Samuli Hanninen, Key Account Director, ABB Marin & Ports
Major advances in icebreaker technology over the last 25 years come together in the ‘Universal Polar Icebreaker’, a concept that goes a major step beyond what traditional designs can achieve while using thoroughly proven marine systems technology, including propulsion.
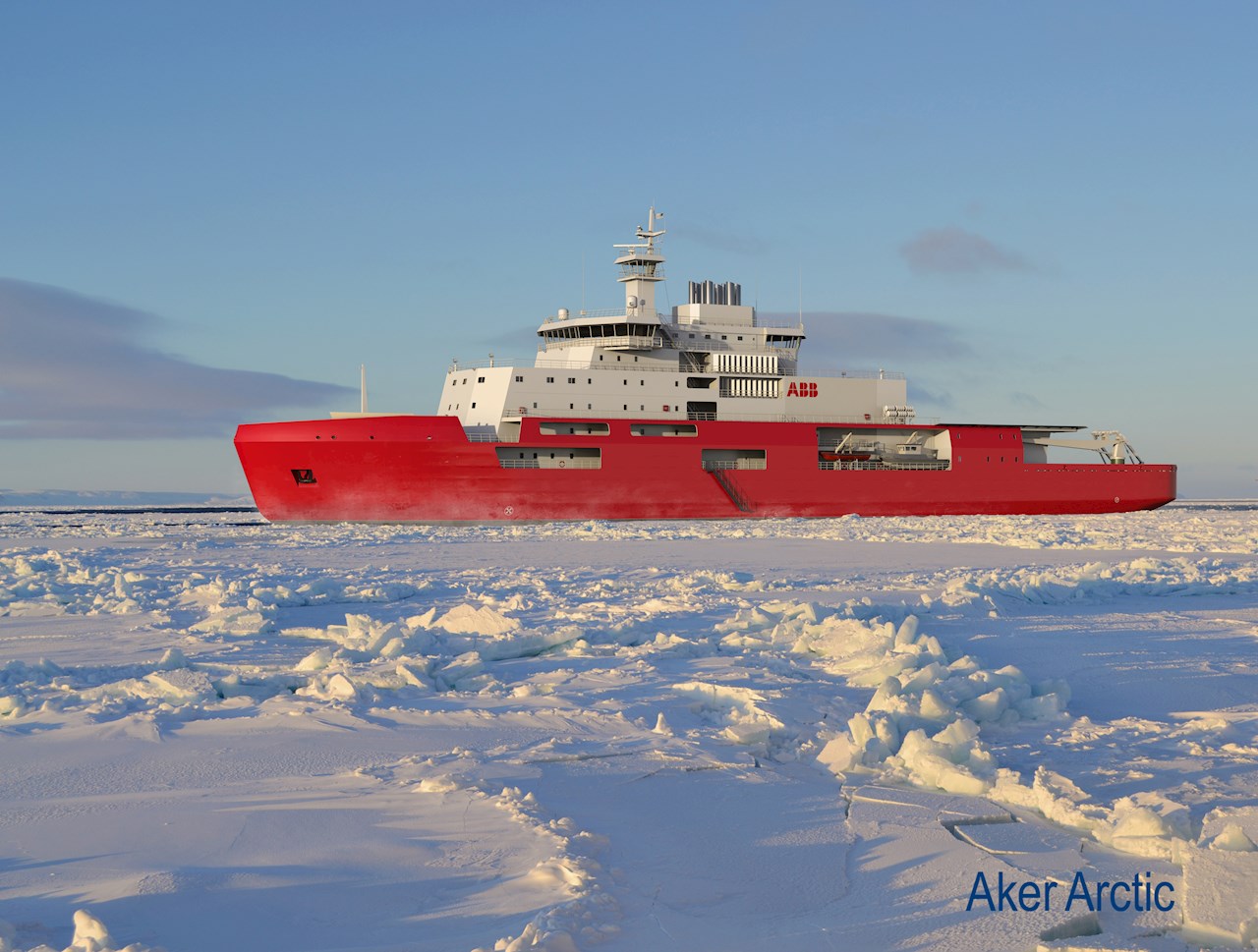
Polar Icebreaker main characteristics
Polar Icebreaker main characteristics
|
|
Length, overall |
135.3 m (444 ft) |
Beam, waterline |
25.3 m (84 ft) |
Draft, design |
10.5 m (34.5 ft) |
Depth, to upper deck |
16.5 m (54 ft) |
Displacement |
Abt. 20,000 mt |
Deadweight |
Abt. 5,000 mt |
Propulsion power |
2 x 17 MW Azipod |
Speed, max |
20.7 knots |
Icebreaking@3knots |
2.44 m (8 ft) |
Ice class |
PC2 Icebreaker |
Polar Icebreaker main characteristics
|
Length, overall |
Beam, waterline |
Draft, design |
Depth, to upper deck |
Displacement |
Deadweight |
Propulsion power |
Speed, max |
Icebreaking@3knots |
Ice class |
Cumulative experience in podded propulsion for icebreakers and ice load measurements provide the basis for a new generation of 17 MW Azipod® units that can drive the highest PC (Polar class) ships through ice.
