ABB’s subsea technology is putting oil and gas platforms on the sea bed
Putting an oil and gas production facility on the sea floor has been one of the holy grails of oil and gas exploration. Located at the bottom of the sea, it would be fully automated. Relocating oil platform workers to shore-based control rooms takes away much of the physical risk, greatly reduces operational costs, reduces the energy needed to recover it, cuts marine pollution and simplifies decommissioning. It can even boost oil production due to the increased flow and pressure of the stream resulting from being closer to the reservoir. While the technical challenges of this quest are formidable, the payoff will be huge.
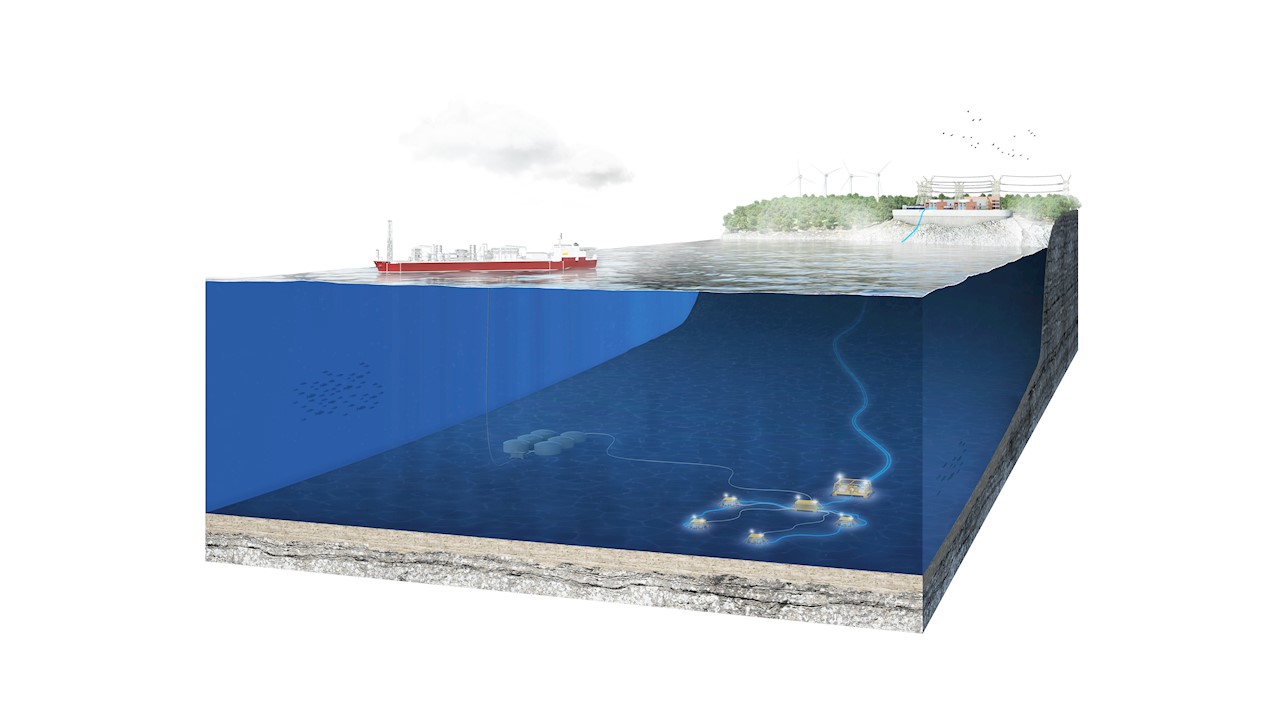
As a pioneering technology leader, ABB has a long, rich history of developing innovative solutions to technical challenges. Its researchers continually look ahead, and nothing excites them as much as cracking a previously impossible problem.
However, subsea oil and gas exploration is done in an extremely harsh environment. New technology that goes beyond today’s current capabilities is required. The target of a five-year Joint Industry Project (JIP) being led by ABB and the Norwegian oil company Statoil is to develop the technology required to seamlessly power tomorrow’s underwater facility. Beginning in late-2013, ABB has been developing electrical equipment that can reliably provide up to 100MW of power (equivalent to what is needed to power a small city) to depths down to 3,000 meters over distances up to 600 km, and then to distribute the power to multiple users – pumps, compressors, etc. The equipment must operate at immense pressures in a highly corrosive environment with little or no maintenance.
