The global steel industry is one of the most energy hungry industrial sectors and a significant producer of CO2 emissions, making it imperative to ensure that production processes are running at their optimum.
It is vitally important that production errors during the manufacturing process are minimized as far as possible to avoid costly wastage and reworking of spoiled products. In steel rolling applications, ensuring accurate measurement of metal flatness during the rolling process can make a major contribution to eliminating wasted product.
An ABB measurement solution has helped a major metals producer to ensure consistent product quality through accurate control of metal flatness throughout the steel rolling process.

Steel producer Outokumpu is one of the world’s largest producers of stainless-steel products including sheet metal and metal strips, wire rods and bars, slabs and ingots. Its products are used worldwide in a wide variety of applications, ranging from construction through to aerospace and automotive.
As the stage at which hard metals are shaped into steel sheets, cold and hot rolling processes are key the metals production process. The need to ensure the highest levels of quality requires close control throughout the rolling process.
"It is vitally important for operators to be able to rely onthe accuracy of flatness control systems in ensuring that metal is rolled to the correct specifications."
When Outokumpu had to replace an obsolete competitor-supplied flatness control system at its Nyby plant in Sweden, ABB was able to provide both the products and expertise needed.
Used in the manufacture of rolled stainless steel strips of varying grades, flatness control systems play a major role in product quality by ensuring that the strips meet the required flatness across their complete production mix.
The mill produces a mix of stainless-steel strips measuring 1000 to 1550 mm wide and 0.35 to 6.0 mm thick.
“It is vitally important for operators to be able to rely on the accuracy of flatness control systems in ensuring that metal is rolled to the correct specifications in terms of thickness and width,” explains Jan Onsten, Account Manager at ABB. “With rolling mill strip speeds typically up to 1000-2000 meters per minute, mistakes arising from in correct control can happen very quickly, potentially resulting in large quantities of rejected material that can have a significant impact on yield.”
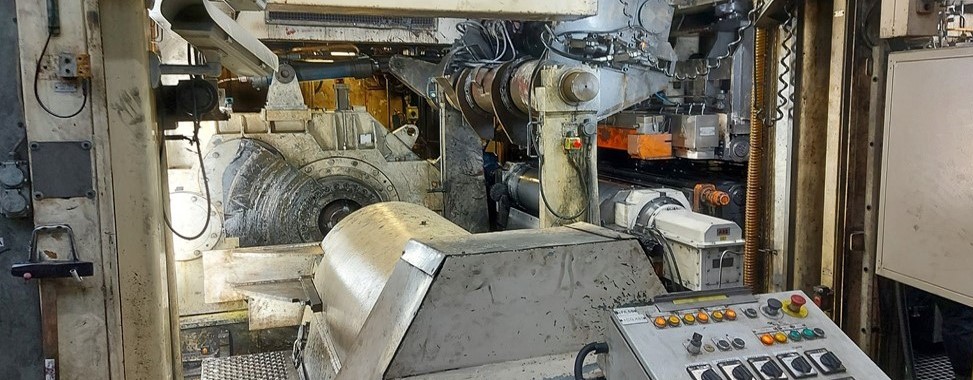
Upgrade solves production issues
The decision to upgrade was prompted by issues with the plant’s old flatness control system. Installed since the mid-1990s, the old system’s rubber coated measurement rolls on the 20-high mill required frequent maintenance due to high levels of wear. To bring them back into service involved removing, recoating and then grinding them. Before being refitted, they also had to be calibrated, incurring further cost and disruption from lost production. The age of the system meant that obtaining spare parts was becoming increasingly difficult and more expensive.
Limitations with the system also meant that it was unable to provide 100 percent control throughout the rolling process, resulting in inconsistent flatness and strip breaks.
As a long-standing ABB customer, Outokumpu made the decision in November 2020 to replace the system with ABB’s Stressometer solution. Featuring ABB’s patented Extended Singular Value Decomposition system (ESVD), the solution has delivered greatly improved flatness control. By optimizing the speed and selection of actuators, ESVD enables fully automatic flatness control with none of the errors and limitations that can affect the performance of traditional control systems.
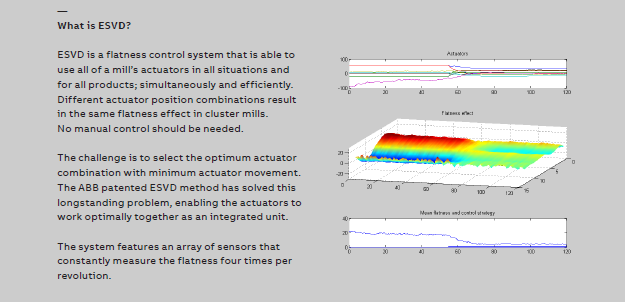
A tough challenge
A major challenge in the upgrade project involved updating the communications between the machine and the flatness control system. With information about the design of the original system being largely unavailable, ABB engineers went to site at the specification stage to record the behavior of the communications system. Using this information, they were able to gain an understanding of how the system worked which then enabled them to develop a solution.
