Håvard Knappskog, Product Owner, Power and Energy Management System (PEMS™), ABB Marine & Ports
Ola Hjukse, Product Area Manager, DS Power Products, ABB Marine & Ports
With the recent rise in the number of hybrid and fully electric vessels, battery power is establishing itself as a real force for change towards more sustainable and energy efficient operations. However, the full benefits of this technology can only be achieved with an advanced power management system on board.
The rise of the marine hybrid powerplant
In reducing operational cost, either directly by reducing fuel consumption or indirectly by avoiding emission penalties, the motivation to install batteries is increasing. This can be achieved in several ways.
- Certain areas have local restrictions on the use of fossil fuels close to harbors and cities, and in environmentally sensitive areas. A large battery can be charged with renewable energy from a shore connection for use during transit.
- Fuel efficiency is improved by having batteries supply transient loads or by replacing engines for redundancy purposes.
When employing batteries, operators must manage both the constraint of limited energy and a dynamic power capacity. Presenting the battery capacity as always available to the propulsion will result in a battery that will simply run flat. Careful considerations on how and when to restrict the use of the battery must be decided at the design phase.
The diesel engine is a mechanical device well known in the industry. A chief engineer can determine its health by feeling the vibrations in the vessel. A battery can cycle megawatts of power without any sound or vibrations. To take full advantage of the benefits provided by batteries in a marine power plant, advanced power management functionality is required.
ABB’s integrated Power and Energy Management System (PEMS™) provides functionality that ensures that all onboard energy sources work together in a smart and predictable way to ensure optimal use of the power plant at all conditions.
Using battery capacity fully
When choosing engines for a specific vessel, design decisions must be made. The most efficient gas fuel engines handle rapid load change poorly while a battery handles load change very well. In fact, load steps are almost irrelevant for battery operations. Some operations such as dynamic positioning (DP), docking or confined pilotage require additional running engines simply to handle the load variations or redundancy, leading to suboptimal fuel efficiency and excessive running hours. A battery can take the rapid variations and let the engines deliver the base load on the power plant leading to smoother loading on the engines themselves as illustrated in Figure 1. To maintain a certain state of charge, the mean battery load is shifted slightly up or down.
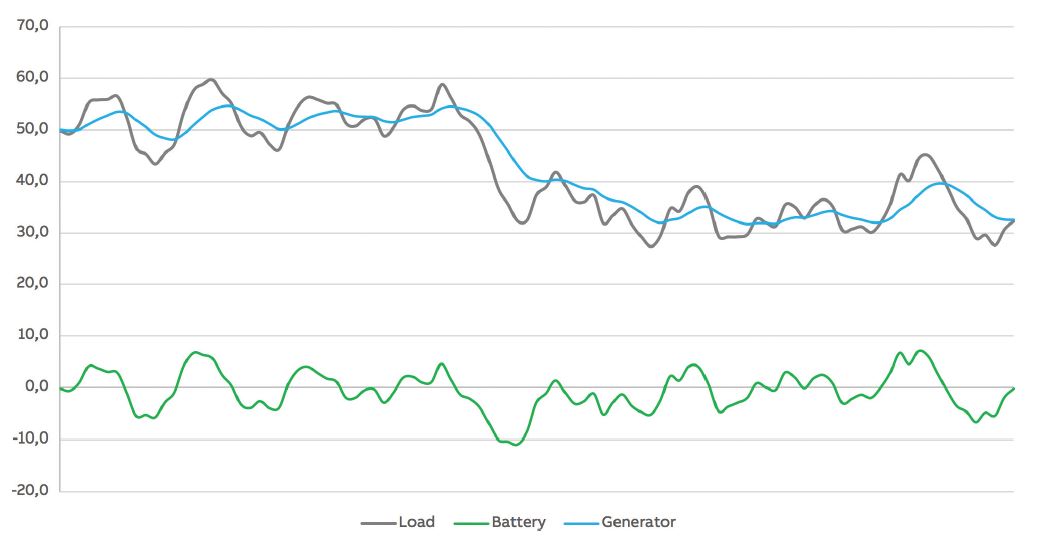
On vessels with high transient loads such as draw works, cranes or large pumps, there is a temporary demand exceeding capability of the connected engines. In a traditional power plant, either a power limitation on the consumers would be triggered or additional engines being connected to the grid.