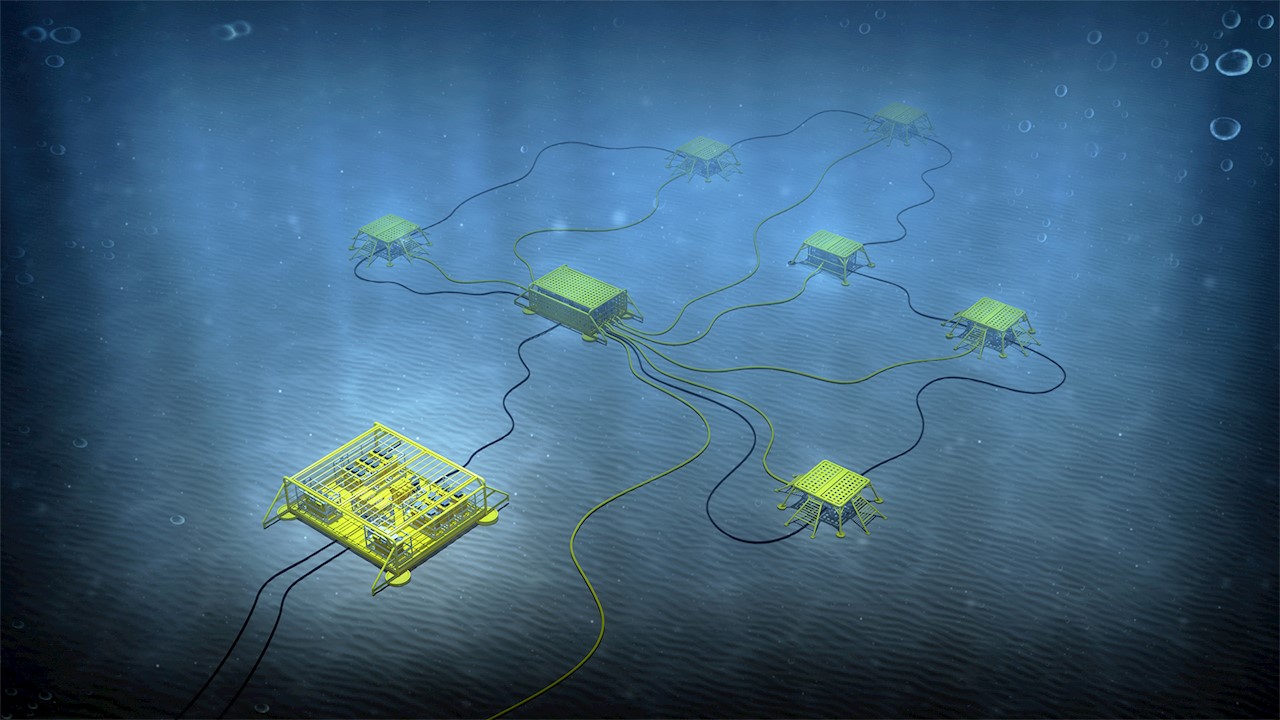
Over 200 expert ABB electrical engineers, physicists and chemists in test facilities around the world are working to develop these next-generation technologies for subsea power. In addition, four specialized subsea labs were created by ABB specifically for the project. Each subsea lab is equipped with pressure vessels to simulate 3,000 meter water depth. The lab in Oslo, Norway tests electronic components and printed circuit boards. In Turgi, Switzerland subsea drive power electronics are tested while power electronic components are tested at the research center in Daetwill, Switzerland. The Vesterås, Sweden lab tests chemical compatibility. The researchers have created a high-resolution digital facsimile of a subsea power grid and combined it with a control system that automates its operations while detecting and diagnosing problems before they occur. The hundreds of thousands of bits and pieces that make up a conventional oil platform have been replicated in digital form. Such an undertaking requires a complex network of sensors and measuring points far beyond anything used in a conventional processing plant.
Subsea technology and rocket science share a certain similarity. "Our work is similar to sending a satellite up in space,” says Jan Bugge, Vice President of subsea technology at ABB and Project Director of the subsea power JIP. “Both work in conditions that once the technology is installed, fixing anything is very difficult.”
While satellites can get the small amounts of power they need from attached solar panels, the separators, pumps and compressors located on the seafloor require vast amounts of power and have to be plugged into a source of electricity. For example, Statoil’s Johan Sverdrup oil field in the North Sea is powered with a 100 MW cable from ABB, which is enough electricity to run a fair-sized city.
The JIP’s initial focus was to understand how electrical components such as capacitors and transistors behave when subjected to pressures of up to 300 atmospheres, which is about four times greater than what a nuclear submarine can survive. The normal mechanical and electrical properties of materials change when they are subjected to this degree of stress, and those changes had to be understood at a basic physical and chemical level.