“Knowing what’s happening at all stages of the rolling process is key to achieving the right quality and minimizing errors,” explains Jan Onsten. “It was therefore essential to know how the communications system worked so that we could ensure that the upgraded solution could enable the constant flow of signals and communication with other systems needed to optimize performance.”
“Ideally, this information would be readily available, but in this case, the age of the original system and the lack of available documentation meant we had to choose a different approach. Fortunately, our engineers had the expertise and experience to tackle the challenge.”
Despite the challenges in upgrading the system, ABB was able to complete the project within three days, with some of the preparatory work already done in advance.
“By testing and analyzing our solution in advance we were able to substantially reduce the time needed to carry out the project on site,” explains Jan Onsten. “This enabled us to meet Outokumpu’s tight window for the work to be carried out and ensured that any disruption to production was kept to a minimum.”
Since the solution was installed, reliability has been greatly improved, with downtime considerably reduced and no need to remove the measuring rolls for service or refurbishment.
“We are very pleased with both overall the solution provided by ABB and the approach it took throughout the upgrade project,” says Project Manager, John Lindberg, for Outokumpu. “The engineering team kept us updated at all stages and provided good guidance and support, responding quickly and providing efficient fault tracing and analysis.”
ABB solutions used at the plant
ABB solutionThe following solutions were supplied for this project:
• Stressometer flatness control system(20-high mill with ESVD)
• ABB technical support
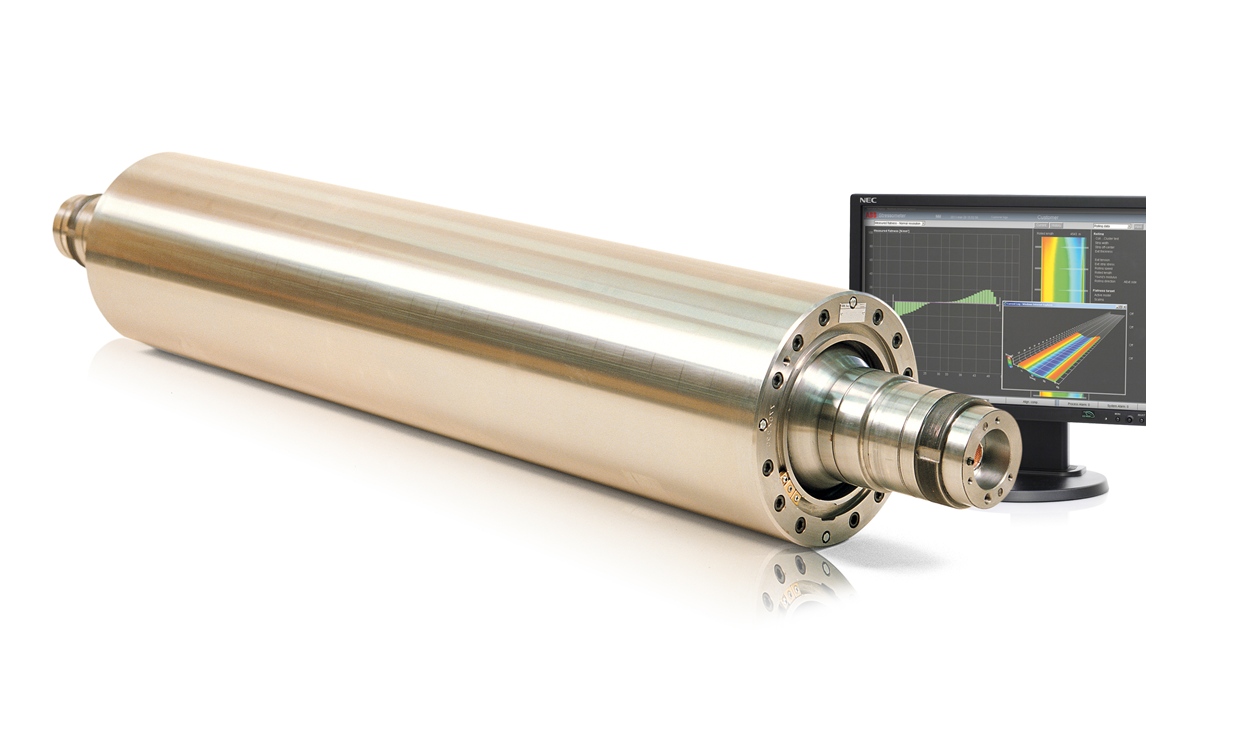