En las últimas décadas, la industria de automoción ha automatizado una gran variedad de procesos, incluidos la automatización de prensas, talleres de carrocería, pintura y montaje de motores y transmisión. Pero cuando se trata del montaje final, la automatización sigue siendo un reto importante. La razón es que hay áreas como la conexión de cables, el montaje del volante y la instalación de muchos otros componentes que son extremadamente complejas.
Josep Vilarrasa, Jorge Vidal-Ribas - Robotics, Final trim & Assembly - Barcelona, España josep.vilarrasa@es.abb.com - jorge.vidal-ribas@es.abb.com; Jordi Artigas - Robotics, Consumer segment & service Robotics - Barcelona, España, jordi.artigas@es.abb.com; Tomas Groth - Robotics & Discrete Automation Technology - Västerås, Suecia, tomas.groth@se.abb.com; Biao Zhang - ABB Robotics - Raleigh, NC, Estados Unidos, biao.zhang@us.abb.com
Ahora, gracias a los avances de ABB Robotics y las tecnologías de control visual, estos avances están dando paso a aplicaciones piloto. Y, lo que es más, se prevé que las tecnologías descritas en este artículo sean eventualmente aplicables a otros campos centrados en objetivos inestables, como operaciones de logística basadas en el uso de vehículos de guiado automatizado. Históricamente, la automatización de muchas de las operaciones del montaje final de automóviles se ha considerado prácticamente imposible. En consecuencia, nunca se han concebido ni diseñado componentes asociados teniendo presentes las capacidades de automatización actuales. El resultado es que las líneas de montaje final de automóviles →01 siguen dependiendo enormemente de la destreza humana.
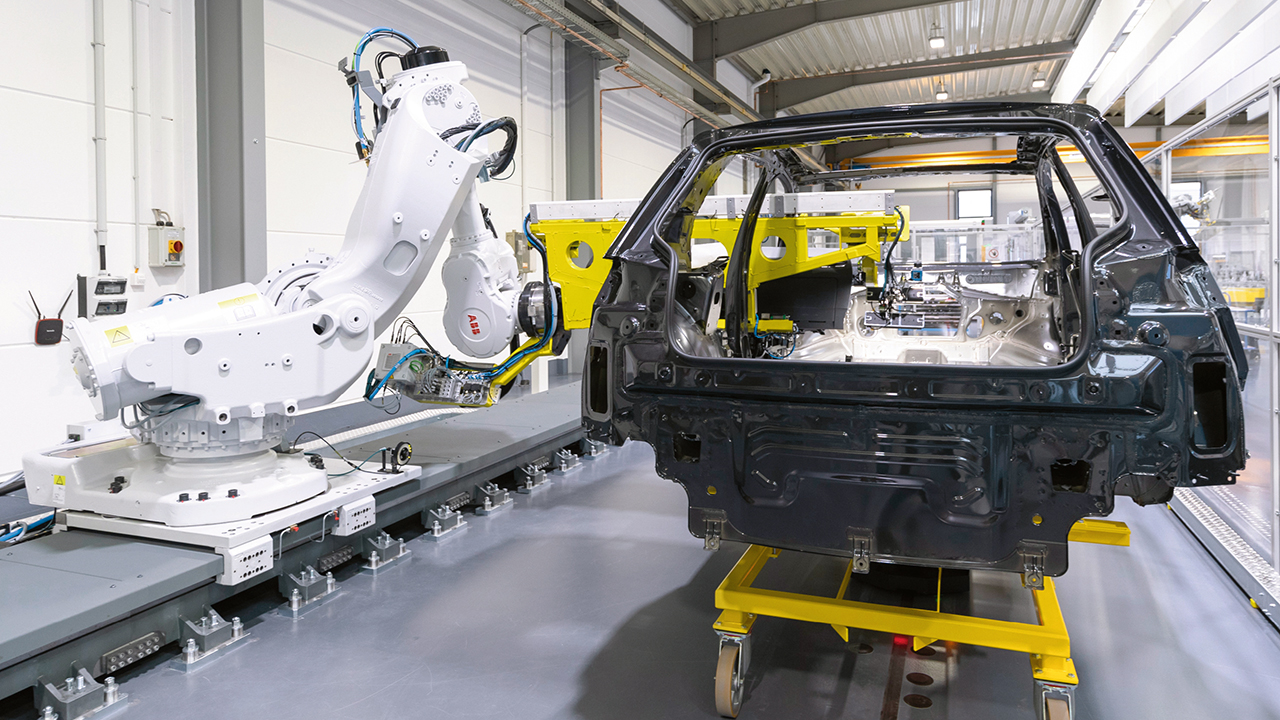
Las líneas totalmente automatizadas en áreas como talleres de soldadura de carrocerías funcionan en modo «stop & go», lo que facilita la automatización de distintas celdas. Las líneas operadas manualmente, por otra parte, se mueven lentamente de manera continua transportando carrocerías por distintos tipos de cintas transportadoras o, en casos avanzados, en vehículos de