Mark Bos, R&D Engineer, ABB Marine & Ports
Martin Jirikowski, R&D Engineer, ABB Marine & Ports
Aleksi Eskelinen, Product Manager, ABB Marine & Ports
The number of containers shipped at sea has grown roughly tenfold over the past decades, and today’s container carrying capacity for the global container vessel fleet has surpassed 20 million TEU. The number of containers being transported by water is estimated to be 6 to 7 million at any given time. A marginal number of these containers never reach the destination port.
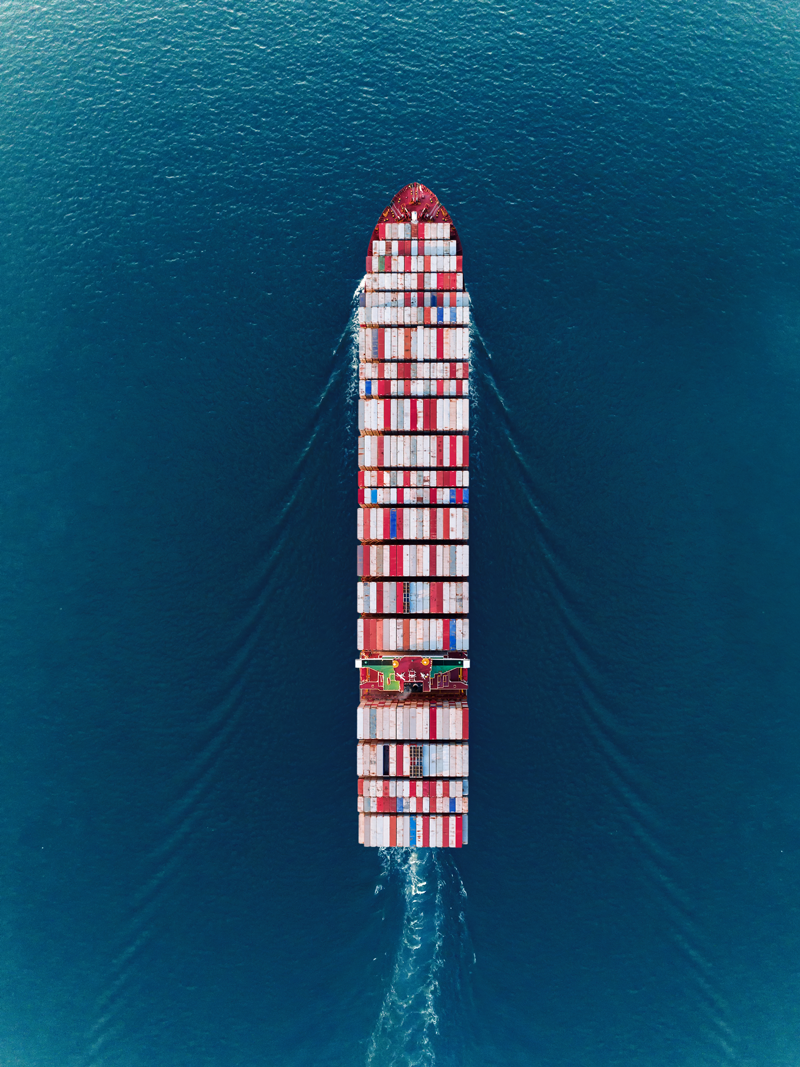
Exact figures are difficult to assess, but a total number of containers lost at sea is estimated to be roughly 1,500 per year. Most of these losses are associated with major incidents where large number of containers are lost in a single incident. However, for most incidents just a small number of containers has fallen off the vessel.
Containers lost at sea may have severe navigational safety consequences when left afloat at the sea surface or at the seafloor in shallow waters. Moreover, the environmental impact can be large especially when hazardous cargoes are transported.
Historical incidents have led to a range of responses from the industry, and several preventive measures are implemented at international level. Noticeable attention has been paid to container securing methods and measurement of container weights, where additional regulations are implemented to reduce the risks.