One result is a completely new concept for a Universal Polar Icebreaker developed by Aker Arctic and ABB Marine & Ports with 2x17MW Azipod® units and the ability to operate in first year ice with a continuous thickness of 2.4m and penetrate thick Arctic sea ice ridges. The vessel would also enable maneuverability superior to all existing and proposed polar icebreakers.
The Universal Polar Icebreaker therefore presents an exciting proposition but it is important to understand that the systems and structural design behind the concept are proven and therefore provide precise precedents for vessel specifications. To recap, contributing elements include:
- Podded propulsion itself – the gearless steerable propulsion system featuring an electric drive motor in a submerged pod outside the ship hull, powered by an onboard diesel generator. ABB’s Azipod® propulsion delivers up to 20 percent better fuel economy, superior maneuverability, greater flexibility of design, lower maintenance and a smaller onboard footprint compared to conventional driveshaft systems.
- The Double Acting Ship (DAS™) principle – together with podded propulsion, the DAS allows vessels to operate independently without icebreaker assistance in challenging ice conditions. It provides better capability than legacy designs and requires less equipment, lowering construction costs and making the ship lighter and more fuel efficient. Hulls optimized for both open water (bow-first) and icebreaking (bow-first or stern-going) offer better performance in both environments using up to 50 percent lower power.
- Onboard power systems – power distribution systems designed to operate at variable frequency allow diesel generators to run at optimal levels (i.e., fewer units running, but operating at peak performance), improving fuel efficiency and reducing emissions.
- Advanced operations and maintenance – remote (onshore) monitoring and condition-based maintenance reduce the O&M (operation and maintenance) costs and increase uptime.
The Universal Polar Icebreaker is envisaged as adouble-acting vessel which features Azipod® propulsion at the stern and at the bow. This combination has been shown to outperform conventional alternatives in all the key areas.
Icebreaking capability
A typical double-acting icebreaker can break ice of up to six feet (91.44cm) thick at three knots bow-first, or up to eight feet (2.44m) thick running astern using the same power. When ice-going vessels equipped with Azipod® propulsion systems run astern in ice, the propellers mill the underwater part of the ridge, cutting a passage through.
Figure 2 is taken from the book “Northern Sea Route and Icebreaking Technology” (Dick and Laframboise, CRREL 1994) and depicts icebreaking performance for different ship concepts as a function of non-dimensional propulsion power required. Each vessel is plotted according to the ice thickness it can break (x-axis) and the power required to do so (y-axis). The purple line shows the potential of vessels with a modern double-acting hull, which clearly deliver better icebreaking performance than any conventional design.
