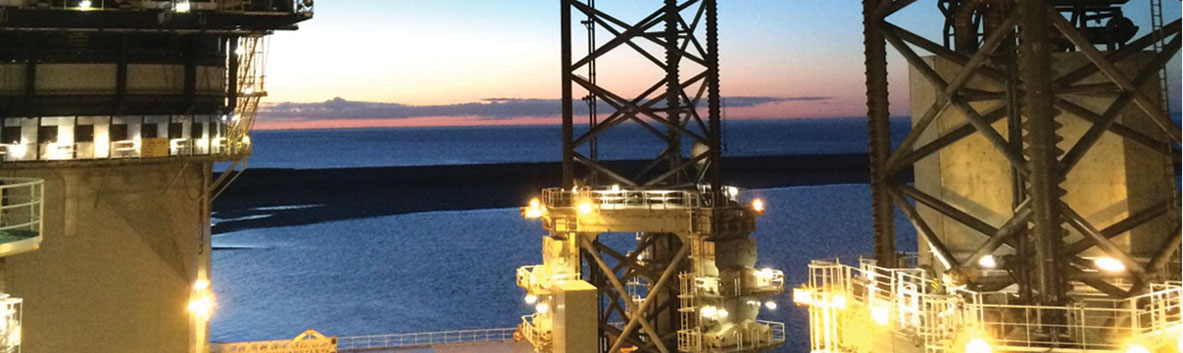
Abstract
ABB’s Jacking Control System (JCS) is an advanced VFD control system, which consists of variable speed drives and controls. The key advantages of a VFD driven jacking system include controlled start-up operations and accurate and precise speed control, resulting in improved efficiency. It optimises the power consumption under various working conditions, and enhances operational and system reliability. ABB’s jacking system is fully integrated with the electric power and automation systems on the high performance 800xA automation platform. Powerful inter-systems connectivity and advanced reporting functionality allow operation in a smarter, safer and more efficient way.
Background
Jacking systems are widely used in the offshore construction and drilling industries, such as in jackup vessels for oil drilling and offshore wind turbine installation and maintenance. Each vessel type places different requirements on the jacking system. There are two main types of jacking systems: pin-and-yoke and rack-and-pinion. For high-speed operation and deep-water application, rack-and-pinion systems are preferred. ABB’s jacking packages are designed to drive rack-and-pinion jacking systems.
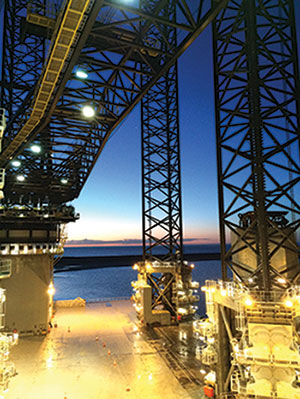
ABB jacking power system
ABB provides a complete jacking power system including power distribution, jacking drives, and motors. Different from the conventional electrical rack-and-pinion jacking system where the jacking motors are typical direct-on-line (DOL), ABB utilizes advanced variable frequency drives (VFD) and VFD motors to optimise power consumption under different working conditions and improve operating flexibility and system reliability. With the traditional DOL system, the jacking motors are directly connected to the power networks via jacking MCCs. The jacking speed is not adjustable during the operation unless two-speed motors are chosen. A typical jacking system for a four-leg liftboat uses 72, 120, and even up to 144 motors working in combination to share the load to elevate or lower the hull against gravity.
ABB jacking drives are selected from ABB ACS800 / ACS880 range of marine low-voltage drives. The variable frequency drives are configured in a multi-drive line up, replacing the traditional jacking MCCs. Each inverter is designed to drive a single jacking motor. The multi-drive is arranged by leg or by layer, depending on the jacking operation requirements. High power braking units and resistors are provided to dissipate re-generated energy during leg down operations or lowering the hull.
