La inteligencia artificial y la robótica: una fórmula para fábricas flexibles
La combinación de inteligencia artificial (lA) y robótica puede mejorar sustancialmente la flexibilidad de la automatización de las fábricas, mediante la sustitución de las aplicaciones rígidas por capacidades de aprendizaje. Con esta potente combinación de tecnologías se pueden ampliar las funciones de los robots, mejorando así la productividad, haciendo el trabajo más seguro y acelerando la producción. La gama de aplicaciones de ABB en este ámbito incluye el uso de la IA para permitir a los robots detectar y responder a su entorno, inspeccionar y analizar defectos, y optimizar los procesos de forma autónoma.
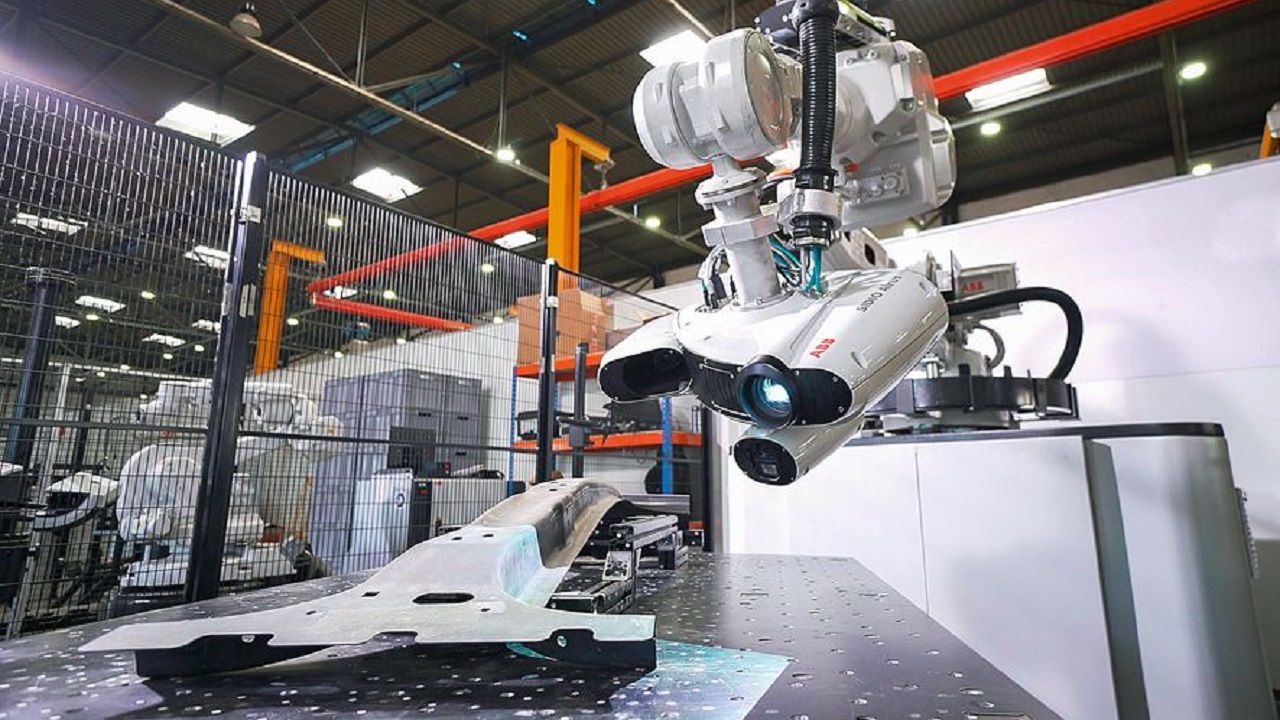
Por ejemplo, los robots equipados con sensores de visión pueden utilizar la IA para identificar objetos independientemente de su posición, mientras que los algoritmos de aprendizaje automático (machine learning) permiten a los robots determinar la mejor trayectoria y las mejores posiciones de agarre para coger objetos. La IA también permite a los robots inspeccionar y analizar una amplia gama de objetos –las costuras de soldadura son un caso concreto (gráfico)– para detectar defectos y problemas de calidad. Esto se logra mediante una combinación de sensores de visión y aprendizaje supervisado, es decir, formación mediante ejemplos.
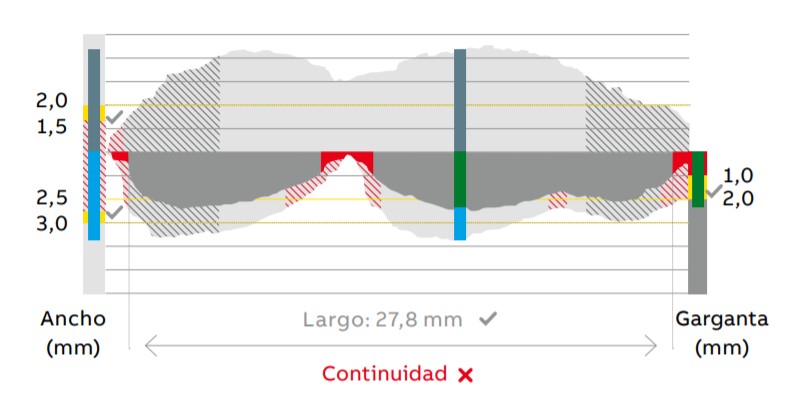
Y cuando se trata de la optimización autónoma de procesos, nada iguala a ABB Ability™ Connected Atomizer, el primer atomizador de pintura robótico, conectado y equipado con sensor, que permite realizar diagnósticos inteligentes en tiempo real y optimizar la calidad de la pintura. Al controlar el estado de variables clave como la aceleración, la presión, la vibración y la temperatura, el atomizador reduce los residuos internos durante los cambios de color en un 75 %, y el consumo de aire comprimido en un 20 %.
ABB también está aplicando algoritmos de IA al análisis del comportamiento de las prensas y los robots en las líneas de prensado y estampado para minimizar los tiempos de espera de los equipos. Mediante la adopción de un enfoque holístico, un algoritmo de control identifica cuellos de botella y gestiona los tiempos de arranque y parada de robots y prensas, haciendo así las líneas más estables y predecibles.
Robots: con la vista puesta en las cadenas finales de montaje de automóviles
Las plantas de producción de vehículos suelen dar una imagen de automatización avanzada, con líneas de robots soldando una carrocería tras otra. Pero no todos los aspectos de la fabricación de vehículos están tan avanzados tecnológicamente. El montaje final es un ejemplo claro. En este caso, la complejidad de procesos como el cableado, la instalación de asientos y la inserción del puesto de conducción exigen unas manos diestras.