guiado automatizado (AGV). Estos sistemas, que normalmente se utilizan en fábricas y almacenes, siguen líneas marcadas o cables en el suelo o utilizan ondas de radio, cámaras de visión, imanes o láseres para la navegación. Independientemente de si el medio de transporte es un sistema de cintas transportadoras o un AGV, el movimiento se produce a una velocidad moderada de cerca de 100 mm/s, lo que permite a los operadores humanos llevar a cabo tareas de montaje con el nivel de seguridad requerido.
En el caso de los robots, sin embargo, estos entornos plantean una serie de retos difíciles. Por un lado, los sistemas de transporte de vehículos tienden a ser irregulares, y los suelos suelen ser desiguales, lo que da lugar a temblores y vibraciones. Así, si un robot debe emular el comportamiento humano en este tipo de entorno, debe estar equipado con visión artificial. Los sistemas de visión convencionales actuales normalmente están basados en capturas de posiciones de referencia estáticas para localizar las posiciones objetivo para las tareas de montaje. En este caso, a medida que las carrocerías se mueven por una línea, se requiere una capacidad adicional: un seguimiento por visión continuo para gestionar los movimientos, las irregularidades y las vibraciones. Su diseño permite a los robots adaptar continuamente su movimiento a una secuencia de imágenes de referencia capturadas mediante visión, con una frecuencia de captura de entre 20-50 por segundo.
El seguimiento por visión está basado en una técnica conocida como Servo Visual →02, que utiliza información de retroalimentación extraída de un sensor de visión para compensar los movimientos y las vibraciones. En este caso, en lugar de moverse conforme a un recorrido programado como lo haría un robot convencional, los movimientos del robot están guiados por la información facilitada por el o los sensores de visión. En cuanto a los robots de ABB, esta funcionalidad, denominada External Guided Motion (EGM), puede actualizar las entradas de orientación cada 4 ms, dando lugar a respuestas muy rápidas.
