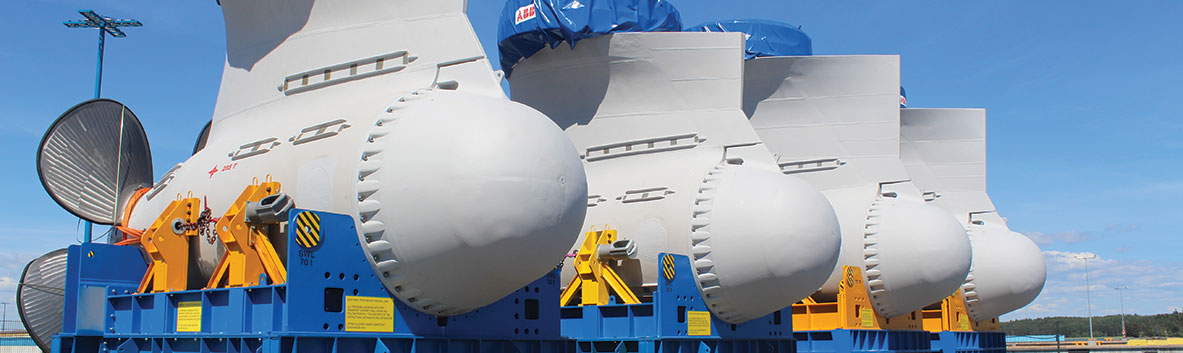
Ice class Azipods® ready for delivery
Ice Mode is the new control technology development from ABB Marine and Ports, commissioned within DSME HN2418, the first of the series of Yamal ice-class LNGs with Azipod®-based electric propulsion. Ice Mode is a set of connectivity and control functions that allow electric-propulsion LNG carriers of the Yamal type to increase availability for ice-breaking operations with dual fuelled engines running on boil-off gas. Running more often for longer periods of time, and with fewer requirements for the switchover from boil-off gas to marine diesel fuel, greatly increases the economy and safety of operation of the long sea ARC 7 ice-classed LNG carriers. The increase in availability and safety is only possible by leveraging connectivity between individual Propulsion Control Units (PCUs), a stable, mature, and capable embedded automation product from ABB Marine and Ports, delivered in its present form for over 15 years.
The issue at stake is dealing with fast load reduction in the AC electric network of a typical electric-propulsion ice-classed LNG carrier, which occurs when the propeller blades of Azipods® encounter large chunks of ice while milling. In such conditions, the rotor of the electrical motor stalls extremely quickly from mechanical braking on ice, and as a result, after the drive of the Azipod® thruster reaches its maximum torque capability, the produced power or speed of revolution of the shaft in rpm dips precipitously, thereby cutting the electrical load. Ordinarily, the unbalancing of load vs. produced electrical power would be seen by the prime mover – the diesel engine running on boil-off gas from the LNG tanks – as reduced mechanical load, freeing it to spin faster. The governor would then throttle down the engine in a ramp-down action that would need to be fast enough to counteract the almost instantaneous loss of load. However, since such a fast ramp-down is impossible when the engine is fired by gas, the engine would need to switch over to marine diesel-burning mode. To work together with the ramp-down action of the governor of the prime mover on the mechanical side, in these scenarios, ABB’s standard solution is to design the electrical system such that a part of the load is temporarily kept on the electrical network by using braking resistor load-banks. This gives additional time to the mechanical equipment to ramp down production in a way that is feasible for the gas-burning regime, at the expense of heating up the resistors.
The Ice Mode functionality takes this principle further, by connecting the individual PCUs, and allowing for the optimal use of various high-capacity electrical loads on the electrical network. First and foremost, assuming the electrical system is operated with closed bus-ties, more than the one load bank, with one connected to the DC link of the stalling pod’s drive, may be used. Additionally, provided that other Azipods® are not currently functioning at peak performance, part of the load may be taken up by those Azipods®. Of course, the redistribution of the electrical load is transitory in nature, since it is assumed that the originating event – the stalling or mechanical braking of the pod hitting ice, is temporary, and normal operation will be resumed.
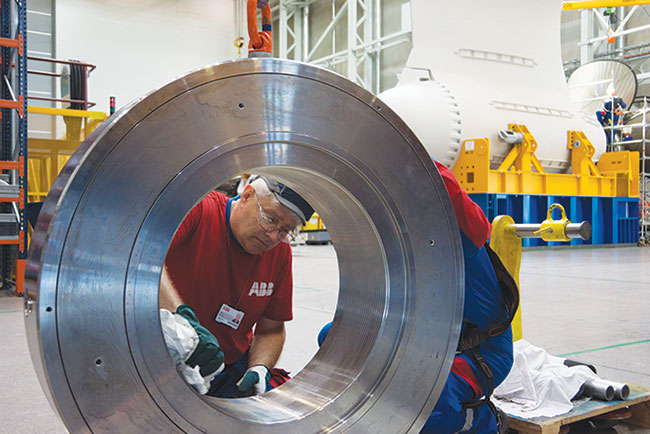
Ice Moe comprises two main parts: 1) the distribution algorithm that kicks in when a difference is detected between commanded power (as load) and the actual load on the system, and 2) the various protection mechanisms required for safe operation of the more complex interlinked system. The local calculation of load difference requires the mutual connection of all PCUs to one another, and effective and timely exchange of critical measurements. Likewise, protection functions require communication of critical state parameters and status feedbacks from all machinery, regardless of place of installation, to all PCUs. With ABB’s time-tested AC800MTM controller technology, and the Inter-application Communication (IAC) protocol for fast, high quality, and easily engineered communication between individual PCU applications, the required communication is easily implemented.
The Ice Mode algorithm dynamically and responsively shifts the instantaneous electrical load from the stalling or braking Azipod® to the other available loads in the network – available load banks and load reserves on other Azipods® that are not already functioning at peak performance. The algorithm provides a qualitatively different, better and increased level of availability of ice milling on boil-off gas than existing solutions. This is achieved by intelligently playing off the complementary capabilities of the remaining loads in the system, while operating with closed bus-ties. On the one hand, somewhat slower, but with extremely high-capacity loads presented by rotating electrical machinery, the remaining Azipods® are used to optimal effect if the braking or stalling is protracted. On the other, quickly reacting resistor load banks, albeit with limited capacity, and duty cycle are used for instantaneous reaction, but must be quickly unloaded to prevent build-up of heat and subsequent interlock in future events. Ultimately, a provision for feasible ramp-down of electrical power production by the diesels burning gas is also taken into account and accommodated.
The protective functions of Ice Mode concentrate on measuring the duration and intensity of over-torque operation of Azipods®, and on calculating the duration, intensity and duty cycles of pulses of current sent by the DC link in the Azipods®’ drives to the resistor load banks. Internal models are used to model resistive heat shunted to the resistor load banks and Azipod® exciter rotor diodes. The models are monitored and updated so that interlocks are safely emplaced, and alarms and events issued to denote that the capability of the system to handle further disruption is reduced due to the operational limits of the machinery.
Authors:
Matko Barisic
Senior R&D Engineer, ABB Marine & Ports, Norway
Børre Gundersen
R&D Manager, ABB Marine & Ports, Norway
Michal Robenek
Project Engineer, Drive System, ABB Marine & Ports, Norway