It is no longer necessary to start additional engines when a battery can provide the peak loads. The result is fewer or smaller engines running at more efficient load level. PEMS™ will utilize the low load periods to make up for the energy taken from the battery.
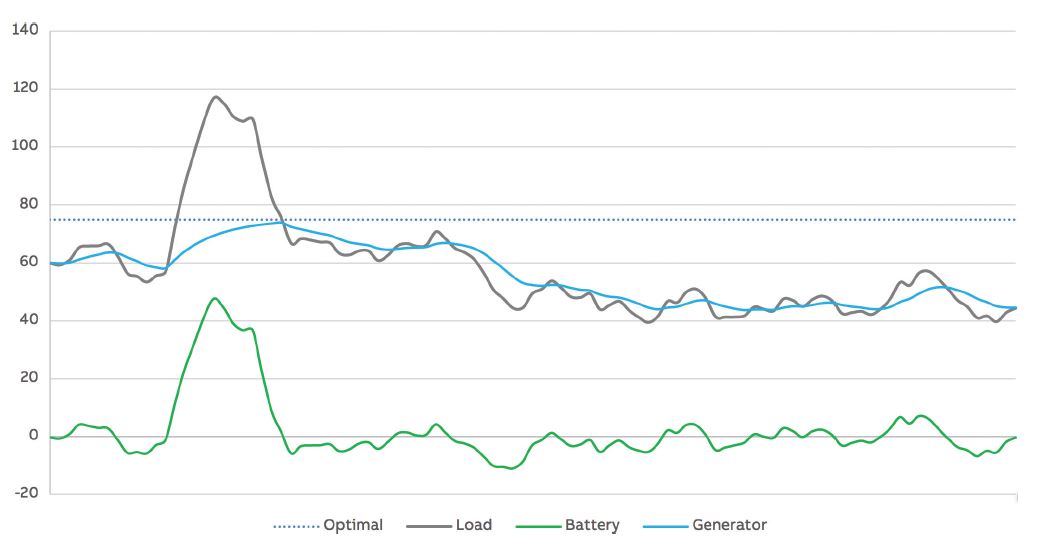
Vessels operating in a dynamic positioning mode (DP) have strict requirements for redundancy where the loss of one engine should not affect the maneuvering capability of the vessel. This often results in multiple engines running with low load to ensure enough available power if one engine were to malfunction and shut down. Operating a marine engine in this way is not optimal. Fuel efficiency is poor, and the accumulation of soot in the engine is high.
Because a battery can provide instantaneous power, it can serve as a backup eneregy source without delivering power to the grid. This enables the running of fewer engines during DP operation. The remaining engines are loaded closer to their optimal operational range.
PEMS™ can differentiate between the power needed for redundancy and the power available for engine support. This allows the power plant to fully utilize the benefit from backup capabilities and engine support simultaneously.