Most of the container losses are associated with adverse weather conditions, usually in combination with other factors. If the ship is not moving in the waves, a container won’t fall off, but when the ship is exposed to rough weather, each individual container is subject to forces on the container and its lashings, and can lead to failure of the lashing or the collapse of the structure of the container. In such conditions, even if a container is not lost at sea, the cargo inside the container might suffer considerable damage.
Forces on a container are related to the mass and accelerations of the container. Mass or weight can be measured easily and won’t change during the voyage, but the accelerations vary constantly. We distinguish mainly between vertical components and lateral components of the loads and accelerations. In our context, vertical and lateral is relative to the vessel. Too high vertical loads may lead to structural failure of a container. Containers can withstand compressive and shear forces up to a certain designed limit. The container at the lowest tier has the largest risk to collapse due to these loads induced by the weight of containers on top of it.
Lateral loads may lead to high forces in the lashings or container corner fittings and introduces the risk for the container to tip over if a lashing fails. Containers at the sides and close to the bow or stern of the vessel are more exposed to this risk.
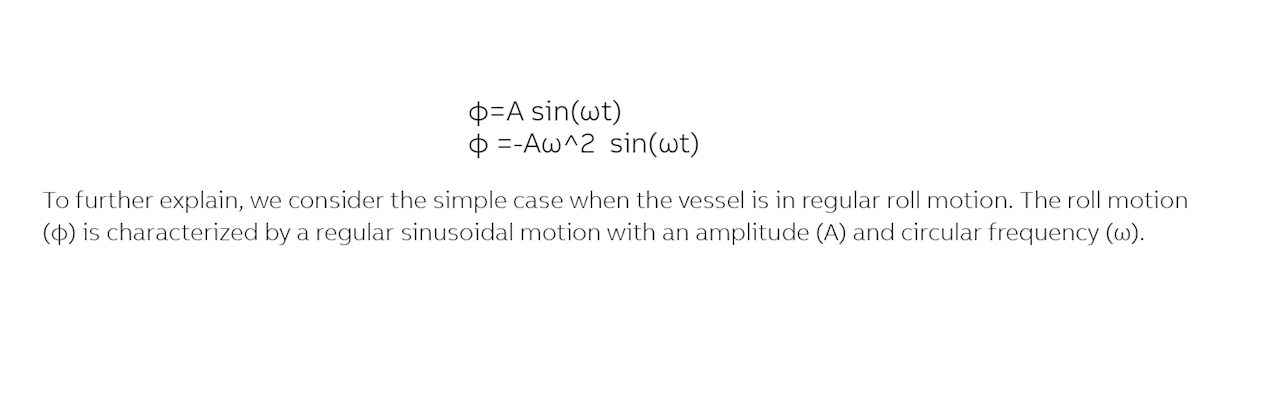
The second derivative of roll motion with respect to time is the angular acceleration. The further away from the axis of rotation the container is, the larger the accelerations due to roll motion. Without coupling to other motions like sway and yaw, the axis of rotation is at the center of gravity of the vessel. Acceleration is largest for the container at the highest tier and near the sides of the vessel. The direction of the acceleration is perpendicular to the plane defined by the axis of rotation and the position of the container. As a consequence, the container with the highest lateral load due to roll acceleration is at the highest tier and – depending on the distance to the center of gravity – be at the centerline or at the side of the vessel. Loads due to roll acceleration are illustrated in Figure 1.
Another contribution to the forces on the container are due to gravity. Gravity has a major impact on the vertical loads but also contribute to the lateral loads when the vessel is inclined. Vertical and lateral components of gravitation are depicted in Figure 2.
Figure 1. Contribution to the loads on containers due to accelerations in pure roll motion, and their lateral and vertical components relative to the ship.