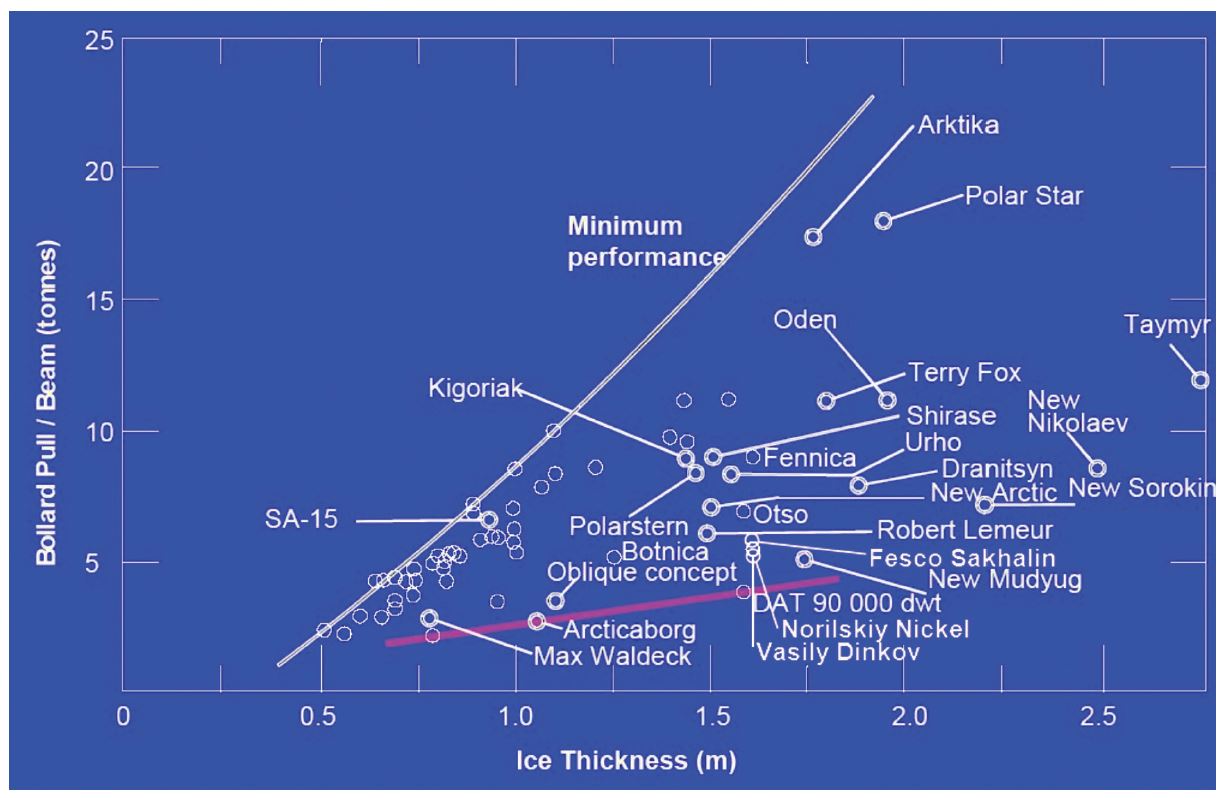
Maneuverability
Compared to the classic triple screw and single-rudder icebreaker, the improvement of turning capability in ice using podded propulsion is remarkable. Figure 3 depicts the turning circle of various vessels plotted against a given ice thickness. It clearly shows how podded icebreakers can turn in much tighter circles than conventional vessels.
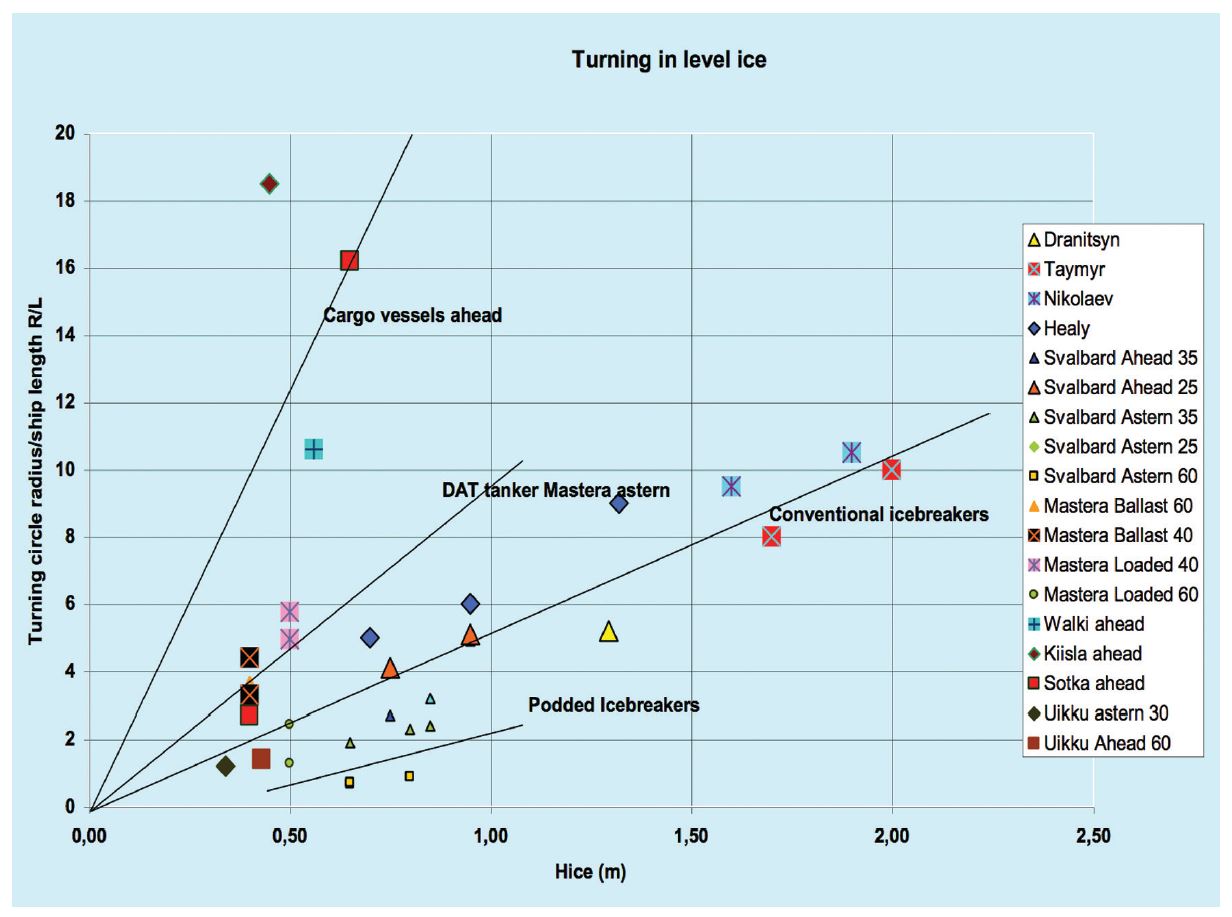
Fuel consumption
The DAS™ design combined with podded propulsion offers a clear advantage in fuel economy, not only in icebreaking operations but in open water. The hull design reduces friction while the superior efficiency of the electric motors means that more of the combustion energy is converted into thrust.
Figure 4 compares the performance of vessels equipped with Azipod® propulsion with conventional shaftline alternatives on a range of metrics. On almost every level, the combination of DAS™ and podded propulsion delivers superior performance.
