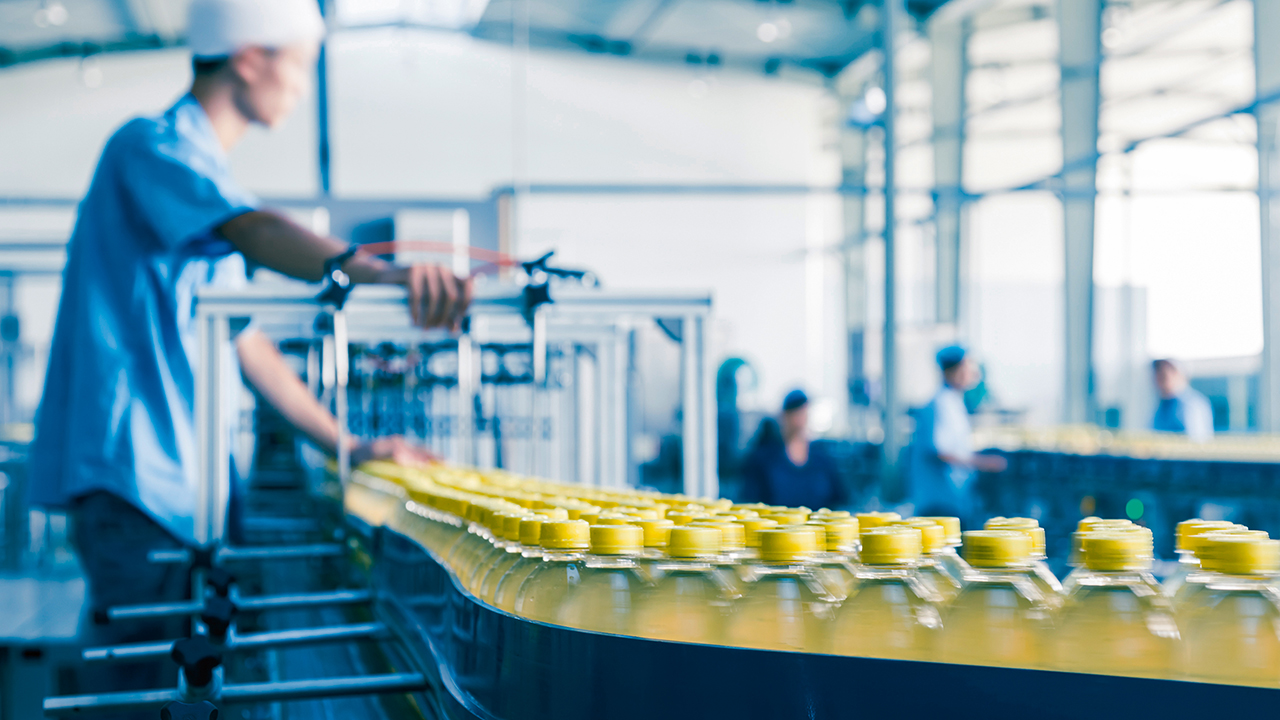
Smart safety from ABB
If incorrectly managed, a food and beverage production facility can present health and safety challenges as machinery, chemicals, spillages, dust, etc., can pose potential hazards. For these facilities, ABB offers a combination of solutions to manage machine automation and safety, from the simplest to the most complex setup:
• Small machines and simple safety applications
• Standalone safety independent from the control platform
• Complete production lines with factory-wide integrated automation and safety
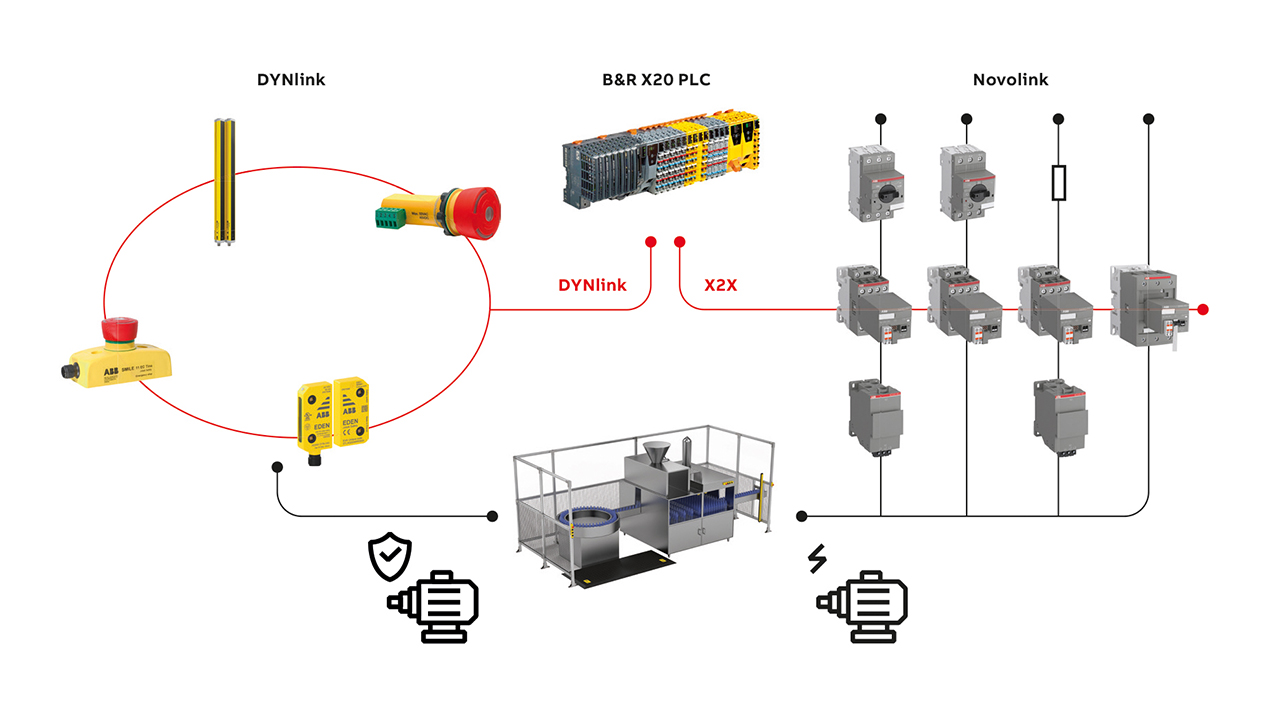
ABB relays and controllers for safety
For the simplest safety system, with only a few I/Os and limited requirements, standard safety relays are adequate. The Sentry series of safety relays from ABB is widely used in these cases. The Sentry has an economical and straightforward design and can be put to use immediately since setup is easy and no programming is needed.
When a larger number of safety sensors and I/Os are needed, or if more advanced functions are required, particularly in terms of communication with the PLC, programmable safety controllers are a good choice. An example of such a controller is ABB’s Pluto, which can be directly connected to the most commonly used safety equipment. Pluto is a powerful standalone safety controller that comes with free programming software and is simple to use.
PLC control systems with integrated safety are used for the most complex situations. These systems are versatile and offer the same number of safety functions as safety controllers. Because both machine control and safety functions are performed in the same PLC, reliable intercommunication between these two features is facilitated and the entire configuration can be executed in a consistent programming environment. Moreover, the advanced diagnostic facilities available in these PLCs help engineers and end-users in their everyday work. The B&R X20 system is a highly capable and compact example of such a PLC that has integrated safety and proven compatibility with ABB safety sensors →03.