No obstante, los ingenieros de ABB están desarrollando técnicas que permitirán a los robots realizar una serie de tareas iniciales en este ámbito. Es probable que el aspecto más difícil de tal desafío sea el hecho de que durante el montaje final, las carrocerías de los vehículos se desplazan constantemente en sentido lineal. Para abordar esta dificultad, un robot asociado al proceso se guía por una combinación de sensores visuales y de control de fuerza en tiempo real, en lugar de moverse según una trayectoria programada.
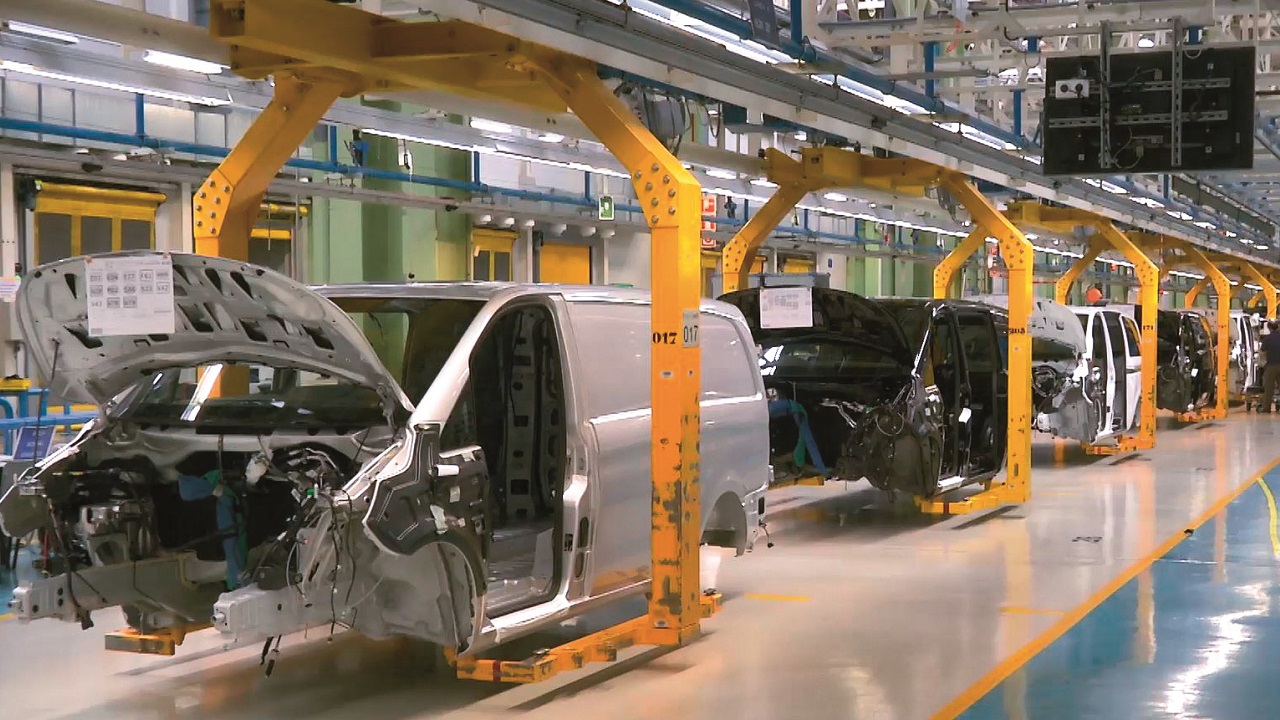
Para completar una tarea de montaje en un entorno tan inestable, el primer paso es que el robot se sincronice con el movimiento lineal de la cadena de montaje. Esto se realiza mediante el seguimiento de cintas transportadoras convencionales o utilizando tecnología de seguimiento AGV (vehículos guiadosautomáticamente). El seguimiento AGV, que también se puede usar en cintas transportadoras convencionales, se basa en el seguimiento visual en tiempo real de códigos de barras bidimensionales de alto rango, conocidos como "AprilTags". Un AprilTag se monta normalmente en el dispositivo equipado con AGV que transporta un vehículo, mientras que la cámara de seguimiento está fija en el suelo o en el pie del robot, cuando el robot está montado en un eje lineal.
Una vez que un robot se ha sincronizado con el movimiento de un vehículo concreto, comienza a realizar una tarea de montaje mientras efectúa un seguimiento continuo de las características naturales del área de montaje en cuestión con una funcionalidad desarrollada por ABB conocida como "Real-Time On-Board Vision", que va instalada en la pinza del robot. La información que ofrece este sistema de visión se combina con los datos de retroalimentación continua suministrados por un sensor de control de fuerza que se instala entre la muñeca y la pinza del robot.
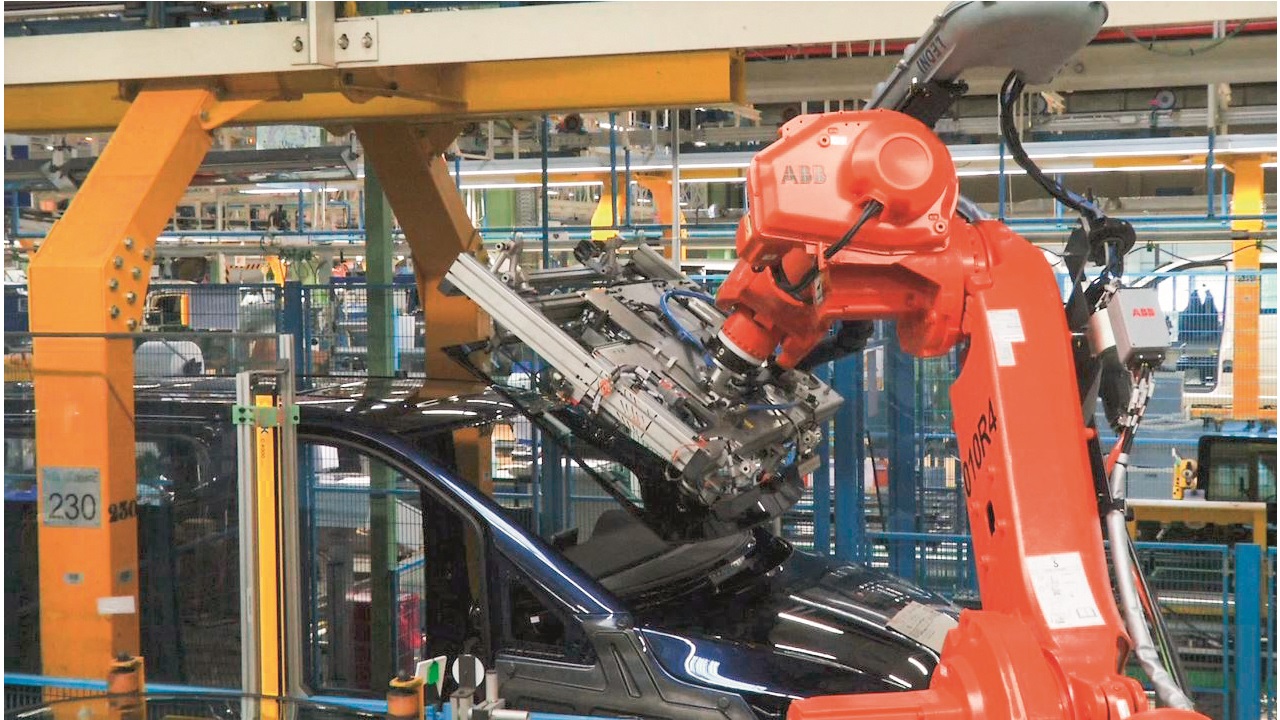
La combinación de la guía de visión a bordo en tiempo real y la manipulación con control de fuerza (fusión de sensor) es la clave para llevar a cabo con éxito un proceso de montaje determinado. Los casos de aplicación pilotos están actualmente en curso, en coordinación con un importante fabricante de automóviles. Por ejemplo, hay plantas alemanas y chinas que realizan en la actualidad operaciones de montaje del puesto de conducción del vehículo. La experiencia adquirida en estas y otras instalaciones es, en potencia, fácilmente aplicable a otros ámbitos del montaje de automóviles, así como a otros entornos de fabricación caracterizados por el continuo movimiento de los elementos objetivo.