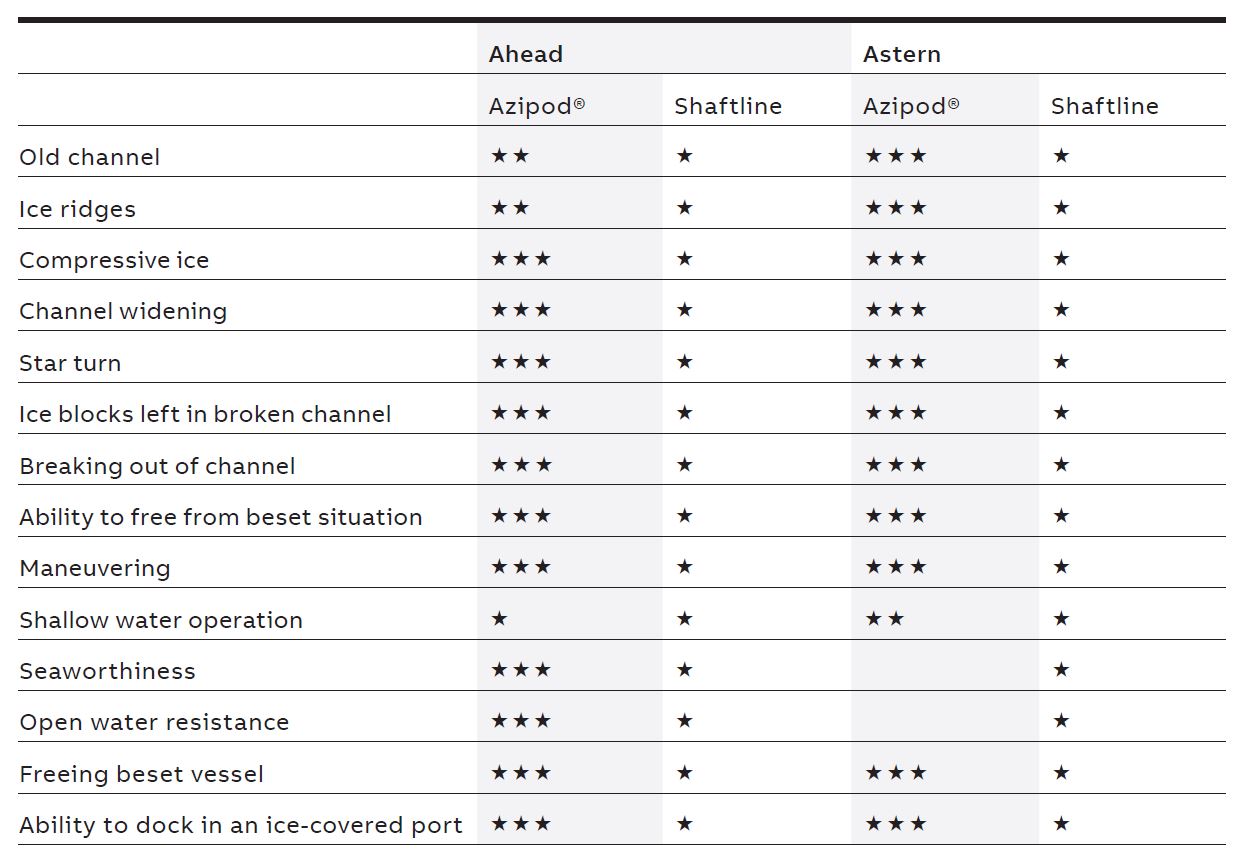
Affordability
There are numerous affordability advantages to DAS™ vessels with podded propulsion. First, podded systems are more compact and use significantly less equipment compared to traditional designs (Figure 5). By eliminating the need for the shaft, main engines, generators, rudders and auxiliary machinery, podded propulsion systems also reduce construction and equipment costs. In addition, space savings from the compact system provide the customer with more flexibility in ship design and mission. For example, a shipowner can use the extra space on board for additional fuel storage, providing greater endurance and mission capability. Shipowners can also reduce the overall size of the vessel, saving on materials.
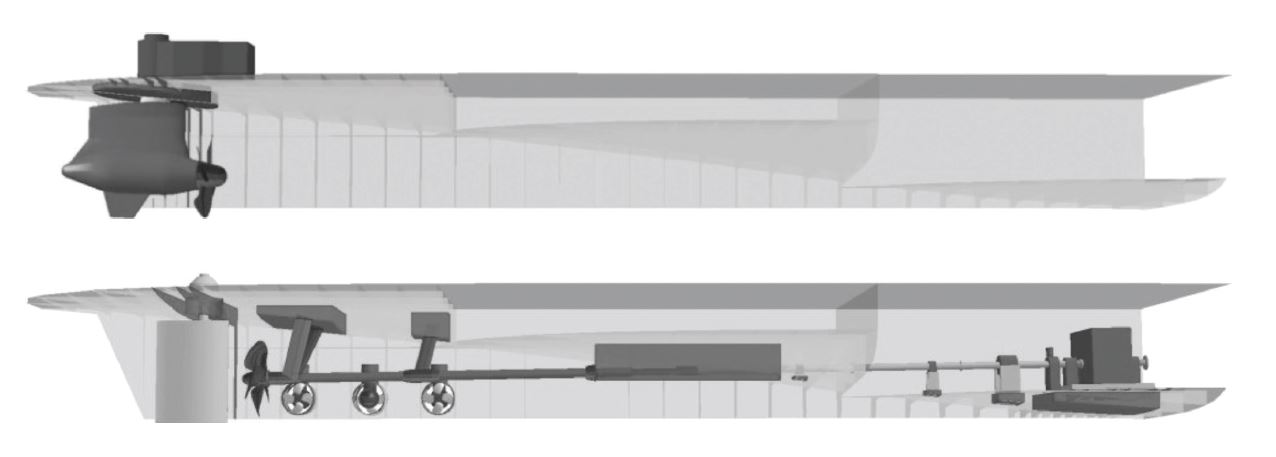
Azipod® propulsion design
Conventional propulsion design
Secondly, DAS™ vessels with podded propulsion are significantly more fuel efficient because the optimized hull design and the system’s reduced power requirement can in some cases lead to a 50 percent boost in efficiency over conventional driveshaft vessels, reducing fuel costs and increasing endurance.
The Dynamic AC, or DAC, power systems used in podded propulsion are designed specifically to operate at variable frequency, which allows the propulsion system to run at varying RPMs in response to changing demand. This has two benefits. It can deliver fuel savings of up to six percent compared to conventional power distribution systems and it allows the engines to run at optimal levels in relation to fuel economy and long-term durability while still delivering outstanding performance. This is especially important in the constantly changing conditions that icebreakers encounter.