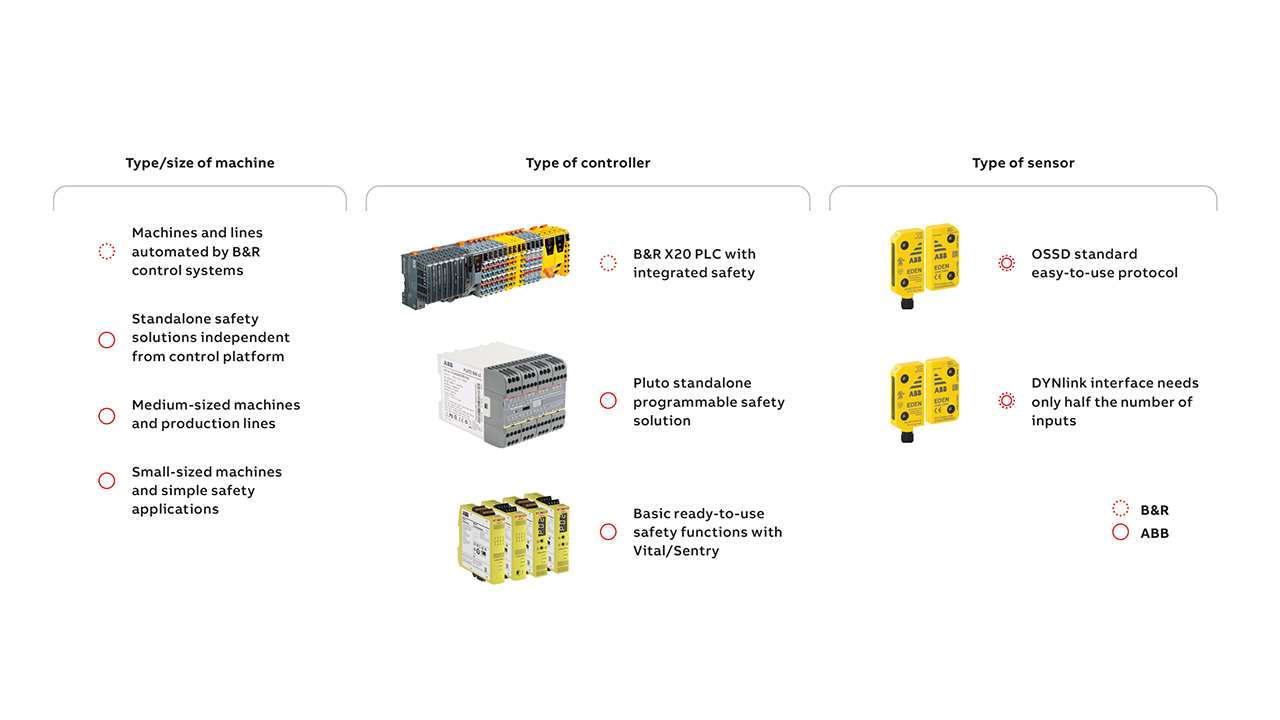
Communication interfaces
In the sometimes harsh environment of a food and beverage plant, robust communications are essential if safety is to be maintained and data relating to compliance with regulatory requirements is to remain secure. If compliance data is lost, traceability can be lost and facility certification jeopardized. ABB offers two communication interfaces that reliably connect safety sensors to safety controllers: OSSD and DYNlink →03.
The OSSD communication protocol is widely used for different types of safety sensors. OSSD enables the connection of multiple sensors in series while maintaining a high level of safety. Most safety controllers on the market (including ABB’s Sentry and Pluto, and the B&R X20) can connect to and monitor OSSD-based sensors.
DYNlink is a communication protocol unique to ABB. It is a sensor communication and cabling approach that attains the highest level of safety using the minimum number of cables and controller inputs. DYNlink is compatible with ABB’s Vital and Pluto controllers and the B&R X20.
Compared to OSSD, DYNlink requires only half the number of inputs, while still maintaining the highest safety level in serial connections. Furthermore, DYNlink also enables add-on functions, such as StatusBus, to get status information from each sensor without adding any extra wires. For example, using just one of the existing leads in an M12-5 cable, StatusBus can keep track of the status of all devices connected in series. This feature provides a cost-effective way to monitor the status of doors, emergency stop buttons, etc.
ABB Novolink™ devices digitalize industrial electric motors
Motor starters are ubiquitous in food and beverage facilities. Often, however, these essential production line elements are not intelligent. This situation can be remedied by ABB Novolink modules, which digitalize motor starters to gain insights into the connected loads and maintain a safe working environment. The modules are easy to design into existing wiring plans and they simply snap onto any AF contactor. Engineering efforts are minimized thanks to reduced wiring and fewer components compared to traditional methods of retroactive digitalization.