ABB amplía la gama de potencias de Azipod para transbordadores y buques Ropax
Desde su lanzamiento en 1990, la propulsión eléctrica Azipod se ha convertido en el punto de referencia del sector para una amplia gama de buques, desde embarcaciones pequeñas hasta rompehielos. En respuesta a las peticiones de los clientes, ABB ha llenado el vacío existente entre los propulsores Azipod de baja y alta potencia con el lanzamiento de una nueva serie disponible en la gama de 7,5 a 14,5 MW. Además de los transbordadores y los buques RoPax (transbordadores de pasajeros de carga rodada), esta gama de potencias también se utiliza para buques de construcción en alta mar, cruceros de tamaño medio y buques "lanzadera". Con esta incorporación, la familia de propulsión Azipod cubre ahora de forma flexible la gama de potencias de 1 a 22 MW.
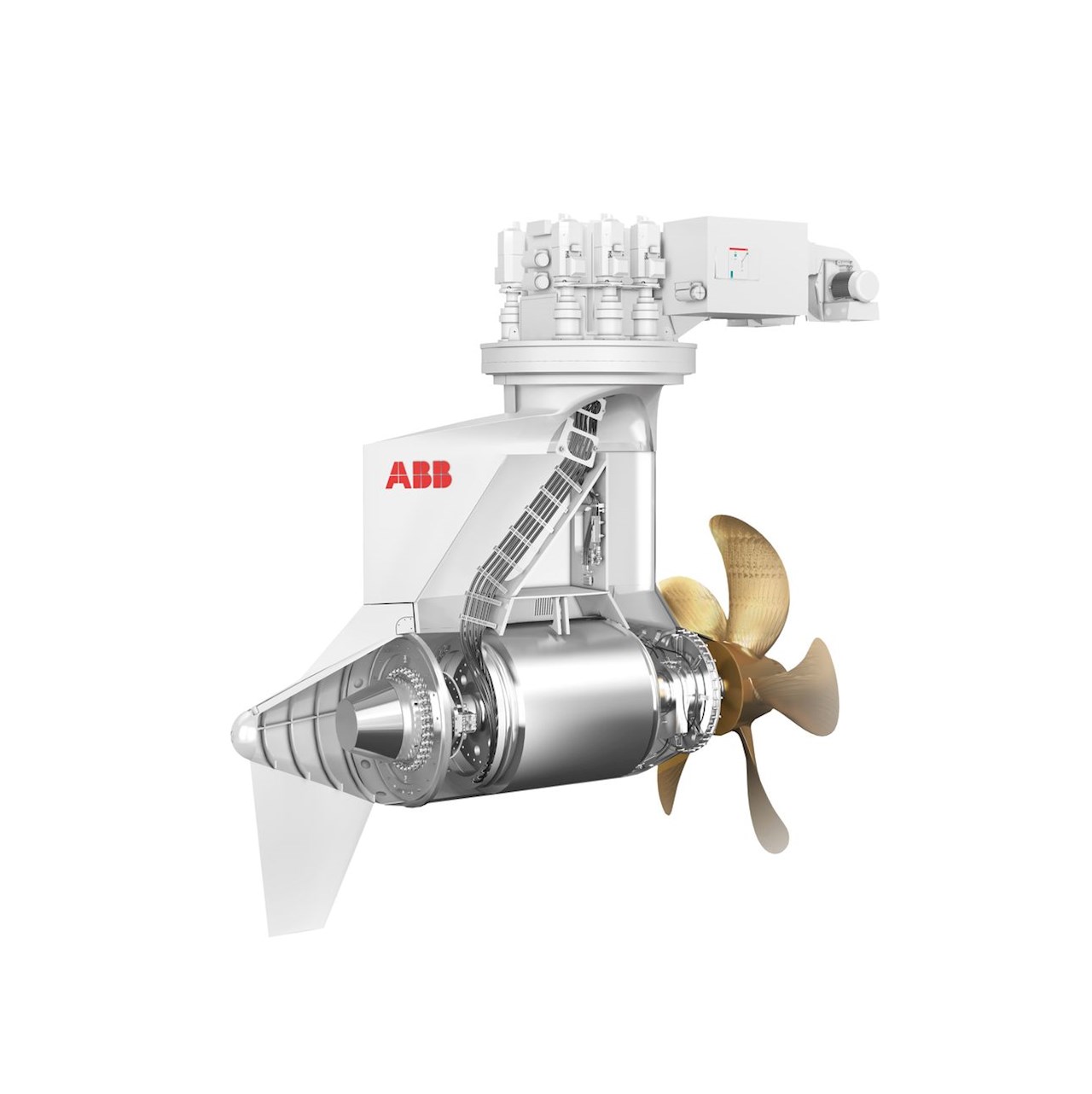
En el centro de la nueva gama de media potencia seencuentran los últimos motores de imanespermanentes de cuarta generación de ABB, que utilizantecnologías de propulsión Azipod probadas, peroperfeccionadas para aumentar la potencia y maximizarla eficiencia. La simplicidad del diseño del sistema depropulsión aumenta la solidez y la fiabilidad, y facilitaelmantenimiento.