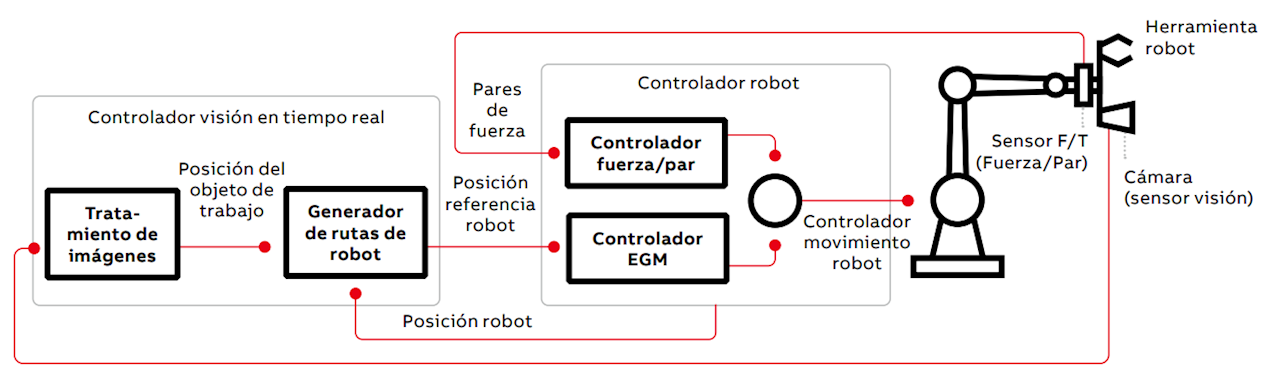
Además de la EGM, los robots de ABB también utilizan un sensor de fuerza-par: ABB Integrated Force Control. Esta tecnología permite al robot adaptar sus movimientos basándose en entradas de fuerza y par obtenidas del contacto con la carrocería (comportamiento mecánico conforme). Normalmente el sensor está instalado entre a herramienta y la muñeca del robot →02. La combinación de la tecnología servo visual y el comportamiento mecánico conforme es un ejemplo de fusión sensorial, una tecnología en la que los datos procedentes de distintas fuentes de sensores se combinan en tiempo real.
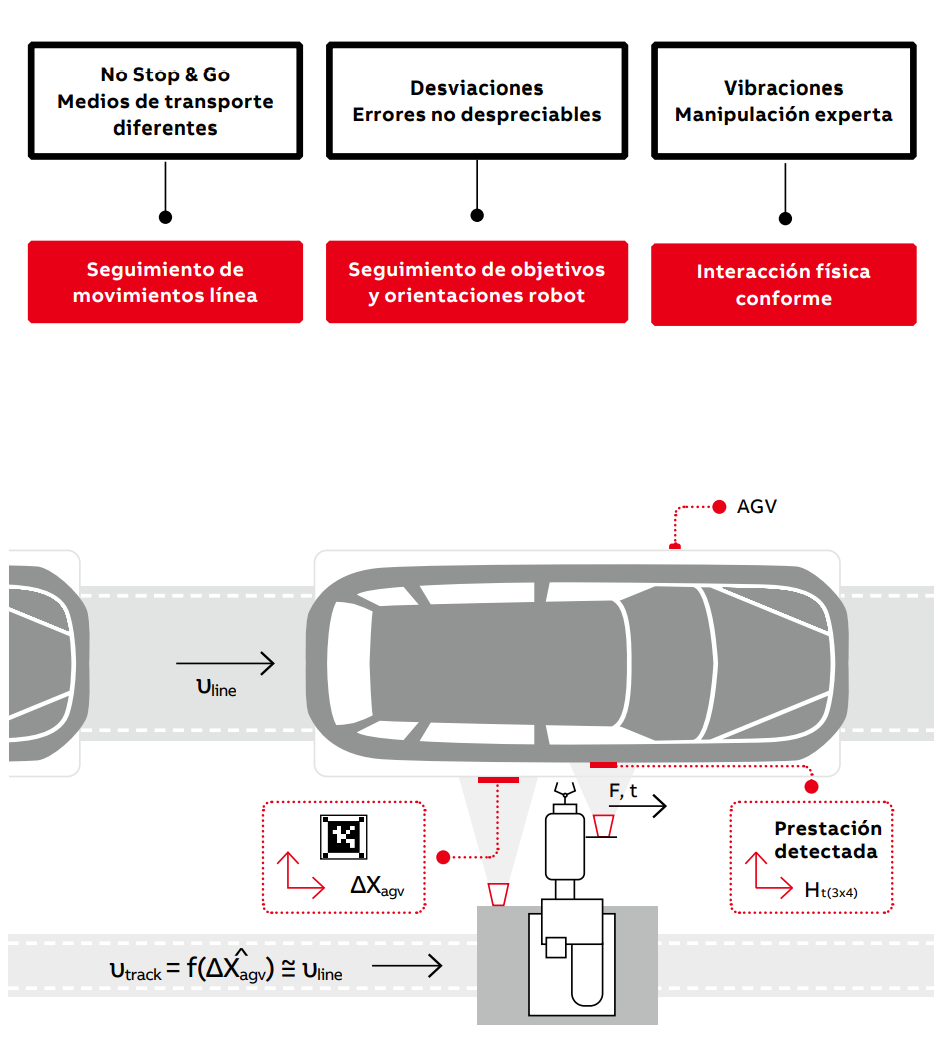
A medida que estas tecnologías maduran, merece la pena plantearse cuál podría ser el aspecto de un proceso de montaje final completamente automatizado. Básicamente, según se menciona en →03, se reduciría a las siguientes tareas.