A third cost advantage of podded propulsion lies in the fact that capital-intensive items such as Azipod® propulsors and steering modules are needed only in the final phase of the vessel construction process, so the costs of both are deferred within the production schedule.
Production risk
As exciting as many new marine technologies are, they must also be viable in an industrial manufacturing environment. It is essential to consider production attributes early in the design and acquisition cycle, especially in cases where equipment faces unique demand, as is the case for icebreakers.
Podded propulsion systems like Azipod® have proven themselves in terms of ease of installation: the single lift requires cuts the time in drydock and reduces schedule risk for the shipyard. Project risks are also reduced by the fact that there are fewer vendors and installation trades to schedule. Furthermore, the podded system eliminates the need for a gearbox, thrust bearing, shaftline, stern tube and seals, lubrication system, rudder and steering gear, stern thrusters and an interior electric motor, while the entire steel structure of the ship can be simplified, meaning less engineering and customization work.
Technology risk
Podded propulsion is also a proven technology that has been deployed on icebreakers for more than 25 years. In fact, two out of three icebreakers built since 1990 have used podded propulsion systems. Azipod® systems have accumulated over 3 million hours of operation without any ice-related damage. Vessels equipped with the Azipod® system have operated along the Northern Sea Route and around Svalbard for more than 20 years, continuously encountering multiyear ice without any reported problems.
ABB’s track record in delivering complete propulsion systems is substantial, including the drive train from generators to propellers along with ship automation, bridge controls and vessel efficiency management. ABB designs, engineers, manufactures and installs each of these components itself. Control over the full cycle of the Azipod® system also minimizes and mitigates schedule, design and construction risks while reducing the number of interfaces between customer and supplier.
Sustainability
In the context of icebreaking vessels, “sustainability” implies reliability, maintainability and supportability over the service life of the vessel. Costs associated with ongoing operation and maintenance are significant because icebreaking vessels remain in service for decades. Therefore, designing the next-generation polar icebreaker involves more than simply choosing the right components. Vessels equipped with ABB’s Azipod® propulsion system have enjoyed outstanding reliability since their introduction. As of 2018, Azipod-equipped vessels boasted availability of well beyond 99.8 percent.
To ensure peak performance, a modern ship should nonetheless utilize the same kinds of monitoring, service and maintenance practices that are used so effectively in onshore industrial environments. Experts armed with data from onboard sensors can provide essential support to vessels in remote locations.
ABB has a long history providing such data-driven intelligence, both on shore and at sea, and recently established a 24/7 monitoring center at its Helsinki facility. The company is already monitoring more than 700 ships worldwide and expects to increase that number to 3,000 by 2020. The Helsinki facility, like a similar one opened in the US in 2018, enables operators to identify and address potential problems early, reduce downtime and schedule risk.
Polaris is the first icebreaker to have benefited from a full size, bow mounted Azipod® unit and started her first season in January 2017. As a DAS™ vessel, Polaris has three Azipod® units – two in the stern and one in the bow.
Generally, the ice performance of Polaris has fulfilled and even exceeded expectations, subject to certain operational refinements.
Following initial trials of the ship’s ice management capabilities with stern propellers running with different steering angles and powers, for example, Polaris was kept in position using bow propeller thrust. While the propeller cleared the area behind the ship efficiently, the operation was not energy efficient. Better energy and time efficiency is achieved by keeping the ship in motion, with the hull breaking the ice and the propeller creating an ice-free area.
Another refinement was made after trials of oblique operations – the method used by Polaris to cut a wide channel by steering at an approximately 40 degree angle, with total power of 13 MW. Here, the test’s success was reliant on the ability of the highly experienced master to keep the ship on course by manually controlling all three propulsors. A more practical way to make a wide and clear channel involves turning stern propellers inwards so the propeller blows ice to the sides of the channel. This method is in constant use when assisting ships in ice.