Por otro lado, esta serie "M" de propulsión Azipod está adaptada para ofrecer beneficios operativos a los propietarios y operadores de transbordadores y RoPax. Por ejemplo, la nueva serie está diseñada para una baja altura a bordo, lo que permite que el sistema Azipod se coloque bajo la cubierta de los buques RoPax destinada a vehículos, de modo que no se ocupa espacio en la cubierta y no se obstaculiza el movimiento de los mismos.
Basada en los principios de diseño sencillo, sólido y de fácil mantenimiento que se ha aplicado a la propulsión Azipod seleccionada en 25 tipos de buques durante casi tres décadas, la última serie de media potencia llega al mercado en un momento en el que los propietarios de transbordadores y buques RoPax se enfrentan a una mayor presión para mejorar la eficiencia energética y reducir las emisiones.
El controlador de robots OmnicoreTM, nominado al premio IERA a la innovación
OmniCore™ de ABB, la nueva generación de controladores de robots diseñados para las fábricas flexibles del futuro, ha sido finalista del premio IERA (siglas en inglés de «Invención y Emprendimiento enRobótica y Automatización») de 2019. Considerado uno de los premios más importantes del sector de la obótica, IERA reconoce a empresas e inventores que convierten ideas innovadoras en productos que cambian el mercado. El premio lo conceden la Federación Internacional de Robótica (IFR) y la IEEE Robotics and Automation Society.
Los controladores de robots de ABB ya son reconocidos por su precisión de recorrido y la duración del ciclo, los mejores de su categoría. Al desarrollar OmniCore, ABB se basó en estas características al tiempo que creaba un nuevo controlador que aumenta considerablemente la flexibilidad de fabricación, y que está preparado para futuros avances en la era de la fabricación digital.
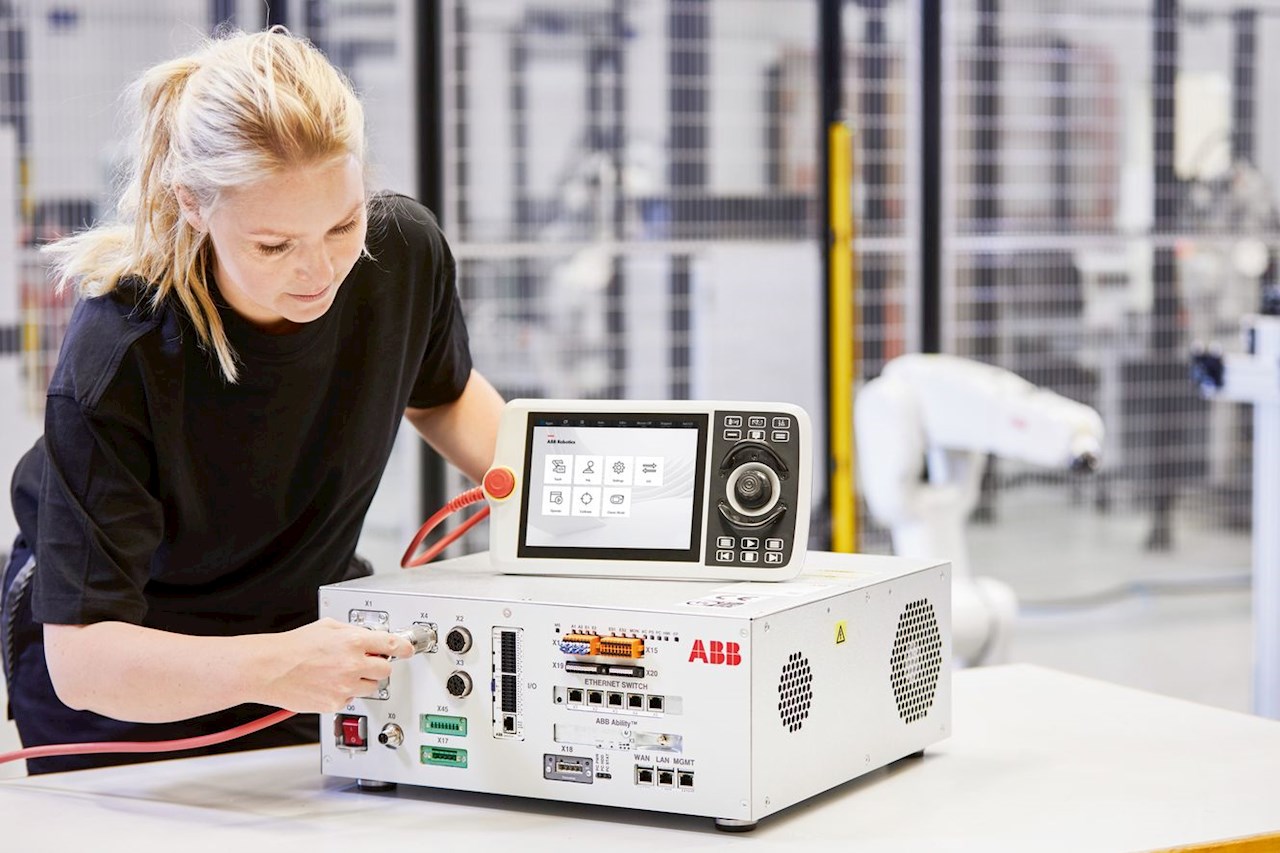
Gracias a su elevado nivel de flexibilidad, OmniCore ofrece a los clientes la posibilidad de fabricar una combinación de productos cada vez más diversos en lotes más pequeños, manteniendo al mismo tiempo la productividad.
Gracias a las funciones "Power-on and Connect" y ABB Ability™, OmniCore puede conectarse a servicios avanzados que aumentan el rendimiento y la fiabilidad, al tiempo que ofrece conexiones fáciles a diversos protocolos de bus de campo, así como sistemas de visión y control de fuerza para soluciones completas.OmniCore incluye medidas de ciberseguridad para evitar la pérdida de datos, cerrando así el bucle entre conectividad, datos y control. También incluye SafeMove2, una solución de software de ABB que transforma los robots industriales en robots colaborativos, capaces de trabajar de forma segura junto a los seres humanos y seguir siendo productivos.
A pesar de todas estas funciones avanzadas, OmniCore es fácil de usar e intuitivo, y se accede a él a través de una interfaz hombre-máquina FlexPendant de diseño nuevo, con una sencilla pantalla táctil para programación visual.
