Five Continents International Container Terminal (FICT) in Tianjin, China, is running at the maximum of its designed capacity, or even above it. To rapidly increase the throughput capacity of the terminal, FICT is modernizing its yard’s crane fleet of 31 manually operated rail mounted stacking cranes. The project is moving ahead at record pace, and the first batch of cranes was rebuilt, automated and commissioned for production within just a few months after the contract was signed.
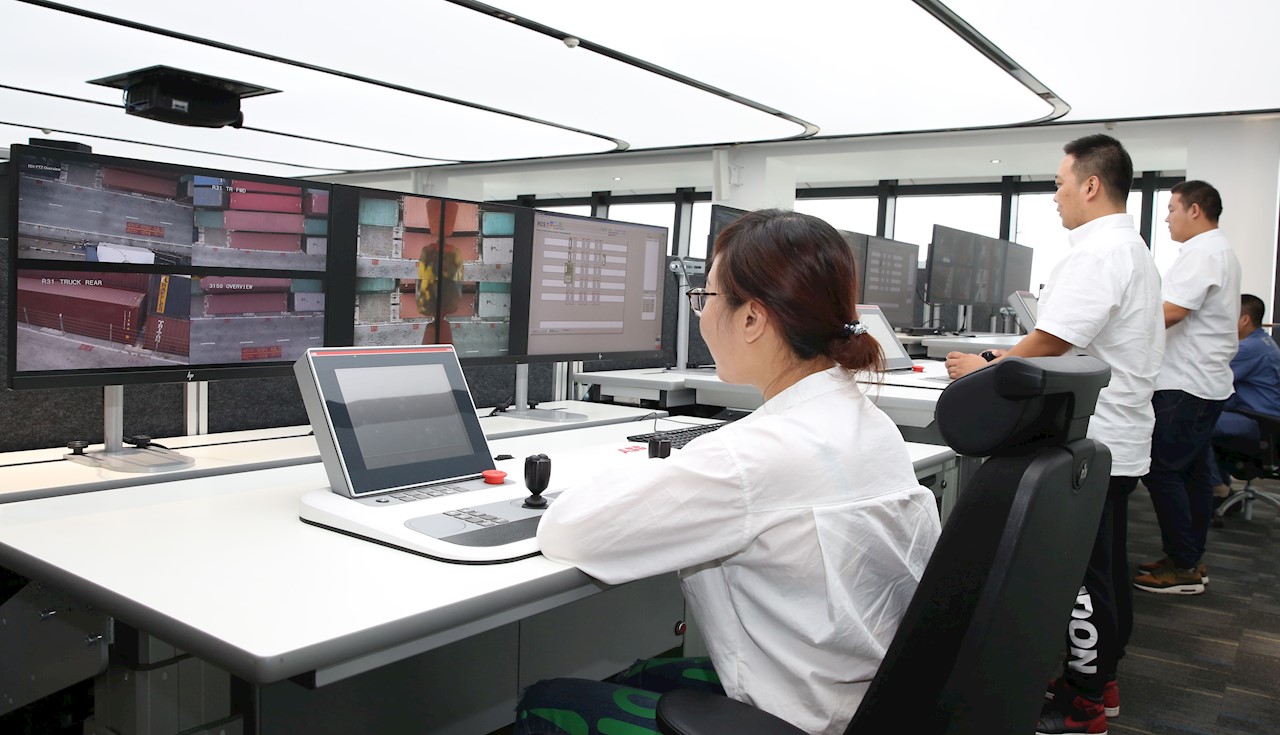
Port of Tianjin where FICT is located is the 10th busiest port in the world and the largest port in Northern China. The port is also the main maritime gateway to Beijing and serves as a link between the Northeast Asia, Central Asia and the Middle East.
FICT opened for operation in 2005. It was originally designed for annual throughput of 1.5MTEU, a capacity that has become insufficient in the “mega-age” characterized by bigger ships and increasing container volumes. An extensive modernization of the yard was initiated to increase the capacity and productivity of the terminal. “We analyzed the terminal’s operation and found that automating the yard was crucial for our overall productivity,” says Mr. Song Tianwei, General Manager at FICT.
As a result, the stacking crane fleet is now being equipped with ABB’s automation and remote supervision solution, and refurbished with ABB’s electrical systems delivered in a pre-assembled, containerized E-houses. The terminal remains fully operational throughout the modernization project.
Re-equipping the yard to ensure the terminal productivity
“We can already see that the cranes equipped with ABB’s automation system deliver a very stable performance of 30 moves per hour,” says Mr. Song. “With this performance, we will obtain more than 10 percent increase in terminal’s capacity at the completion of the modernization project.”
Mr. Song adds that, upon completion of the project, FICT will be able to utilize the yard space more efficiently. “At the same time, we will offer a better and safer working environment for our crane operators, who are very happy about the move to control room environment,” he says.
ABB is delivering the modernization of the cranes in collaboration with ZPMC. The stacking cranes at FICT are specifically designed for this terminal and have two vehicle lanes within the crane portal. Some of the cranes have a rope tower, while some have a reeving that resembles a ship-to-shore (STS) crane.
“FICT is a very technically competent customer, and they designed and specified the solution themselves. We tailored our solution to the unique mechanical design of these cranes and to FICT’s requirements, relying on our experience on automating nearly 900 stacking cranes worldwide,” says Uno Bryfors, Senior Vice President of ABB Ports.
Bryfors explains that automating stacking cranes without a rope tower is more demanding. “The sway control needs to handle trolley movement, gantrying and hoisting, and often all the three simultaneously. Our system is able to handle all of this and thus enables our customer to achieve efficient automated yard operation,” he says.
According to Bryfors, terminals around the world are now re-equipping their yards for more efficient operations needed to serve today’s mega ships. “Automating stacking cranes is our core competence and we have a strong track record in terminals in all main Asian markets. We believe that automatic stacking cranes and especially cantilever type cranes will be the preferred type of equipment for yards in many terminals around the world, including in China,” he says.