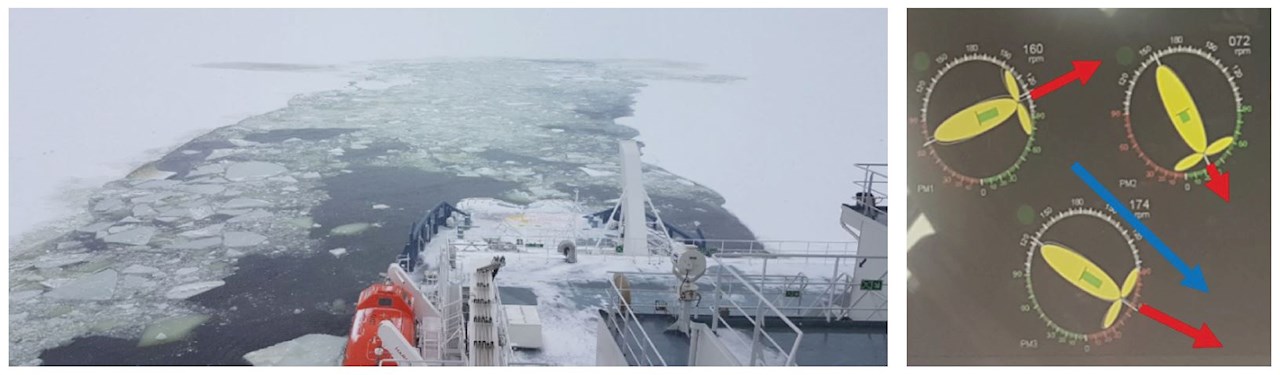
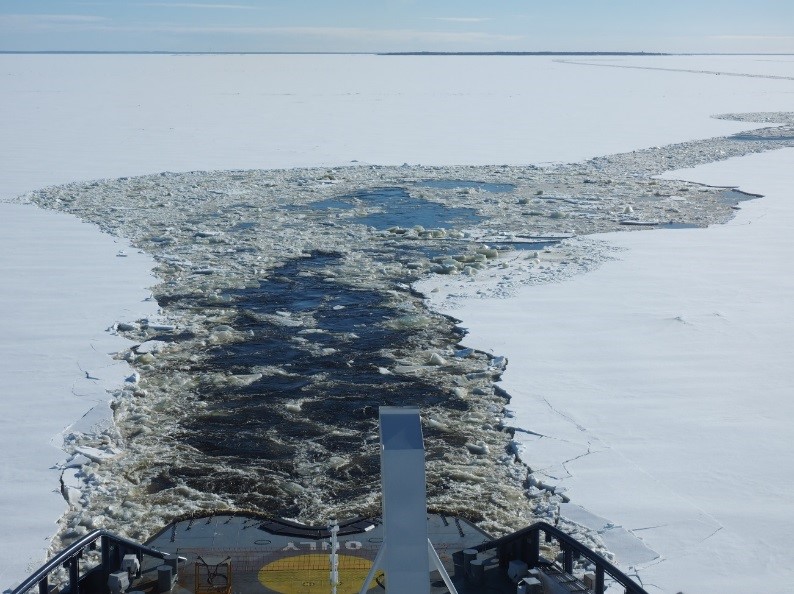
Some adjustments were made after a run made in the ice ridge field. Because of the high speed of 10 – 15 knots, the run proved to be the highest loading situation in the ice trial voyage. The bow propulsor loads were the highest, but significantly lower than the maximum design loads for the propulsor.
The Finnish icebreaker Polaris has now seen two winters of navigation in the Northern Baltic, with its ice breaking duty time amounting to about 1,500 hours per year. Most of the time operations have called for less than half of the ship’s maximum propulsion power. After two years of operational experience, the maximum loads measured were about 40 percent of design loads, see Figure 8. It can be concluded that the maximum loads experienced by bow and stern mounted thrusters are of the same magnitude.
ABB has measured the ice loads on the bow and on one of the stern Azipod® units and concludes that Polaris can be operated without limitations, as with other Baltic icebreakers. When utilizing its unique capability provided by the bow mounted Azipod® unit, the vessel outperforms its contemporaries.
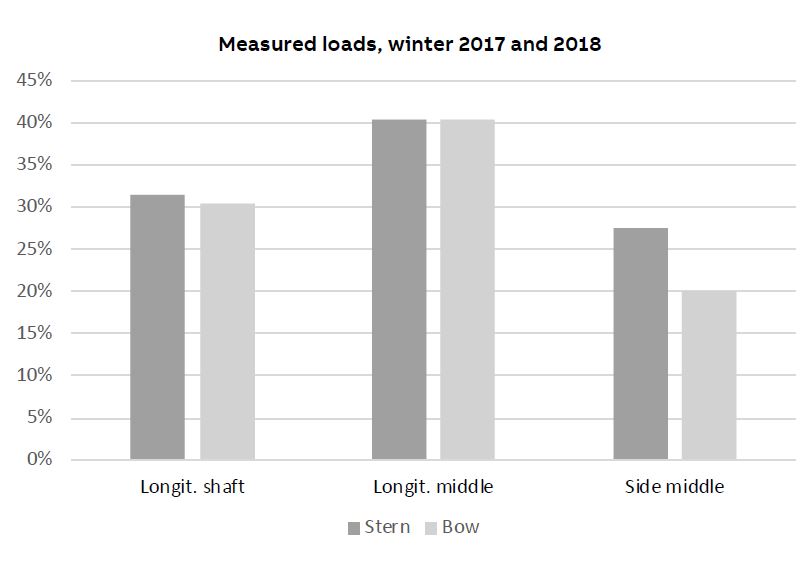
The Universal Polar Icebreaker
The 17 MW Azipod® units included as part of the Universal Polar Icebreaker concept should therefore be seen as a kind of culmination of all that has gone before, as a solution enabled for the highest Polar Class ice-going vessels.
