- Sims Metal, a division of Sims Limited, is a leading metal recycler that buys, processes, and sells ferrous and non ferrous metal. Their purpose is to create a world without waste to preserve our planet
- Sims Metal has ambitious climate targets, including a commitment to be carbon neutral by 2030 and net zero by 2050. As part of these commitments, they are working with suppliers and partners to introduce innovations and new technologies into its operating processes
- ABB’s ACS6080 Medium Voltage AC Drive and motor and transformer package has been selected by Sims Metal to support in power generated and controlled for their metal shredding application at their facility just outside of Melbourne, Australia. Extremely high levels of safety, both for people as well as equipment, are delivered via an arc-resistant design and certified functional safety features of the drive
- The ACS6080 drive has already proven to reduce the energy usage of the metal shredding application. Increased throughput has also been observed and the electronic control of the ACS6080 drive is so rapid that spikes are now virtually non-existent
Sims Metal, a global leader in metal recycling, buys, processes, and sells ferrous and nonferrous metal to manufacturers in 30 countries. With a global footprint of more than 130 metal recycling facilities across 15 countries, the business serves consumers, businesses and governments by diverting millions of tonnes of secondary materials from landfill each year. Sims Metal is keenly focused on addressing their decarbonisation and circularity challenges, as well as those of their customers by enabling the use of secondary materials in customer supply chains. In 2021, the business reported that it recycled 8.6 million tonnes of discarded metal, turning them into valuable products for society.
In Australia, Sims Metal is a leading collector, processor and supplier of recycled metals like steel, iron, copper and aluminium. Through their network of more than 30 facilities serving all states and territories across the country, Sims Metal buys and processes discarded metal from local businesses, other recyclers and the general public. Sims Metal has a facility in Brooklyn, Victoria, where their processing capacity is facilitated by fragmentisers, shears and balers. This allows them to operate at the highest environmental and quality standards to produce products that are recognised and sought after globally.
The mill Sims Metal uses to process scrap metal was previously powered by a liquid resistance starter (LRS). Andrew Butcher, Regional Director for Asset Development at Sims Metal says, “we were noticing frequent and exponentially high energy spikes occurring on the supply network as a direct result of load being processed in the mill. This caused significant increases in energy consumption and was additionally leading to unexpected downtime due to necessitated equipment maintenance.”
Arvind Sharma, Business Development Manager for Drives at ABB Australia supported Sims Metal to identify the best technological solution to overcome the challenge. An ABB ACS6080 medium voltage industrial drive was selected to replace the LRS unit being used.
The ACS6080 is an all-compatible drive offering high performance in critical applications. Sharma says, “industrial operations such as this, which are running demanding processes, require high performance motor control to enable plants to operate more efficiently, produce higher-quality output and increase profitability.
In this case just as importantly, we wanted to strengthen Sims Metal’s business plan to lower their energy consumption and limit the peak demand in this application in turn lowering their environmental impact.”
The ACS6080 features a modular design that enables it to be configured for single or multi-motor applications, and to be tailored to individual requirements. Extremely high levels of safety, both for people as well as equipment, are delivered via an arc-resistant design and certified functional safety features. It offers increased productivity due to new MP3C motor control.
In the processing mill metal shredding application, by implementing the ACS6080 drive, Sims Metal was able to upsize the accompanying motor to a 6-megawatt rating to induce more power which has overall led to higher processing throughput with reduced energy demand.
Image currently unavailable
Image currently unavailable
Image currently unavailable
Image currently unavailable
Image currently unavailable
Image currently unavailable
Image currently unavailable
Image currently unavailable
Image currently unavailable
Image currently unavailable
Image currently unavailable
Image currently unavailable
Image currently unavailable
Image currently unavailable
Image currently unavailable
Image currently unavailable
Image currently unavailable
Image currently unavailable
Image currently unavailable
Image currently unavailable
Image currently unavailable
(L-R): ABB’s Arvind Sharma, Business Development Manager for Drives, and Andrew White, Service Sales Business Development Manager at the entrance of Sims Metal, Brooklyn, Victoria in Australia. (L-R): Luke Schouw and Arvind Sharma, from ABB Australia, with Sam Pisani from Sims Metal, along with Andrew White from ABB, standing in front of the metal shredding machine powered by ABB’s ACS6080 medium voltage drive and motor also supplied by ABB’s packaged offering. Truck arriving at Sims Metal, preparing to be weighed. Sam Pisani, Victoria State Engineer at Sims Metal, and Andrew White from ABB, preparing to inspect the newly installed ACS6080 medium voltage drive onsite at Sims Metal. A closer look at ABB’s ACS6080 medium voltage drive on site. ABB supplied transformer, newly installed onsite at Sims Metal. ABB flowmeters installed to support the drive’s cooling tower operations at the plant.
The previously experienced high energy spikes with the LRS unit are no longer an occurrence. The electronic control of the ACS6080 drive is so rapid that spikes are virtually non-existent.
"The application is now using less power thanks to the improved power factor (0.95) where it was previously (0.75).”