Novolink modules connect electric motors into higher-level automation and smart manufacturing systems, giving customers the real-time data and analytics they need to implement energy-saving strategies and operate safely. The modules enable the predictive maintenance, remote control, fault diagnostics and data analytics required for the world of Industry 4.0.
There are two Novolink modules: the SFM1 and the SCV10. The SFM1 Novolink contactor module monitors key maintenance statistics, including motor operating hours, contactor switching cycles and trips.
The SCV10 Novolink current and voltage module provides motor protection and monitors the status of connected equipment. This module connects to the SFM1 module and measures line voltages, phase currents, power, frequency, total harmonic distortion and other important parameters. The SCV10 uses a ribbon cable to connect via an X2X port to the SFM1, from which it draws its power. The SCV10 module also offers thermal overload protection according to IEC/EN 60947 for single- and three-phase induction motors. The device also integrates current transformers that measure up to 40 A nominal current and voltage up to 690 V AC.
Novolink modules are compatible with 24 V DC coil contactors – from AF09 up to AF96 in screw versions and from AF09 up to AF38 in push-in spring versions. ABB’s AF contactors have an advanced, electronically controlled magnet system that covers the complete power range and are complemented by a full list of accessories. Novolink modules can be connected in a daisy chain with multiple devices working in sequence using standard Ethernet cables.
The Novolink modules are fully integrated with the B&R automation system and help detect load, supply or feeder issues, thus reducing the time needed for problem-solving.
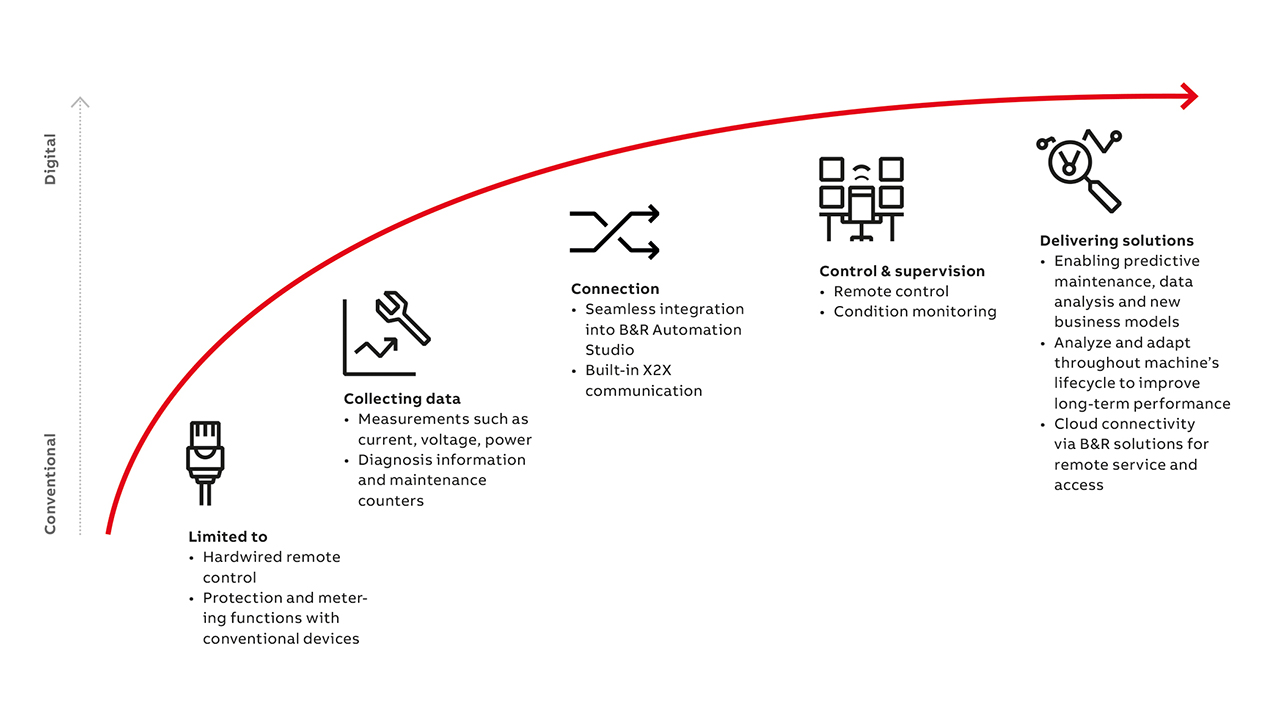
The future lies with smart manufacturing
The migration from the traditional world to the new world of digitalization and smart and safe manufacturing results in shorter installation times, simplified engineering and preventive maintenance that is easy to implement. Measurements of principal parameters – such as current, voltage, power and energy consumption – are complemented by a wealth of diagnostic information. The solutions described in this article benefit from full compatibility with B&R Automation Studio (a software development environment) and B&R’s integrated safety technology →04 – 05. Connectivity via B&R solutions facilitates remote access and service. It is now easier than ever to implement safety concepts with either OSSD or DYNlink communication protocols to allow customers to enhance safety, benefit from more flexibility in their production lines and be assured they adhere to regulatory requirements.
