Throughout the shipping market demand has stepped up for vessels with improved functionality and technical solutions that reduce maintenance cost and improve fuel economy. Against this background, DNV GL and ABS have released new rules that require a vessel to achieve high safety and reliability when running with a closed bus configuration.
DNV GL and ABS have one set of rules and notations for closed bus operation. Demand for newbuilds that comply with the new class requirements is increasing, as is interest in upgrading existing vessels to comply with these new rules.
Class rules have become much stricter. ABS now requires vessels to meet part of the EHS-P notation to be allowed to run with closed bus configuration. The new rules are also putting more responsibility on the power system integrator, with the need to prove that the delivered system can meet the necessary reliability and safety requirements. This involves more testing, dynamic simulations and extensive FMEA analysis.
Most of the sailing fleet can upgrade to meet the new requirements with the same high safety and reliability as new vessels. The technical requirements for DP3 closed bus and enhanced notations have many similarities, but the strictest one is the DNV DYNPOS AUTRO Closed Bus.
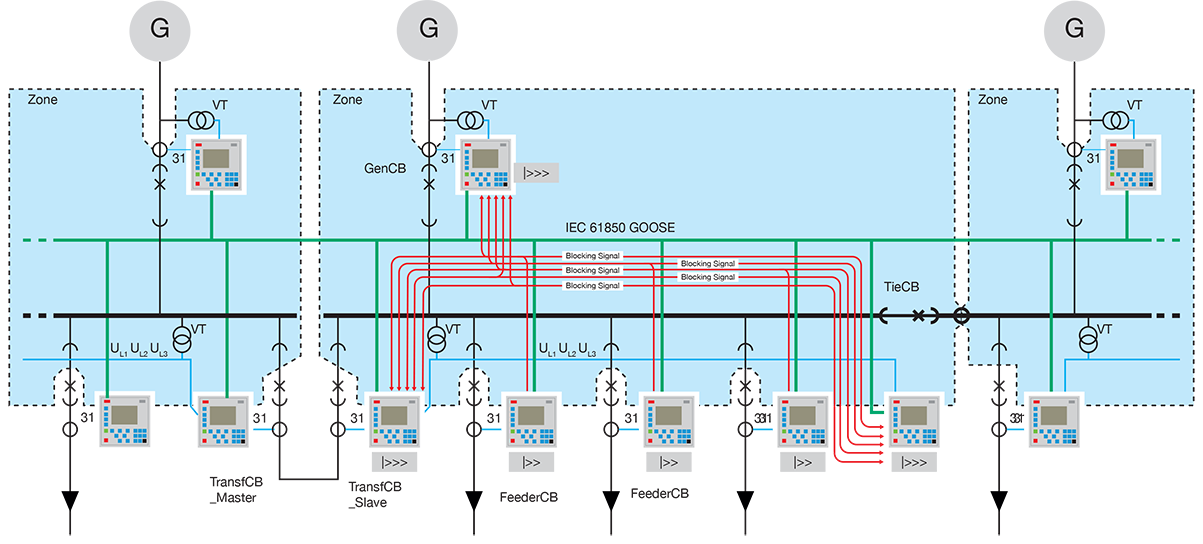
To get a better understanding of how to upgrade a sailing vessel with an ABB power and thruster system to, for instance, DNV DYNPOS AUTRO Closed Bus, we take an example from a typical drillship. Let us consider a drillship with six generators, six thrusters and six distribution transformers equally shared between three HV switchboards, and with three redundancy zones with A60 walls. All of the switchboards have two transfer lines/bus-ties that allow them to connect in ring, and we also make the assumption that the vessel has an HV switchboard with REM545/REF543 protection relay, fast recovery after blackout for the ACS6000 thruster drive, but no pre-magnetizing of the transformers.
Change to new generation relays
If we start with the HV switchboards, the REM545/REF543 protection relay can meet the zone protection and arc protection requirement by adding some CTs and arc protection to all of the compartments, but the self-diagnostics to find hidden failure are not available for this type of relay. Therefore, the relays must be changed to the new generation relays, RELION REM 630 and RELION REF 620. These relays are based on data communication peer-to-peer with GOOSE from the IEC 61850. Protection is block-based with time-delay protection as a backup, built-in hidden failure monitoring and the ability to communicate directly with the drilling drive and thruster system for immediate and precise load reduction in case of generator feeder trip.