1. Seguimiento de los movimientos de la línea
Esto significa hacer un seguimiento de los principales movimientos de una línea de montaje para obtener un entorno pseudoestático. Normalmente, los robots han hecho seguimiento de partes de un sistema de cintas de transporte utilizando lo que se conoce como una función de seguimiento de las cintas transportadoras. Este sistema se basa en utilizar un codificador mecánicamente conectado al movimiento de la cinta transportadora. Sin embargo, en el caso de las carrocerías que se desplazan en AGV, esta forma de seguimiento no es sencilla de implantar debido a las adaptaciones mecánicas que implica.
La solución de ABB a este reto ha sido aplicar su tecnología Servo Visual, que hace un seguimiento de los AGV bien mediante un sistema AprilTag o mediante una característica visual del AGV. La ventaja de utilizar un sistema AprilTag es que no solo es fácil de instalar, sino también mucho más robusto. Desarrollados por la Universidad de Michigan, los AprilTags son códigos de barras bidimensionales conceptualmente iguales que los códigos QR. La diferencia es que los AprilTags están diseñados para procesar pequeñas cantidades de datos, lo que los hace comparativamente robustos y más fáciles de detectar, resultando en una precisión de localización mejorada y un procesamiento informático más rápido.
El seguimiento visual, por otro lado, implica el uso de cámaras montadas en sala o una cámara montada en el pie del robot si el propio robot está montado sobre un eje lineal. El eje lineal del robot, también conocido como «track motion» en la cartera de productos de ABB, conlleva el uso de una unidad lineal controlada por servo que sirve para ampliar el alcance del robot. El eje lineal del robot es necesario en aquellos procesos de montaje caracterizados por un tiempo de contacto significativo entre la pieza o el componente que debe montarse y la carrocería.
La tecnología no se limita a hacer un seguimiento de los movimientos del robot en los AGV y también puede utilizarse en cintas transportadoras convencionales.
2. Seguimiento de objetivos y orientación del robot
Una vez alcanzado este entorno pseudoestático, el robot aún tiene que enfrentarse a tolerancias residuales, irregularidades y vibraciones antes de llegar a su objetivo de montaje. En este caso, hay una cámara montada en la herramienta robot. El robot conoce la posición relativa de la cámara en relación con el controlador fuerza-par (FTC) de la herramienta, lo que le permite concentrarse en la posición objetivo. A diferencia del seguimiento del movimiento de la línea basado en AprilTags, la cámara se centra en una imagen de una característica real →03 de una carrocería monitoreada cuya posición relativa al objetivo de montaje se conoce. En estas circunstancias, no se utilizan AprilTags debido a la complejidad añadida que se requiere para montarlos y después retirarlos, algo que tendría que realizarse en las distintas estaciones. Sin embargo, hacer un seguimiento de las características visuales a medida que las carrocerías se mueven a alta velocidad sigue planteando un reto, especialmente por lo que respecta a gestionar varios colores y variaciones en las condiciones de iluminación. →04 ilustra los movimientos de un robot en relación con el control de un objetivo utilizando visión en tiempo real.