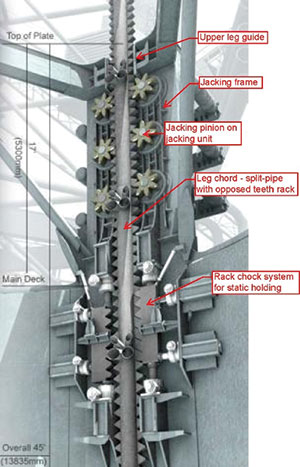
ABB jacking control system
ABB’s jacking control system is based on advanced 800xA control platform, which provides the operators with the information needed for jacking control and system maintenance. Its design principle is to provide simple, familiar controls for safety and ease of operation. It supports two or more jacking control stations and combines physical control panels with intuitive computer screens for information and monitoring. In addition, it is also possible to integrate the ABB remote diagnostic system (RDS), which allows connectivity to shore and provides remote system monitoring and expert services.
Figure 4 shows the HMI graphics of ABB jacking control system, which provides streamlined and intuitive design with optimised colour contrast to further improve effectiveness of operation and safety. Advanced reporting functionality enhances the smart, safe and user-friendly operation experience.
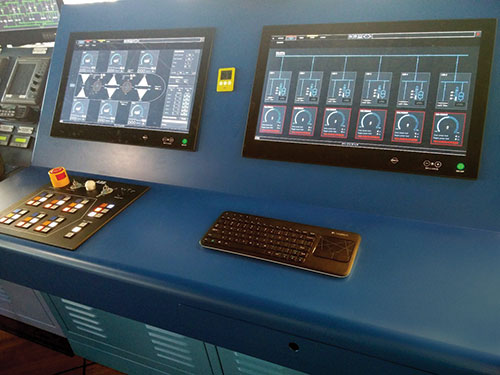
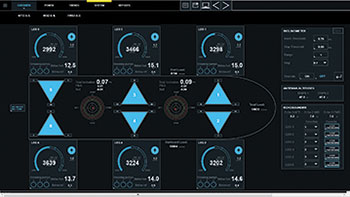
Benefits of variable-speed jacking system
With the traditional DOL system, the starting currents are very high, causing large voltage and frequency variations. The power system reliability is therefore significantly degraded when the jacking system is started, which causes vessel blackout. For jack-up vessels with dynamic positioning (DP) system, the transition period from DP to jacking operations is critical. Blackout while maintaining position close to an offshore construction site would be highly dangerous, and represents a risk that must be eliminated.
ABB’s VFD-driven jacking system has many benefits. First of all, standard marine approved electric motors can be used to replace the special DOL high-slip jacking motors, which is very expensive and with low efficiency. On the other hand, ideal brake control during starting and can be achieved with VFD control, where a torque memory function is used to transfer the load smoothly between the brakes and the motors. In addition, the jacking control system can be integrated with the power management system (PMS), reducing the risk of overloading the power plant to minimum.
Another issue with conventional DOL jacking systems is the inflexible jacking speed, with the jacking legs moving too fast for levelling and load-balancing operations, while moving too slowly during leg handling. Variable speed systems solve these problems. The operator can select a lower speed as needed in order to prevent rushing and promote safety. Higher speeds are available during leg handling, without the electrical and mechanical shocks caused by two-speed motor switching.
ABB direct torque control (DTC) VFD helps to enhance the system safety, especially during the starting/stopping period. The DTC control method makes it possible to control full torque at zero speed, and provides smooth starting or stopping jacking operation.
Compared with the scalar control (V/f control), an open-loop control method, DTC displays superior performance, especially during starting and stopping. During starting, the V/f control needs to estimate the frequency that will provide enough torque to hold the load without causing a jerky start. This might be difficult due to the variable load, which can vary from -10% to 60%. ABB has chosen a smarter way: the speed reference is maintained at zero speed while the closed-loop control is used to measure the load and to hold it without moving. Once the motor brakes are released, the speed reference is slowly accelerated to the set point. The entire starting process is very smooth and fast. Similarly for the stopping operation, the V/f control needs to estimate a frequency that will keep the load still without dropping or fighting with the brakes. ABB’s Direct Torque Control allows the motors to support the load while brakes are engaging, providing a smooth load transfer from motors to brakes.