El sistema de electrificación submarina permite al sector del pretróleo y el gas aventurarse en las profundidades marinas
En 2013, ABB y sus socios industriales conjuntos, Equinor, Total y Chevron, iniciaron un proyecto de expansión para diseñar y probar una solución completa de electrificación submarina destinada al sector del petróleo y el gas. Para permitir las operaciones en lugares remotos en aguas ultraprofundas, ABB desarrolló equipos modulares (componentes y conjuntos), que se integran para formar un sistema de electrificación submarina1. El sistema consta de aparamenta de accionamiento de velocidad variable (VSD) y un sistema de protección y control para el transporte, distribución y conversión de energía a bombas submarinas y compresores de gas a una capacidad máxima de 100 MW y profundidades de agua de hasta 3000 metros; y con distancias de transporte de hasta 600 km y requisitos de vida útil de hasta 30 años. Se ha despejado la superestructura (topside) y se han reducido las demandas de suministro eléctrico y las emisiones de gases de efecto invernadero.
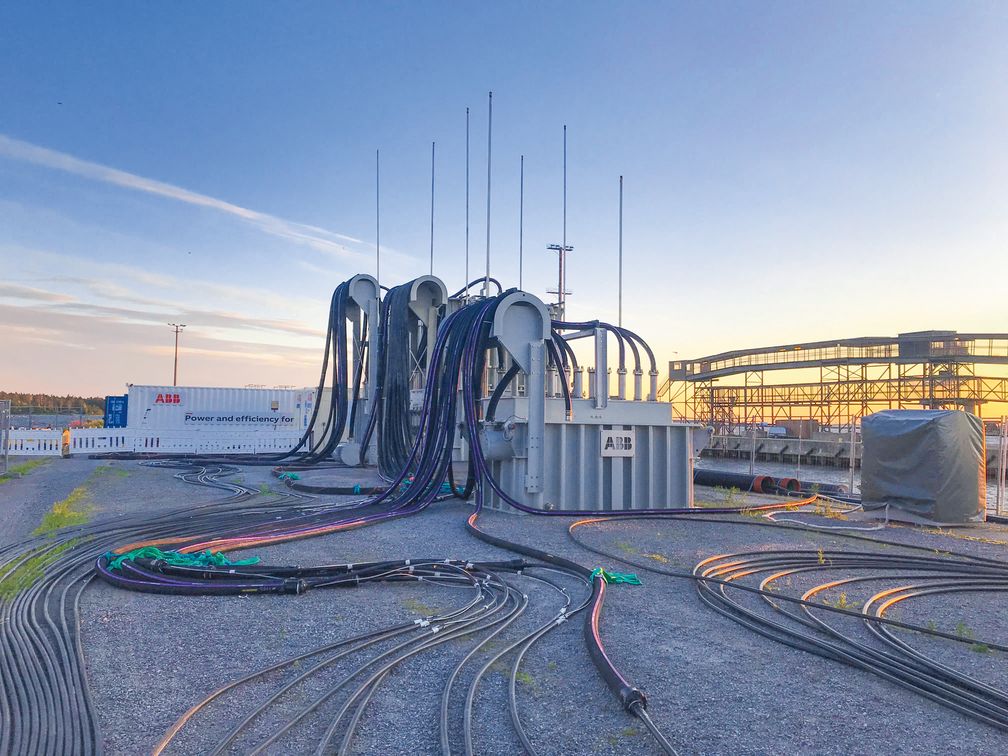
Adoptando un enfoque pragmático paso a paso del diseño de los equipos, ABB llevó a cabo con éxito simulaciones, pruebas de laboratorio y de campo para garantizar que todos los componentes, subconjuntos y conjuntos cumplían los requisitos de acuerdo con las etapas del nivel de preparación técnica (TRL) definidas en la norma DNV RP-A203 y API 17F para sistemas submarinos de control de producción.
Satisfechos con los resultados individuales del dispositivo, se realizaron pruebas en aguas poco profundas (SWT). Se utilizó un prototipo de un sistema de accionamiento de velocidad variable (VSD) de media tensión y se efectuó en un lugar destinado a pruebas de un puerto protegido durante más de 1000 horas2, con resultados impecables.
En junio de 2019 se ejecutó una segunda serie de pruebas SWT (esta vez durante 3000 horas) con un prototipo de todo el sistema de electrificación: dos VSD configurados en paralelo con aparamenta y controles. Los resultados de esta prueba y todas las certificaciones positivas anteriores garantizan la fiabilidad del sistema en condiciones submarinas difíciles. El éxito de esta prueba SWT, finalizada en noviembre de 2019, permite que el sector del petróleo y el gas sepa que esta solución de electrificación está lista para su uso en el entorno submarino profundo.
Notas al pie
1) ¿Ha despertado este asunto su interés? Pues en este número hay más artículos sobre el sistema, su diseño y su cualificación. Consulte en la pág. 44: «La tecnología submarina de ABB está preparando los fondos marinos para un nuevo futuro energético».
2) Consulte en la pág. 50 «Sentando las bases de la conversión de energía submarina», con información detallada sobre la tecnología, el diseño y la funcionalidad de un sistema de accionamiento de velocidad variable (VSD) submarino.
Interruptor de CC ultrarrápido de alta corriente basado en la electrónica de potencia
Los sistemas de distribución de CC a menudo necesitan una protección muy rápida frente a fallos, que simultáneamente ofrezca selectividad de protección, alta supervivencia y capacidad de reconfiguración después del fallo. ABB ha desarrollado ahora un interruptor de CC de estado sólido con electrónica de potencia (SS DCCB), con pérdidas de conducción extremadamente bajas, alta densidad de potencia y un tiempo de reacción ultrarrápido, que soluciona estos problemas de protección. Los SS-DCCB de alta corriente están indicados para intensidades nominales de 1000 a 5000 A, a una tensión operativa de 1000 V CC, y pueden interrumpir una corriente de cortocircuito potencial de varios centenares de kA, es decir, con una rapidez hasta mil veces mayor que los interruptores electromecánicos.
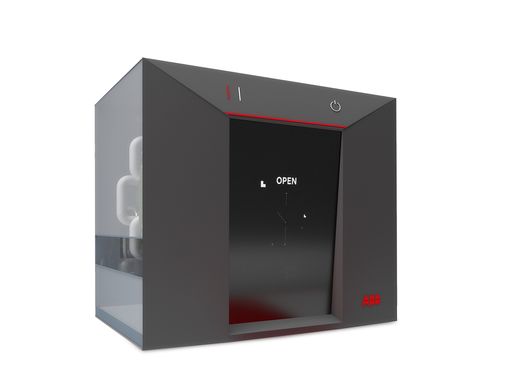
El SS-DCCB de ABB se basa en la conexión en paralelo de tiristores conmutados por puerta integrada y bloqueo inverso de silicio (RB-IGCT) desarrollados internamente en ABB. El interruptor de estado sólido puede enfriarse con agua para lograr una alta densidad de potencia, o bien con una avanzada refrigeración de dos fases, que proporciona la simplicidad de la refrigeración por aire con un rendimiento cercano al de la refrigeración por líquido, y garantiza bajos costes de instalación y mantenimiento, así como una larga vida útil.