Butcher says, “we have a power meter on the incoming system that measures monthly energy usage. We had the LRS in the old system at the start of the month of July 2022, and after a comparison of energy usage where the ACS6080 was installed at the end of the month, we could see a drastically improved graph analysis.
Additional notable observations shared by Sims Metal includes the subsequent energy cost savings and the higher tonne per hour in material processing thanks to the increased power of the system overall. This is giving them more opportunities to keep previously discarded materials in use for as long as possible to champion economic, environmental, and social value.
"One month after the installation of the new ABB drive shows an average power consumption saving of 2,000 kilowatt hours. That’s quite significant particularly given we believe this to be the world’s largest system application for metal shredding."
Regarding positive analytical results observed so far, Butcher says, “the results we’ve seen so far speak for themselves. Looking at the data of our site energy meter one month after the installation of the new ABB drive shows an average power consumption saving of 2,000 kilowatt hours when compared to the power usage of the system which utilised our old LRS unit.”
That’s equivalent to avoiding the greenhouse gas emissions of approximately 5,661 kilometres driven by an average gasoline-powered passenger vehicle1 or 2.14 tonnes of carbon dioxide avoided.2
Butcher continues, “that’s quite significant particularly given we believe this to be the world’s largest system application for metal shredding.”
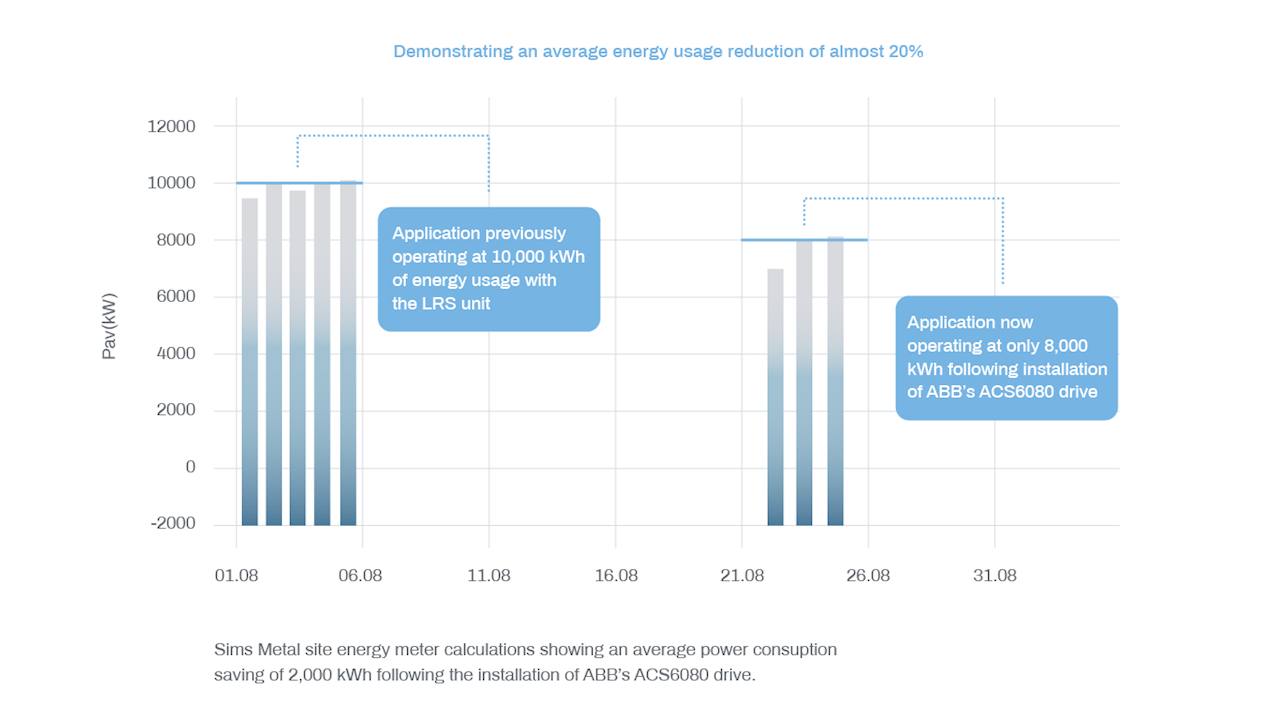
Andrew White, Service Sales Business Development Manager shares, “it’s always satisfying to know we helped a customer address all their major application concerns. In this case reduced mechanical issues, decreased maintenance requirements, and reduced points of failure throughout the drive train overall.”
He continues, “this leads to improved process production output and processing speed for Sims Metal. Given ABB’s local service team will be proactively providing components and support for years to come I am confident Sims Metal will continue to have a positive experience.”
Sims Metal recently received a $20,000 AUD Victorian Government Business Recovery Energy Efficiency Fund (BREEF) Grant thanks to their proven initiative to implement more energy efficient technologies into their operations, including the ABB drive.
1 SOURCE: EPA (2021) calculator.
2 SOURCE: Australian Government - Department of the Environment and Energy carbon calculator.