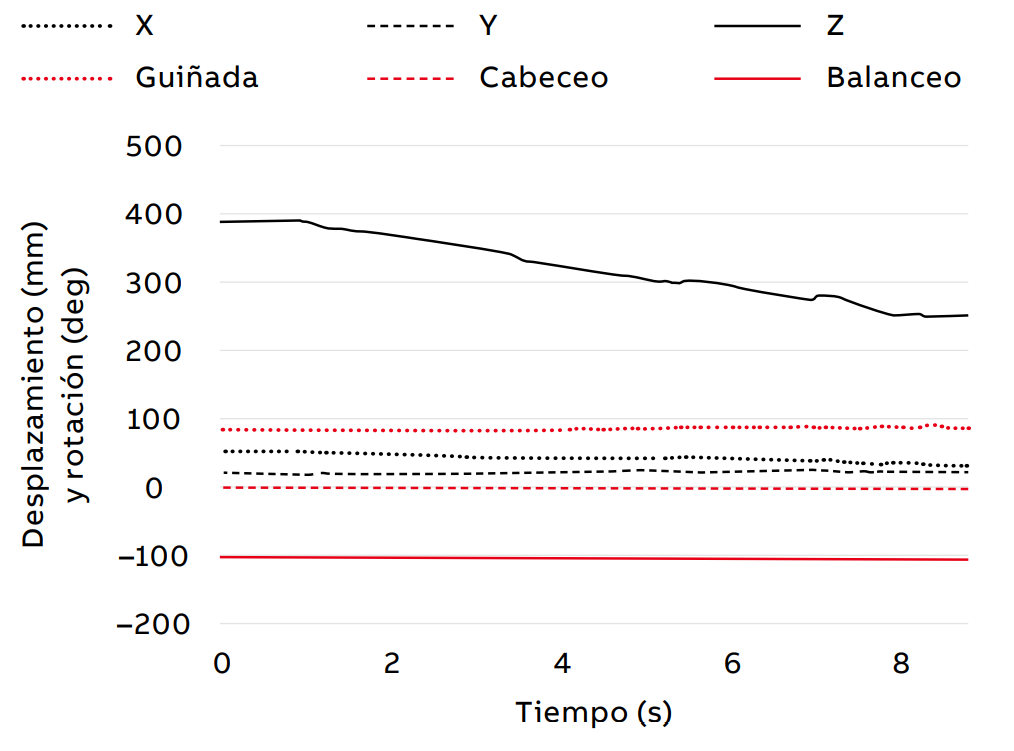
3. Interacción física conforme
Una vez identificado el objetivo, se inicia el contacto físico, y el robot lleva a cabo su tarea de montaje →05 siguiendo una combinación de entradas de sensores de visión y fuerza-par. Esto implica mantener el seguimiento de visión durante todo el contacto y comportarse de manera conforme utilizando el feedback continuo facilitado por el sensor Force Control instalado entre su muñeca y la herramienta. Esta combinación de entradas procedentes de un sensor de visión y un sensor de fuerza-par (fusión sensorial) son la clave para llevar a cabo un proceso de montaje con éxito.