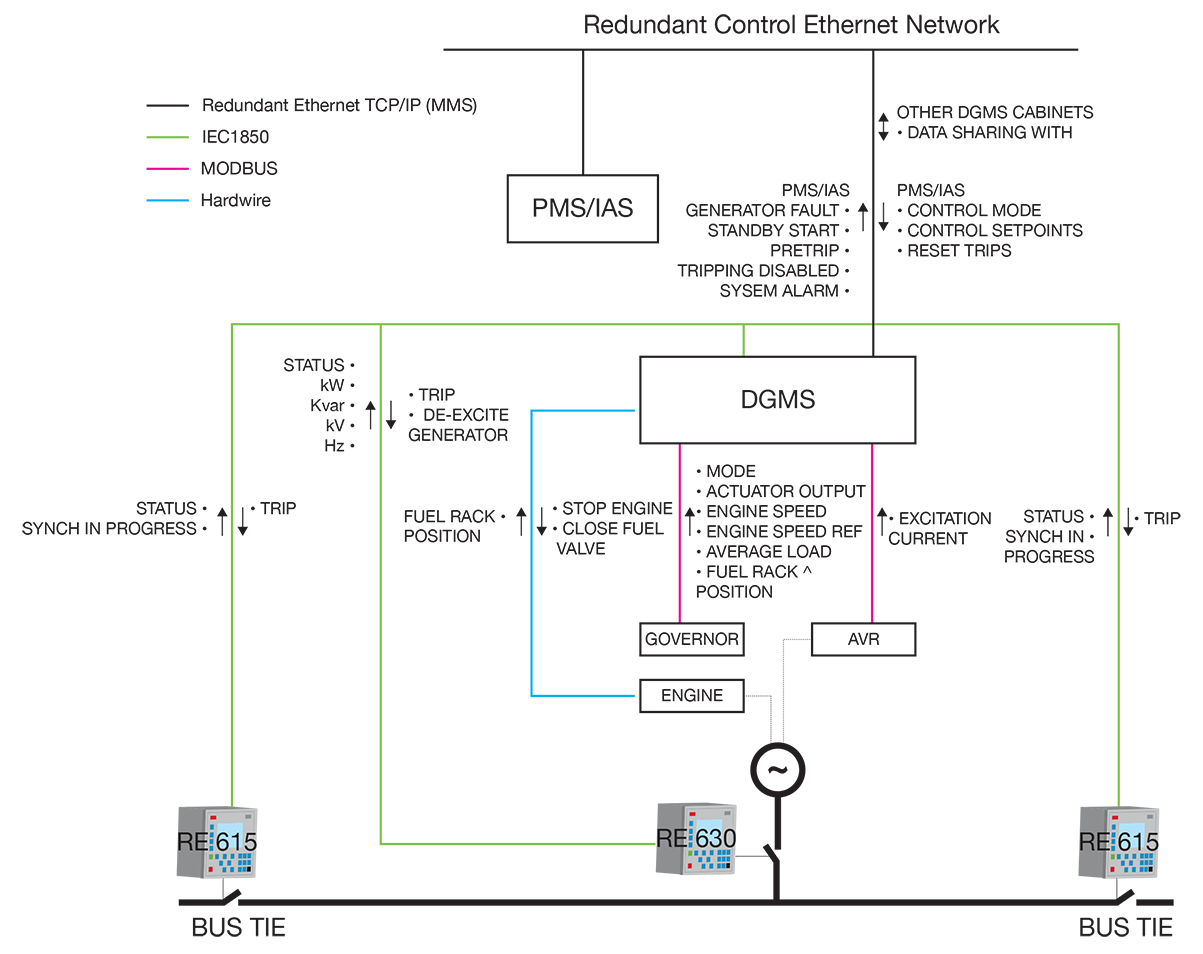
To meet the enhanced generator protection, the ABB Diesel Generator Monitoring System (DGMS) will be implemented. The DGMS will monitor the generator and the diesel engines for abnormal conditions and will be able to take action before a failure happens, be it a failure caused by over/under fueling, over/under excitation or an active and reactive power output, etc. Since this is seen as an extended part of the protection system, the DGMS should be delivered by the HV switchboard supplier.
In the event of a blackout, the transformers will be closed – preferably at the same time – to reduce the recovery time after blackout. To reduce the stress on the generators and the voltage drop during inrush, pre-magnetizing of the transformers should be implemented for the large HV transformers. This will also allow for an integrity check of the transformers before they are connected, which will avoid the connecting of a faulty transformer. If pre-magnetization is required, this must be evaluated on a case-by-case basis during pre-engineering.
Fault ride-through depends on essential HV and LV breakers not opening during a voltage drop when there is a short circuit. This is not a problem for the HV switchboard, but for the LV switchboard, a study must be done to evaluate the fault ride-through capability and adjustments must be made accordingly.
In an autonomous generator and thruster system, control and automation functions are decentralized. This means the auxiliary, electric auxiliary and water-cooling must be connected only within the same redundancy group and must not be dependent on external automation outside the redundancy group to be able to restart after blackout. For a drillship or semisubmersible vessel, the configuration must be evaluated during pre-engineering to look into how the configuration of the water cooling and auxiliary is at present connected. For the autonomous control, the thruster control will be upgraded with more functionality to be able to run a restart after blackout without a restart procedure from automation.
Many of the class requirements for the closed bus operation are quite similar, but the main ones are:
– Protection on the HV switchboard and improved functionality with zone protection
– Hidden failure monitoring of the protection system
– Enhanced generator protection
– Arc protection or insulated bus for the HV switchboard
– Blackout recovery time and procedure
– Pre-magnetizing of the transformers where high inrush currents are a problem for fast restart after blackout
– Fault ride-through
– Autonomous generator
– Autonomous thruster systems
Everything must work together

Blackout recovery has a time frame of 45 seconds from complete blackout to being ready for DP. To meet this requirement, it is necessary to look not only at the power system, but also at the diesel generators, automation and the thrusters. Everything has to work together. For the power plant to be ready for DP, it takes about 10 seconds from when the diesel engines are ready, if the abovementioned upgrades are implemented.
DNV GL requires new tests, studies and reports to approve the closed bus DP3 operation. These are a live short-circuit test on board the vessel, an FMEA report on the power plant and a dynamic stability study. The FMEA report must be made by a third party and must be done on the complete power plant delivered from ABB. If any remarks come out of this report, ABB will follow up and take necessary action.
Conclusion
The fleet of deep-water drilling vessels, built in accordance with previous classification rules, may be upgraded with solutions to meet the requirements of the newer and more stringent class notations. The efforts needed to upgrade the systems must be carefully analyzed and discussed with class societies to evaluate the content and scope of an upgrade. For some installations it might not be feasible. However, a range of technical solutions are available that can provide additional features for safety and availability regardless of full compliance or not with the newer notations.