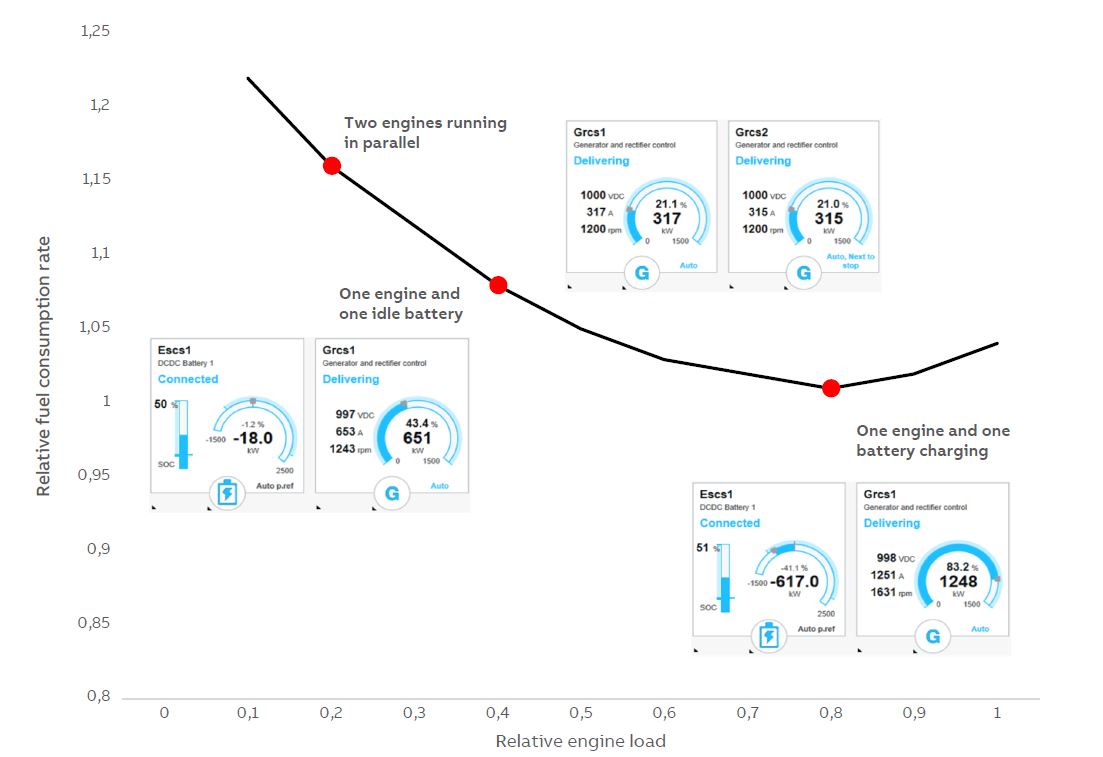
Aside from peak shaving and redundancy, the most obvious use case for batteries on marine vessels is similar to electric vehicles ashore. The battery can be charged by a shore connection to be used as the only power source for the entire transit, although the limited range makes this scenario most viable for ferries and short-sea shipping. The high efficiency of batteries and electric propulsion together with power from shore can lead to lower operational cost, depending on the energy cost at the point of connection.
Batteries can also be used as a primary energy source when zero-emission operations are desired for vessel equipped with hybrid power plants. Cruise vessels are facing local regulations that limit the use of fossil fuels within an area typically in or around ports or other sensitive areas such as fjords. It is imperative that the power plant can handle any transition without interruption to the power supply. PEMS™ is able to determine when it is safe to make a transition into zero-emission operation, and when engine start up is required.
Simple control of a complex power plant
Batteries provide great benefits to a marine power plant, but also add complexity when it comes to control. To obtain the full benefit of installed batteries, all energy sources must be controlled in a harmonious and organized way.
PEMS™ simplifies the operation of hybrid powerplants by allowing the operator to focus on how the powerplant should act, instead of having to focus on each individual power or energy source.
To determine the correct operational decisios, the operator is presented with a comprehensive overview of the current situation. The most important information is immediately recognizable at a glance and the operator is able to navigate to more detailed information easily and intuitively.
An intuitive, high performance user interface combined with a predictable control philosophy makes PEMS™ an easy to use power management system for complex power plants.
Image currently unavailable
Image currently unavailable
Image currently unavailable
Image currently unavailable
Image currently unavailable
Image currently unavailable
Figure 4. PEMS™ user interface in the ‘night’ mode Figure 5. PEMS™ user interface in the ‘day’ mode.