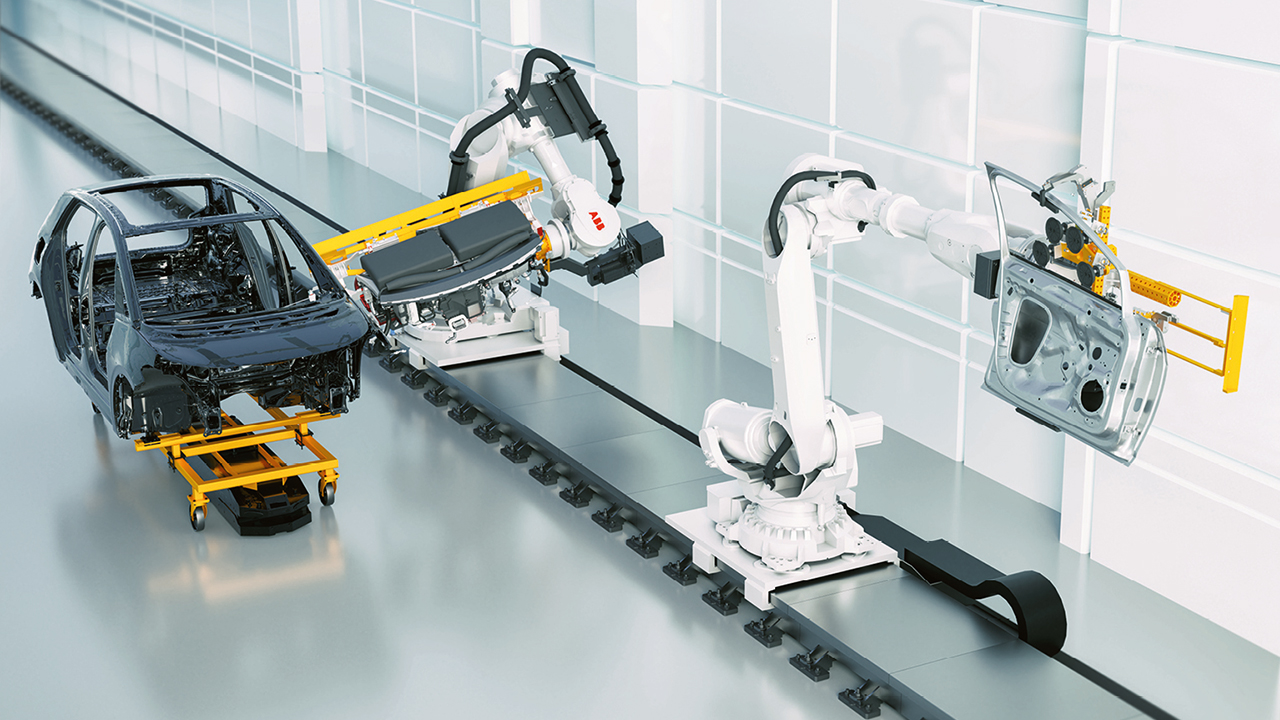
En algunos casos de aplicación, pueden no requerirse las habilidades de los pasos 2 y 3. Por ejemplo, es posible que no sea necesaria una precisión sin fallos si la tarea está seguida de una operación manual en una estación aguas abajo. En otros casos, el paso 1 podría omitirse debido al uso de un seguimiento de cinta transportadora tradicional.
Mirando al futuro
En el futuro, podrán implementarse nuevos conceptos que permitirán el montaje de objetivos en celdas estáticas, obviando así la necesidad de tecnologías diseñadas para llevar a cabo tareas de montaje en líneas en movimiento. Por ejemplo, un concepto considera agrupar las celdas que pueden automatizarse fácilmente en una sublínea totalmente automatizada en modo «stop&go». Otros conceptos consideran celdas de montaje estáticas que abordan la logística de coches y componentes a medida que se mueven.
No obstante, la demanda de la automatización de las tareas de montaje en líneas móviles seguirá jugando un papel fundamental a corto y medio plazo. Si bien esta demanda actualmente responde a necesidades de aplicación procedentes del entorno de montaje final de automóviles, una vez que estas tecnologías se desarrollen por completo, no hay duda de que serán aplicables a otros campos centrados en objetivos inestables, como las operaciones logísticas con AGV.
Por ahora, sin embargo, ABB está concentrándose en aplicar esta tecnología al sector automovilístico, donde sus aplicaciones piloto basadas en el cliente ya incluyen montaje de cabina —actualmente en producción— colocación de alfombrillas, colocación de asientos, montaje de puertas, y mucho más. Además, la experiencia adquirida a través de estas y otras aplicaciones se destinará a otras aplicaciones de montaje de la industria de la automoción que se caracterizan por presentar dificultades técnicas parecidas.