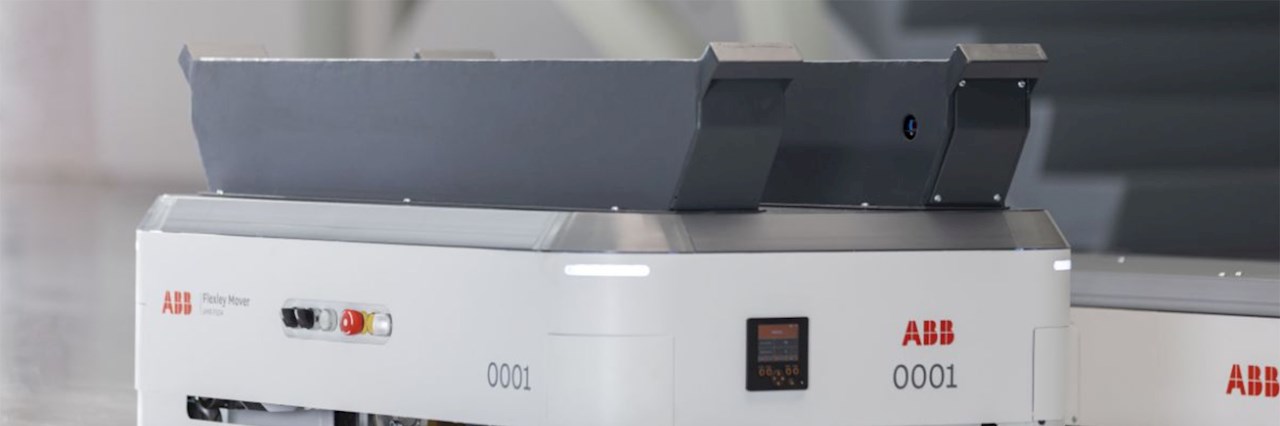
Robotic Process Automation is one of the most beneficial transformations possible to increase the productivity of an industrial plant. Let's have a look at where to start to achieve automation that will help save costs in your organization.
At AMR ABB Robotics, we are experts in implementing automation for different industries, and we know that every one of them is different and with individual needs and challenges. So let’s start from the beginning!
Where to start in a robotic automation process?
While not all processes suit automation, there are many repetitive industrial tasks that can be automated easily with mobile robotics. As a first step, we recommend going over a few high-level assessments to know which processes might benefit from undergoing automation. This step will determine how automation can help you save costs and effectively increase your production rate.
Is your business ready for automation with robots?
To start off an automation project, it is a key step to evaluate the feasibility of implementing mobile robots in your plant or warehouse with an expert. The easiest way to do this is to contact one of our experts and get a Feasibility Analysis to evaluate which solution suits you best, how many robots you will need and an estimated cost for the project.
Through the Feasibility Assessment study, you will then be able to identify which processes are not structured in a way that would benefit from automation, and which ones are.
You may also look around and see if other companies in your industry are implementing robotics in their processes. If that is the case, we recommend gathering information to identify which processes exactly have been automated, and why. This will also give you some insight as to the most common automation applications on the market.
If you would like to know more, you can find some Case Studies from different industries that have successfully implemented robotics in their plants in the Resources section of our website.
Processes that can be automated:
1. Transportation:
Transportation processes can implement robotic process automation to increase the overall efficiency of a system. Taking workpieces from one workstation to another can be done automatically with the help of robots. Different types of machines and techniques are commonly used to automate transport systems; among them are different conveyor systems and autonomous mobile robots. These machines lessen the burden of transporting Work-In-Progress items from one workstation to another while reducing the time required for traditional transport methods.
For instance, in Logistics and Ecommerce, mobile robotics can help with optimizing your storage space as well as responding quickly to demand peaks and improving customer satisfaction, multiplying your productivity and increasing picking rate effortlessly by up to three times.
2. Material Handling:
Managing short-distance movement within a building or between buildings is key in intralogistics operations. Automated material handling makes products easier to locate, move and ship, streamlining production and order picking processes. At the same time, it reduces costs and potential damage to products when they are transported properly.
Picking is a process that can benefit from robotic automation as well. AMR ABB Robotics Mouse range of robots can support the preparation of kits of related items, speeding up manufacturing or picking processes. Similarly, our Flexley Stack line can transport raw materials to feed lines or handle finished products at the end of the production line for storage or preparation of shipping docks. If you have similar processes in your plant, they can be a good starting point for automating your processes.
3. Assisting in production flows:
In addition to logistical and production processes, a large number of complementary movements take place within the plant. Mobile robots can perform auxiliary tasks such as collecting waste or defective parts. They can also supply empty containers, boxes or pallets.
How many robots do I need?
The use of AMRs provides a reliable and accurate solution for you to increase efficiency and traceability in your production and distribution processes, optimize the transportation and delivery of products or improve and streamline order preparation while saving costs.
But how many mobile robots might you need to achieve your goal? In our experience, each project is different. Whereas some plants need only 3 units, other, larger or more complex projects may require more. This will depend on the size, needs and demands of each business.
For an example of a smaller size, we implemented eight 10TN Tribot AMRs guided by SLAM navigation for our client SEAT in the automotive industry. These robots increased our customer’s productivity by improving their competitiveness and flexibility, and significantly reduced their time to market and logistics expenses.
For a more large-scale example, we installed 30 P204 AMRs in the logistics warehouse of a client in the Ecommerce industry to automate their picking process.
There is no strictly defined quantity of robots that you might need, which is why we always recommend requesting a Feasibility Analytics first to analyse your requirements. At AMR ABB Robotics, as experts in automation and robotic solutions, we would like to support you in discovering how to automate your industrial processes. If you choose to work with us, we will start by: Finding the solution that best suits your needs. Sizing the project: How many AMRs do you need? Obtaining a technical solution for your project. Getting a quote so you can estimate the ROI. Solving all your doubts with an expert.