Las pérdidas de potencia son un 70 % menores que lasde las soluciones comparables de electrónica de potencia.
Con la creciente popularidad de los buques totalmente eléctricos, la distribución a bordo de electricidad de CC está llamando mucho la atención gracias a su capacidad para manejar grandes flujos de energía en un espacio confinado, con una alta eficiencia del sistema y un bajo coste del ciclo de vida. El SS DCCB es perfecto para estas aplicaciones marinas, y es en este ámbito donde se utilizará el dispositivo inicialmente. Se trata del primer interruptor de ABB listo para poder integrarse directamente en cualquier sistema de distribución de CC de los buques. Una arquitectura modular, un hardware simplificado y unas interfaces digitales garantizan la máxima flexibilidad. El nuevo interruptor es perfecto también para muchas otras áreas, como microrredes de CC, sistemas de almacenamiento de energía de baterías, centros de datos, infraestructuras de carga de vehículos eléctricos, etc. La primera aplicación comercial está prevista para este año.
Una aplicación para detección de anomalías que ayuda a los robots a reducir el tiempo de inactividad
Todo el mundo sabe lo que es una anomalía, ¿verdad? Por ejemplo, que todos los botones de su camisa sean iguales excepto uno… Bueno, en realidad este es un ejemplo bastante obvio. Pero cuando se trata de distinguir qué alarmas son reales y cuáles son falsas entre las generadas por los robots de una fábrica, la situación se complica.
La detección de anomalías, que es una rama del aprendizaje automático (machine learning), se centra en la detección e identificación de discrepancias que se desvían significativamente de la mayoría de otras observaciones en grandes conjuntos de datos o flujos de datos. Tales discrepancias, si se detectan y localizan repetidamente, pueden proporcionar una alerta temprana de funcionamiento incorrecto o la confirmación de un evento que podría necesitar la atención humana.
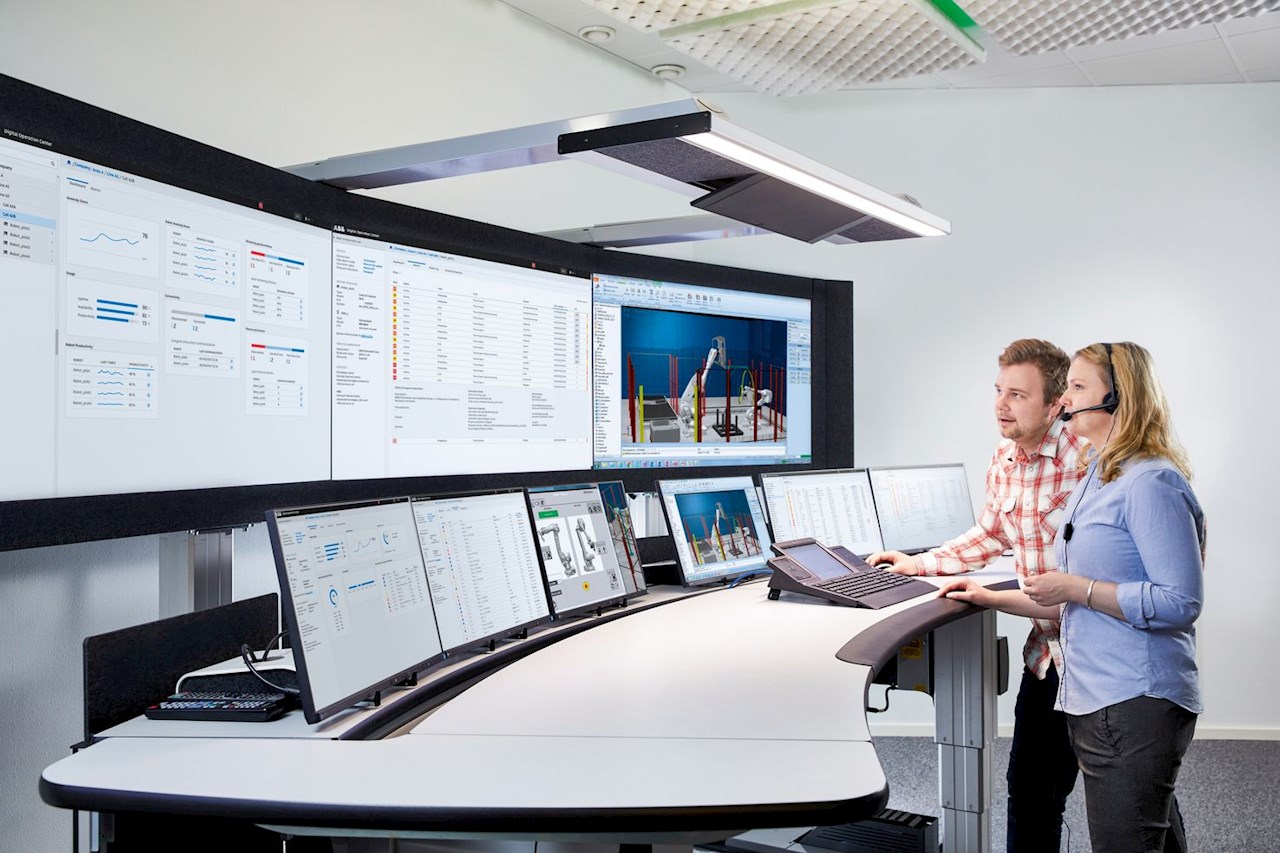
Utilizando un enfoque histórico en relación con una gran cantidad de datos, los ingenieros de software de ABB han desarrollado una vía estadística para comprender las distribuciones de eventos para robots individuales en entornos fabriles y obtener información sobre su estado en tiempo real mientras cada robot está en funcionamiento. El enfoque está diseñado para mostrar puntuaciones anómalas en los paneles de control de la flota de robots, generar alarmas de eventos automáticamente, ejecutar las actividades de mantenimiento de manera proactiva y predictiva, reducir el tiempo de inactividad, evitar microparadas y, en última instancia, maximizar la eficacia general de los equipos (OEE).