In general, these mighty units incorporate familiar advantages: hydro dynamically favorable Azipod® unit position enabling hull form optimization for lower resistance; superior maneuverability ahead and astern; power generation based on the Dynamic AC enabling the fuel and performance efficiencies available to variable frequency.
In particular, though, the concept study confirmed that a polar icebreaker with two such high power podded propulsion units would be among the most capable polar icebreaker designs ever built, operating in first year ice with a continuous thickness of 2.4 m and penetrating thick Arctic sea ice ridges. What is more, such an Azipod® propulsion solution will achieve vessel maneuverability in difficult ice conditions superior to all existing and proposed polar icebreakers.
To further enhance the Universal Polar Icebreaker Concept, ABB and classification ABS agreed that ABS will perform an Approval in Principle process for the propulsion system. Depending on the outcome of the AIP-process, ABB will improve and refine the design in order to fulfill the requirements stipulated by ABS. This should speed up the delivery schedule of such Azipod® units in case they are chosen for a pending project.
In short, based on long years of experience, the Universal Polar Icebreaker concept presents an exciting opportunity for the industry to take advantage of a variety of technologies and systems that can deliver economic, operational and environmental benefits. The resulting state-of-the-art vessel will be equipped to deliver superior performance well into the future.
Sidebox
Polaris: state-of-the-art icebreaker
The Finnish government engaged Aker Arctic Technology to design and Arctech shipyard to build a new icebreaker that exhibits several of the technologies discussed in this paper. The Polaris features dual-fuel propulsion with three Azipod® units driven by either diesel or LNG-fired generators. It also has a remote diagnostic system allowing onshore experts to support troubleshooting and regular maintenance. The ship was delivered autumn 2016.
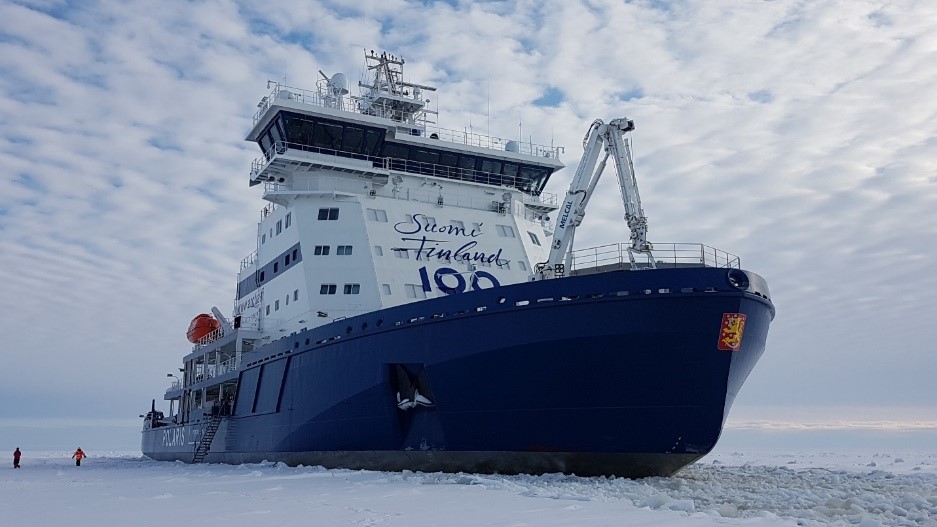
“We have assisted thirty merchant vessels but only one needed towing, as the Azipod® [units] are extremely efficient … the flushing effect keeps most of the ice away from the bulb of the assisted vessel. We have received plenty of positive feedback from customer ships for this feature.”
Captain Pasi Järvelin (source: Arctic Passion News)