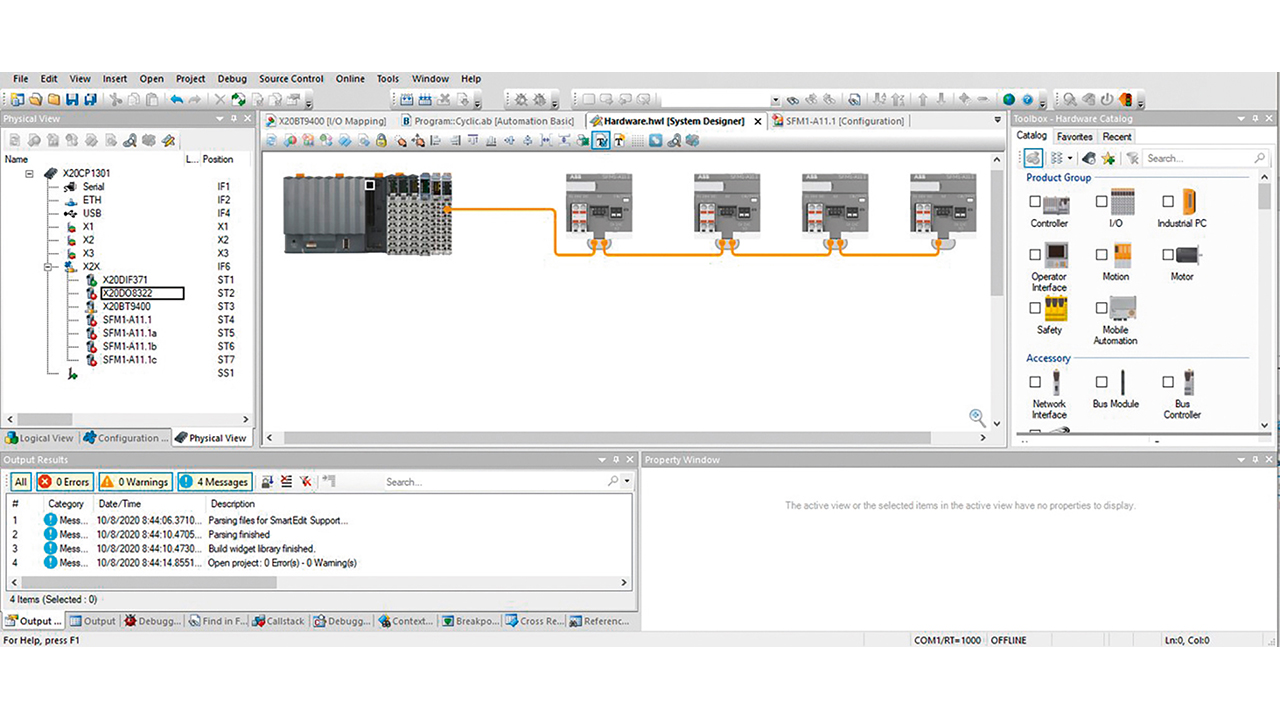