La idea es crear una herramienta que los clientes puedan usar para gestionar los datos de parámetros físicos, así como alarmas y eventos generados por robots de forma agregada, con vistas a obtener actualizaciones del estado del robot junto con gráficos de tendencias de puntuación que puedan indicar problemas futuros y una forma de identificar rápidamente la raíz de los problemas. ABB ofrecerá la herramienta como aplicación basada en el aprendizaje automático (machine learning) y formará parte de la última generación de ABB Ability™Connected Services.
EC Titanium: motor y accionamiento inteligentes integrados
Como su nombre indica, el nuevo motor y accionamiento inteligentes integrados EC Titanium de ABB combina motor y accionamiento de velocidad variable (VSD) en un solo paquete fácil de instalar. El EC Titanium está concebido para aplicaciones de 1 a 10 CV e incorpora los últimos avances en motores y accionamientos en una solución sumamente eficiente, compacta y conectada.
Se eligió un diseño de motor de reluctancia síncrona asistido por imanes de ferrita (FASR), ya que el bajo nivel de pérdidas hace que estos motores puedan alcanzar una clase de eficiencia IE5 y ser rentables.
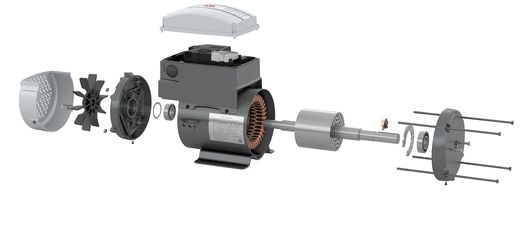
Otras ventajas dignas de mención son su diseño fácil de instalar y una alta densidad de potencia (el doble que los motores de inducción). Un VSD integrado permite a los clientes adaptar la velocidad de accionamiento a los requisitos del proceso y hacer funcionar los equipos en su punto más eficiente desde una perspectiva energética, lo que prolonga la vida útil, ahorra energía y facilita el cumplimiento de las normas de eficiencia. A plena carga, el rendimiento total del sistema es elevado. A carga parcial, modo en el que operan muchos clientes, la eficiencia puede ser un 16 % mejor que con un motor de inducción equivalente.
Otras ventajas para las aplicaciones de bombas y ventiladores incluyen la reducción de los requisitos de inventario, ya que se dispone de diferentes caudales del mismo paquete. Además, los productos integrados reducen los costes mediante la reducción de piezas y la simplificación de las compras y el montaje. El ECTitanium ofrece a los clientes múltiples opciones de conectividad (cableado, RS485 o Bluetooth). Por otra parte, el accionamiento actúa como sensor para el paquete motor/accionamiento, y se puede añadir un sensor inteligente para motores a fin de medir otros parámetros de rendimiento. Una vez conectado, los datos pueden enviarse a la plataforma ABB Ability™, donde un software con algoritmos avanzados analiza la información y detecta anomalías para la supervisión del estado y el mantenimiento predictivo.
Sotware de tercera generación para recogida y empaquetado, que reduce los tiempos de puesta en servicios de días a horas
¿Cómo pueden los fabricantes responder con eficacia a las demandas de personalización masiva y los ciclos de vida más cortos del producto? Cada vez más, la respuesta es la tecnología de gemelos digitales, que permite a los clientes probar configuraciones en líneas de producción virtuales antes de modificar o construir líneas físicas.
Con esto en mente, ABB Robotics ha lanzado la tercera generación de su software PickMaster® para aplicaciones robóticas de recogida y empaquetado.
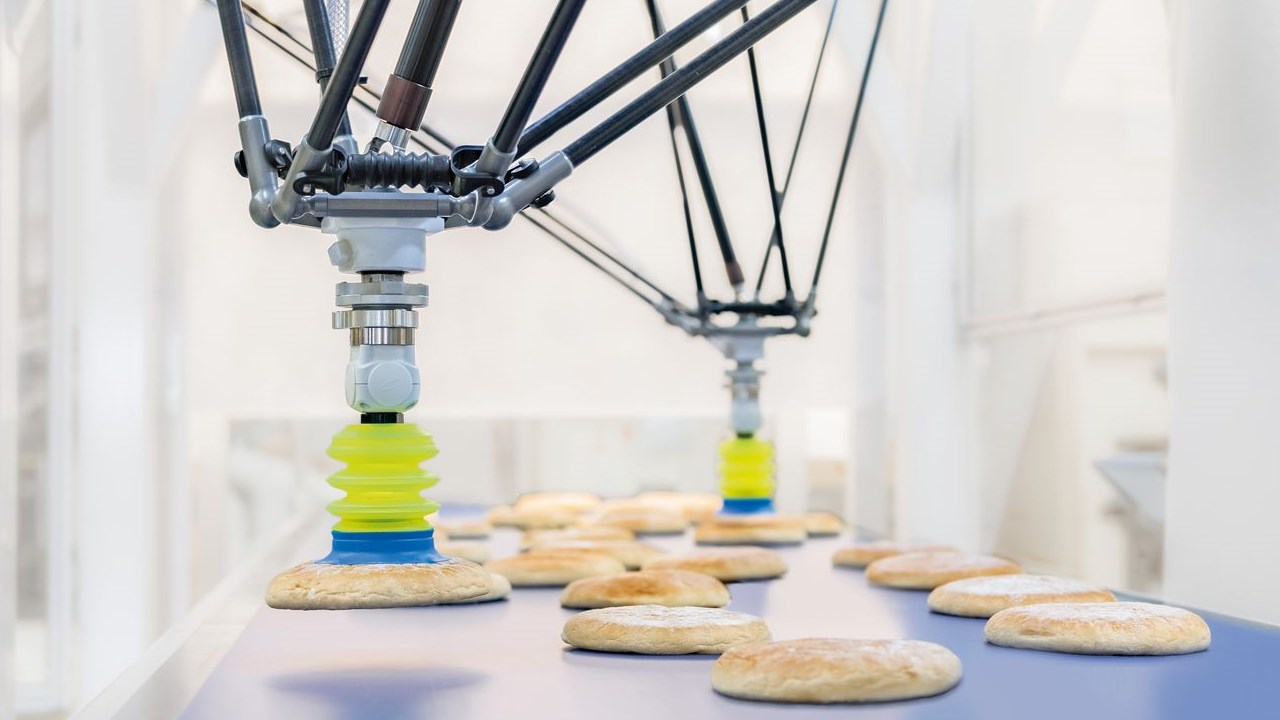
El software es líder del mercado por lo que respecta a la configuración fácil de acciones robóticas complejas y se ha convertido en una referencia en el sector por simplificar la integración de robots en la recogida de flujo aleatorio guiada por la visión, el empaquetado y la manipulación de materiales desde hace más de 18 años.