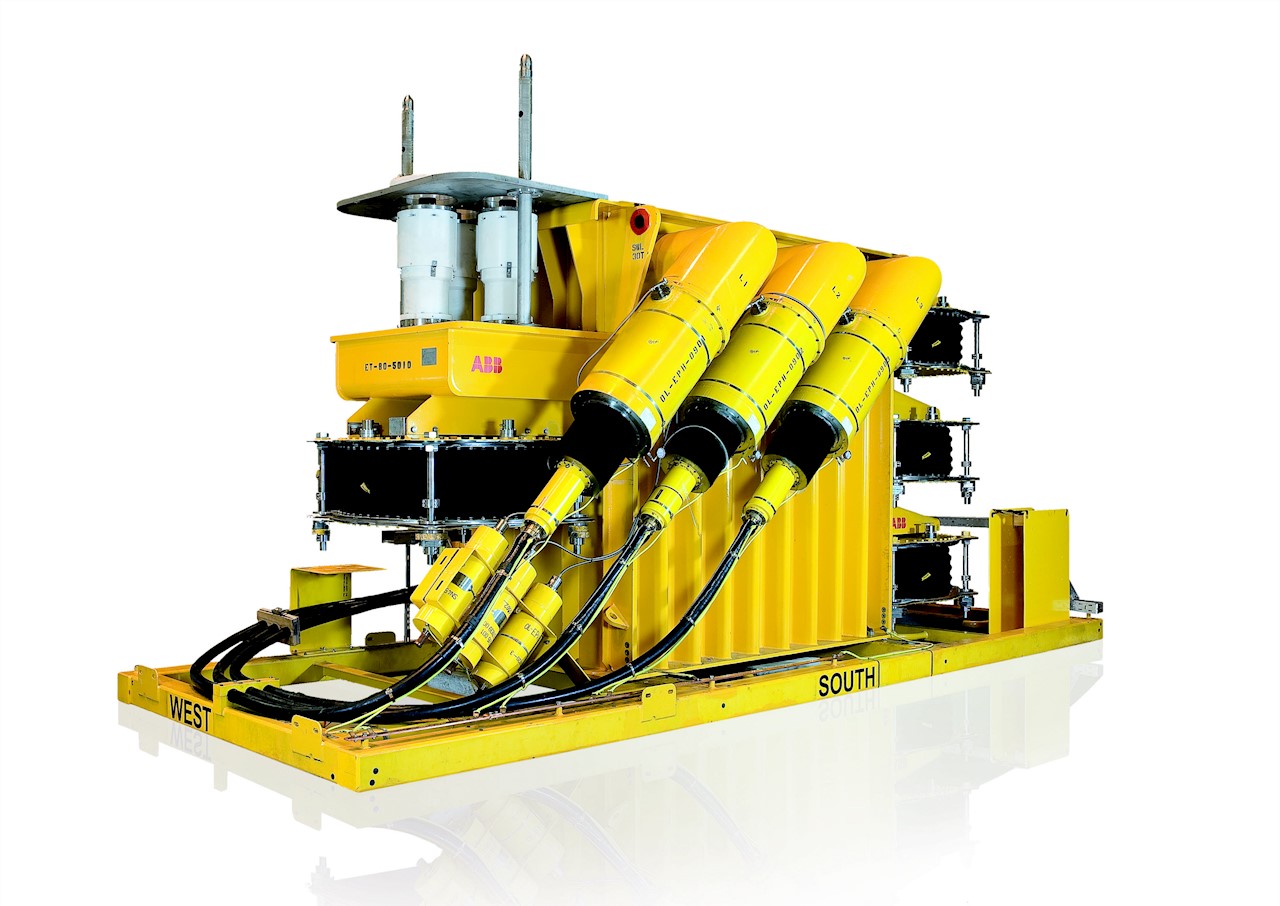
This investigative phase of the work was completed by April 2015. Since then researchers have been building individual components and putting them together to form sub-modules and full-scale prototypes. One milestone is due to be passed later this year when the first 100 tons drive module will be tested in shallow water. The complete set of subsea power products under development will be put together for an extensive 3,000 hour shallow water testing next year. The first installation of the subsea power products in the real offshore production site is expected to begin in 2020.
“When we started this project we knew what the key challenges were, but it’s taken a greater understanding of the physical properties and simulating 30 years of lifetime through accelerated tests to develop the technology,” says Bugge. “We are confident that the technology will behave the way we expect it to when it is bolted to the sea bed beneath a 3 km-high water column."
A highly complex system in such an extreme environment must be reliable. Therefore the project is focusing on FMEA (failure modes and effects analysis) to foresee what could possibly malfunction.
The main defense against operational failure in a system that can’t be maintained in the usual way is to build in redundancies and wire them to a monitoring and control system that predicts a failure before it can occur. “We have to think about all the possible things that can go wrong, we have to know how we can check if they are going wrong, and we have to be able to reconfigure the equipment to correctly adjust,” emphasizes Bugge. “We have to prove to our customers that the whole thing is going to be ultra-reliable because pulling up equipment from 3,000 meters costs a lot of money.”
Challenges like putting a platform on the sea bed is just one of the advances ABB is making a reality. Innovative ideas and visions such as these help industries do the impossible and go where others have not been before.