Cutting the amount of wasted steel helps reduce carbon emissions
Steel is one of the most important commodities in the world, used to build a huge number of products and constructions – around 57 tons of steel is produced every second. It is also one of the most polluting industries, with 1.83 tons of CO2 emitted for every ton of steel produced. Ensuring that steel is manufactured effectively and efficiently, avoiding wasted product, ensures that no extra pollution is produced. A Chinese steel mill is using ABB force measurement solutions to ensure it achieves maximum productivity while causing no extra pollution through the need to remake steel.
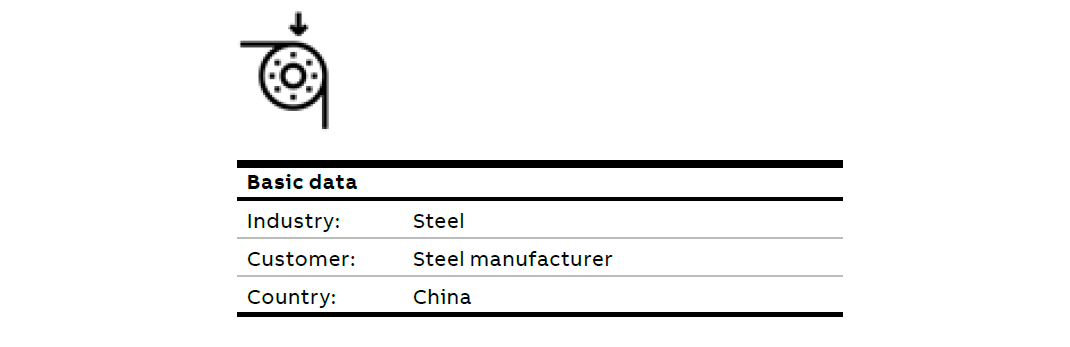
Established in 2016, a major Chinese steel manufacturer produces hot strip rolled steel products. Its products include carbon structural steel, high-quality carbon structural steel, low-alloy high-strength steel, weathering steel, pressure vessel steel, medium and low grade non-oriented silicon steel, high-strength steel for automobile processing, steel for pipelines and marine steel. It currently has an annual production capacity of around 10 million tonnes.
The company’s products are widely used in high-speed train bodies, automobile structural parts, containers, household appliances, hardware, tools and other types of finished goods.
In 2019 the plant installed three new Hot Strip Mill (HSM) production lines, with all the roll force measurement systems supplied by ABB.
The 1780HSM mill has a capacity of 3.5 million tonnes a year and can produce strip ranging from 900 mm to 1630 mm wide.
The two other strip mills, 1450HSM numbers 1 and 2, can both produce three million tonnes of product a year, with strip widths ranging from 900 to 1300 mm wide.
“Using an ABB load cell, the measurement is more stable, more accurate and less susceptible to interference.”
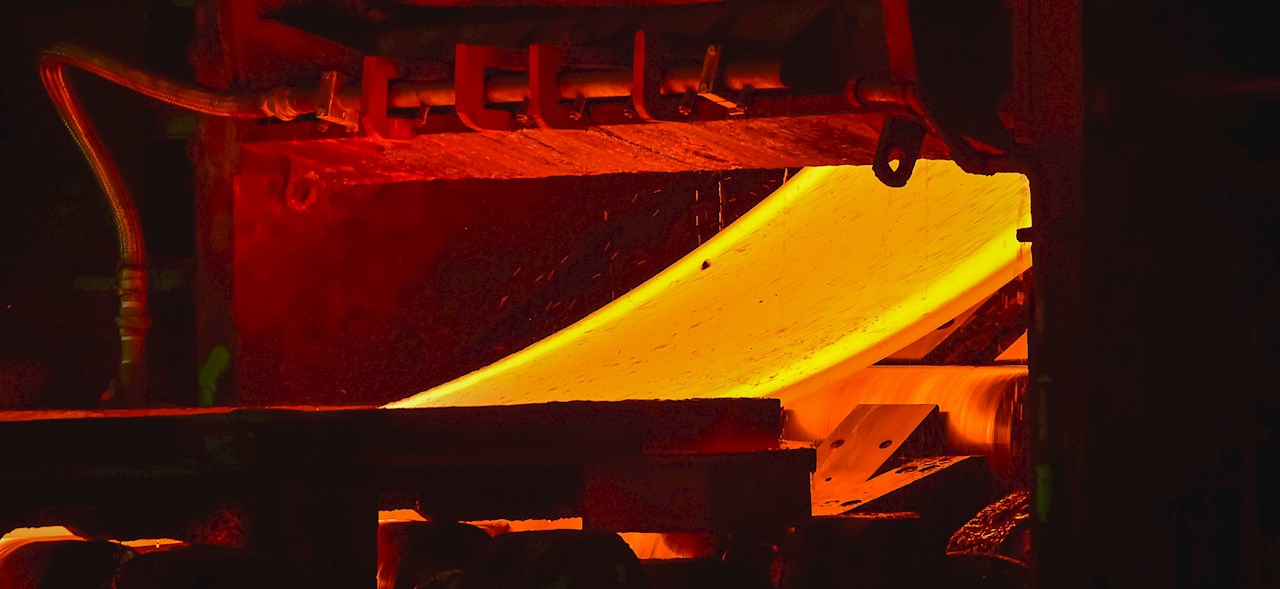
Precision force measurement gives higher quality steel
Measuring roll force of the HSMs can be achieved in two ways, either via an oil pressure sensor, or a load cell.
Oil pressure sensors have several drawbacks, not least the fact that some of the pressure in a hydraulic system has nothing to do with the load being applied – for example, some pressure is needed to raise the piston off the bottom of the cylinder, while the oil itself also exerts pressure.
The plant’s Electrical Director says: “Using an ABB load cell, the measurement is more stable, more accurate and less susceptible to interference. In addition, the response time is faster.
"This gives more precise control of the production line, improves production efficiency, raises product quality, and reduces waste.”
The robustness of the load cells is a critical feature, as all the load cells are installed under the lower backup roll, a very harsh working environment. When the rolling mill is working, there is a lot of water around the load cells to cool the mill rolls during loading. In addition, strong vibration forces mean that water and some oxides can enter the load cell package and be deposited on the surface of the load cells, which could cause uneven force distribution and poor insulation.
The load cells also experience a relatively large rolling force.
ABB’s Millmate roll force system is the perfect choice for measuring roll force in both hot rolling and cold rolling mills, thereby achieving the correct roll gap settings and force distribution.
Key benefits for the customer include:
No calibration required
The system is proven to be exceptionally robust and resilient to high forces as well as aggressive mill agents. The load cells are calibration free, can withstand overloads up to seven times the nominal force, and provide extended lifetime due to being contained in a robust, stainless-steel box. The load cells come in different sizes from 0.1MN up to 60MN.
High accuracy
Due to its low impedance and high output signal power, the Millmate roll force load cell has an extremely low sensitivity to insulation defects and maintains measuring accuracy at insulation levels down to 10 kΩ.
ABB solutions used at the plant
ABB solution
• 54 ABV PFVL141 Millmate Roll Force rectangular load cells with nominal loads ranging from 3.1 to 25MN.
• 12 circular load cells with nominal loads of 3.1 or 4 MN.