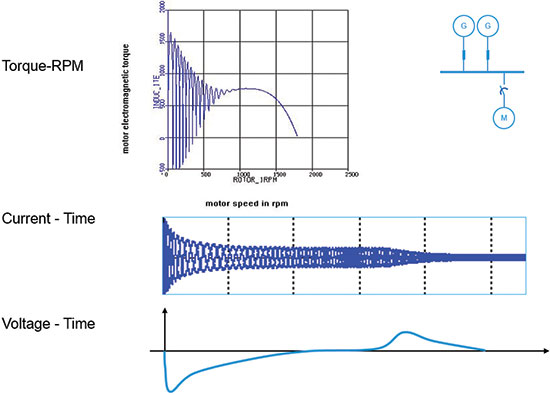
Case study
ABB has successfully delivered a complete jacking control system for Swire Blue Ocean wind turbine installation vessels Pacific Orca & Pacific Osprey. The vessels are currently operating in the North Sea. For this project, ABB provided the retrofit solution to upgrade the conventional DOL jacking system to VFD-driven jacking control system.
The jacking multi-drives are arranged by leg, and each leg is equipped with one jacking control unit (JCU). A redundant network is provided between the control cabinets and the bridge. As indicated in Figure 6, the jacking control topology, one central jacking control console works as the main operation station, as well as one local control panel for back-up purposes. In addition, ABB also provides power management system (PMS) integration on the same network.
The success of the Swire jacking project represents a significant milestone for ABB in the jack-up or liftboat market. As the leading electrical systems integrator, ABB continues to work closely with ship owners, builders and designers. The connectivity with the entire marine industry provides inspiration to design the optimal jacking control system for each vessel.
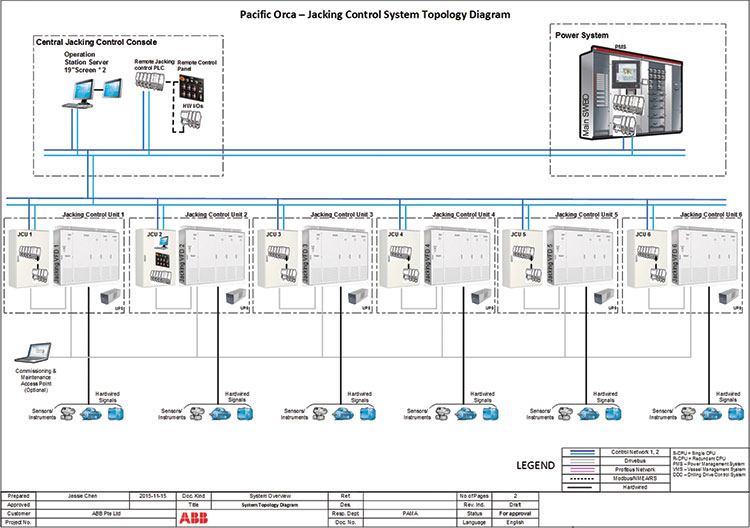
[1] Knud E. Hansen A/S “Design of Wind Turbine Installation Vessel – Pacific Orca for Swire Blue Ocean”
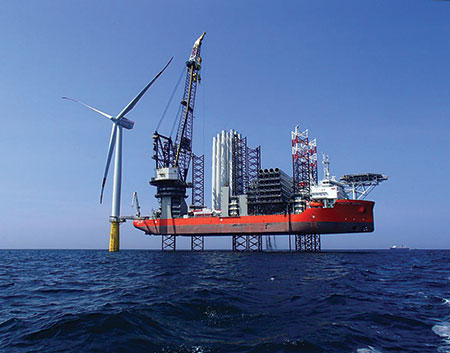
Authors:
Louis Kennedy
Senior Lead Engineer, ABB Marine & Ports, Australia
Jessie Chen
Product Manager, ABB Marine & Ports, Singapore
Ricky Chan
Technology Manager, ABB Marine & Ports, Singapore
Alf Kåre Ådnanes
Hub business unit manager, ABB Marine & Ports, China