Equipado por primera vez con tecnología de gemelos digitales, el software acorta los tiempos de puesta en servicio, que pasa de días a horas, y reduce los períodos de cambio de producto, de horas a minutos. Ofrece una mayor flexibilidad y una mejor visualización de la colaboración entre múltiples robots, logrando con ello resultados de flujo optimizados sin pérdidas de producto ni paquetes incompletos en envoltura de flujo, carga de bandejas, embalaje de cajas y cartones y aplicaciones de manipulación.
Puesto que el software permite la programación offline de las tareas de recogida y empaquetado, los usuarios pueden crear, simular y probar una instalación robótica completa en un entorno virtual sin interferir con sus líneas de producción reales. Utilizando la tecnología de gemelo digital, el proceso de recogida puede optimizarse en el mundo virtual en tiempo real, mientras que el proceso real actúa en consecuencia. Esta operación no solo ayuda a los clientes a mitigar los riesgos costosos y laboriosos, sino que también acorta el tiempo de comercialización de nuevos productos, ya que las líneas de productos se pueden instalar con mayor rapidez y aumentar su velocidad al máximo sin que haya sorpresas durante la puesta en servicio.
PickMaster® también ofrece una interfaz de operario moderna para la planta de producción, que proporciona a los operarios y a los directores de planta una visión completa y un control de los resultados de producción. Esta solución cumple la norma industrial PackML, se integra perfectamente con otras máquinas de empaquetado, así como con los sistemas de producción y planificación de la fábrica.
PickMaster® está disponible en multitud de configuraciones y puede trabajar a la perfección con todos los robots de ABB, así como con diversas máquinas virtuales y físicas. Es la herramienta más adecuada para fábricas y líneas de producción en las que es crucial una mayor producción, tiempos de respuesta más rápidos y cambios rápidos de producto.
A200-H: la nueva referencia en turbocompresión de una sola etapa
Como buque insignia de la generación de turbocompresores de una sola etapa, el A100-H, lidera actualmente el campo de la turbocompresión de una sola etapa, con coeficientes de presión de hasta 5,8, una eficiencia de hasta el 66 % y una presión media efectiva al freno (bmep) de hasta 22 bar. Para valores superiores de bmep, el sistema de dos etapas Power2® de ABB responde a la perfección. Para una aplicación con una bmep de entre 22 y 24 bar, la turbocompresión de dos etapas es potencialmente demasiado compleja.
Para llenar este vacío entre la turbocompresión de una y de dos etapas, ABB ha desarrollado el A200-H de una etapa, con un coeficiente de presión de hasta 6,5 y una eficiencia máxima del turbocompresor superior al 69 %. El A200-H permite la turbocompresión de una sola etapa en motores de gas de alta velocidad con una bmep de aproximadamente 24 bar, al tiempo que aumenta la eficiencia del motor en comparación con el A100-H.
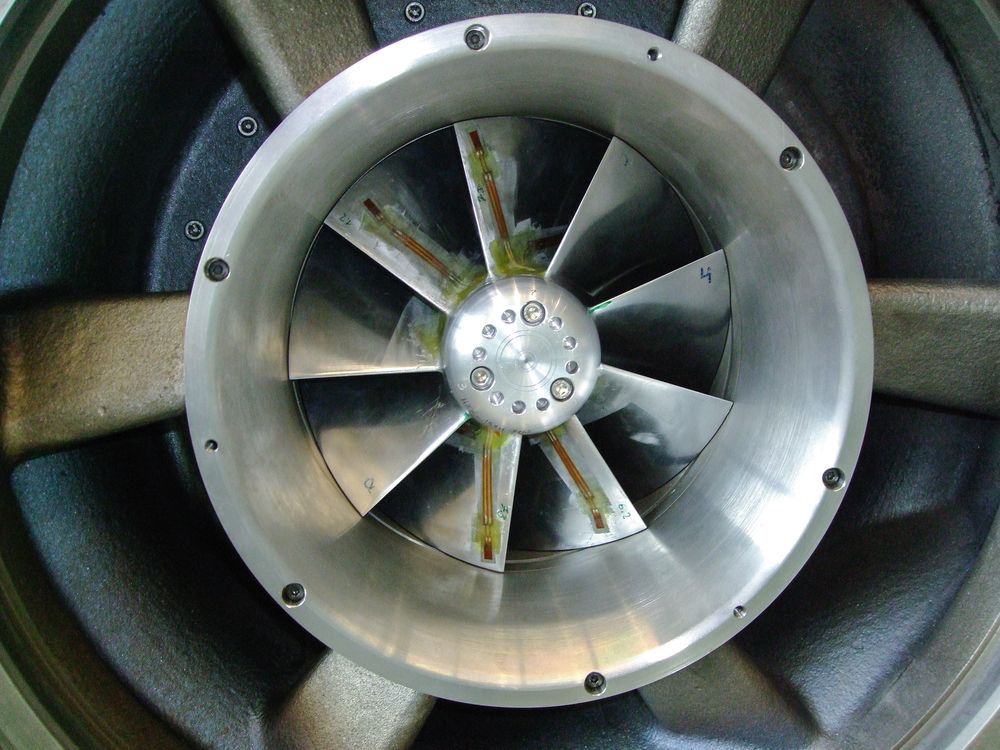
La turbina del A200-H se ha adaptado al compresorpara obtener la máxima eficiencia posible del turbocompresor y cumplir los requisitos mecánicos. Además, con vistas a futuras aplicaciones de nivelación de cargas punta con muchos ciclos de arranque y parada, se ha minimizado la tensión de la carcasa1.
Por primera vez, el cliente puede elegir entre dos conceptos de cojinete: un diseño patentado del módulo de cojinetes que soporta los cojinetes lisos de ABB, o bien cojinetes de bolas de alta eficiencia desarrollados recientemente que, a carga parcial, tienen una pérdida de potencia de alrededor del 15 % de la que tiene la opción de cojinetes lisos. Estos nuevos cojinetes reducen el tiempo hasta la plena carga en un 15 %.
El control de la velocidad y la temperatura del turbocompresor, los ciclos de arranque y parada, las condiciones ambientales y otros parámetros se introducirán utilizando sensores integrados en el turbocompresor o accediendo a los datos del grupo electrógeno. Estas fuentes de datos exhaustivas permiten una evaluación de la vida útil de los componentes basada en la exposición y, por ejemplo, permiten que los rotores superen el tiempo de ejecución predefinido por los enfoques convencionales, que son más rígidos.
Nota al pie
1) Para más información sobre el turbocompresor A200-H, consulte el artículo «A200-H: la nueva referencia en turbocompresión de una sola etapa» en las páginas 56-61 de este número de la Revista ABB.