Image currently unavailable
Image currently unavailable
Image currently unavailable
Image currently unavailable
Image currently unavailable
Image currently unavailable
Figure 2. Contribution to the loads on containers due to gravity for a heeled ship, and their lateral and vertical components relative to the ship. Figure 1. Contribution to the loads on containers due to accelerations in pure roll motion, and their lateral and vertical components relative to the ship.
The two contributions to the accelerations – gravity and roll acceleration – add up to the total acceleration exerted on the container. In the case of regular roll motion both components vary over time and have their extremes for the lateral acceleration at the same moment in time. Containers at positions higher than the vessels center of gravity will have the components amplified. The magnitude of the contribution from gravity is linear with the roll amplitude, but the magnitude of the contribution from roll acceleration is linear with the roll amplitude, and also square with the circular frequency and hence square with the period of roll motion.
The situation becomes much more difficult to understand if motions in all six degrees of freedom are considered at the same time. Not just the motion amplitude is important but also the relative phase shift of the different motion components. Besides this the behavior of the vessel depends on the loading condition and in particular transverse stability.
Accelerations are easy to measure with accelerometers. Velocity then follows from the integration of the acceleration over time. Further integration over time will lead to the motion of the vessel. If the accelerations are measured in all six degrees of motion – that is three translations and three rotations – and the structure of the vessel is rigid, then the acceleration and motion of every location on the vessel can be calculated from the measured accelerations. In reality vessels are not rigid, and the vessels structure does bend due to the varying loads on the hull. Also, a limited measuring accuracy introduce uncertainty in the calculations. However, when accelerations are measured at a minimum of three locations well distributed over the vessel these limitations can be overcome. Measuring and monitoring the accelerations is called motion monitoring. Motion monitoring may be used as a basis to quantify the risk of losing containers due to excessive accelerations in the wave conditions at the time of measurement.
Monitoring vessel motions make it possible to retrieve historical time series of accelerations for any location on board. This is valuable information when investigating an incident. This information is also useful during daily operations. Is the current situation still acceptable or critical for the containers and lashings? The real value for safe operation of the vessel comes when the vessel motions and acceleration levels are predicted for the near future and considered when making decisions for the operation of the vessel.
Weather forecasts include the wave conditions and are valuable information for the master to avoid unsafe conditions. Such information can help avoid sea areas where excessive vessel motions are likely to occur. However, the interpretation of a wave forecast with the aim to reduce the level of accelerations at the container locations is a task of too high complexity to do manually. Avoiding areas where the waves are the highest may not be effective if the distribution of wave periods and wave directions relative to the vessel have more impact on the acceleration levels than the height of the waves. Automation can help and translate the forecast wave conditions into forecast vessel motions. Knowledge of how the vessel responds to waves is essential to do this and theories have been developed to prepare such information with sufficient accuracy for onboard use. For ranges of wave directions, wave periods and wave heights in combination with a range in vessel speeds and loading conditions the response of the vessel in the waves is calculated and stored in a database.
Vessel response forecasting is the automated process to translate the wave forecast into a forecast for the motions of the vessel. ABB Ability™ Marine Advisory System – OCTOPUS is ABB’s solution for onboard use where vessel response forecasting is embedded in the system. ABB Ability™ Marine Advisory System – OCTOPUS does provide information about the current situation, and also helps to identify the risks related to the motions when changing heading or changing the speed of the ship. An example of onboard display is illustrated in Figure 3. Motions like roll and pitch are calculated for the full range of headings and ship speeds and are compared with a limit. Red areas indicate conditions where at least one of the given limits is exceeded. Amber areas indicate conditions where motions are acceptable, but close to the limit.

Vessel response forecasting is an aid to decision-making for operations at sea and is common practice for complex offshore operations. Nowadays vessel response forecasting is also introduced in the container shipping industry with the aim to improve the safety of the vessel, its crew and the cargo.
References
Standing, R.G. Review of the role of response forecasting in decision-making for weather-sensitive offshore operations.
BMT Fluid Mechanics Research report 347, prepared for Health and Safety Executive.