Conventional condition monitoring of motors is costly and time consuming for large factories as engineers need to manually gather data and generate reports for each motor. When a motor fails, unexpected and expensive downtime and loss of production are often the consequence. But what if engineers could predict and address a problem before it occurred? What if the motor could communicate its health to factory operators and let them know when it is time for a service? And what if this could be done affordably at a large scale?
Smart Sensors
Smart sensors are the answer to all these questions. A sensor, about the size of a smartphone, is easy to attach to motors or other industrial assets, such as pumps, mounted bearings or gearing, turning them into a smart, wirelessly connected devices. The motors can then transmit their condition data to a smartphone or secure cloud-based server where it is further analyzed with algorithms, using decades of ABB experience and know-how. The analyzed result is then sent back to a smartphone or dedicated customer portal, informing factory operators about the state of the motor or pump, and predicting any potential problems before they become consequential.
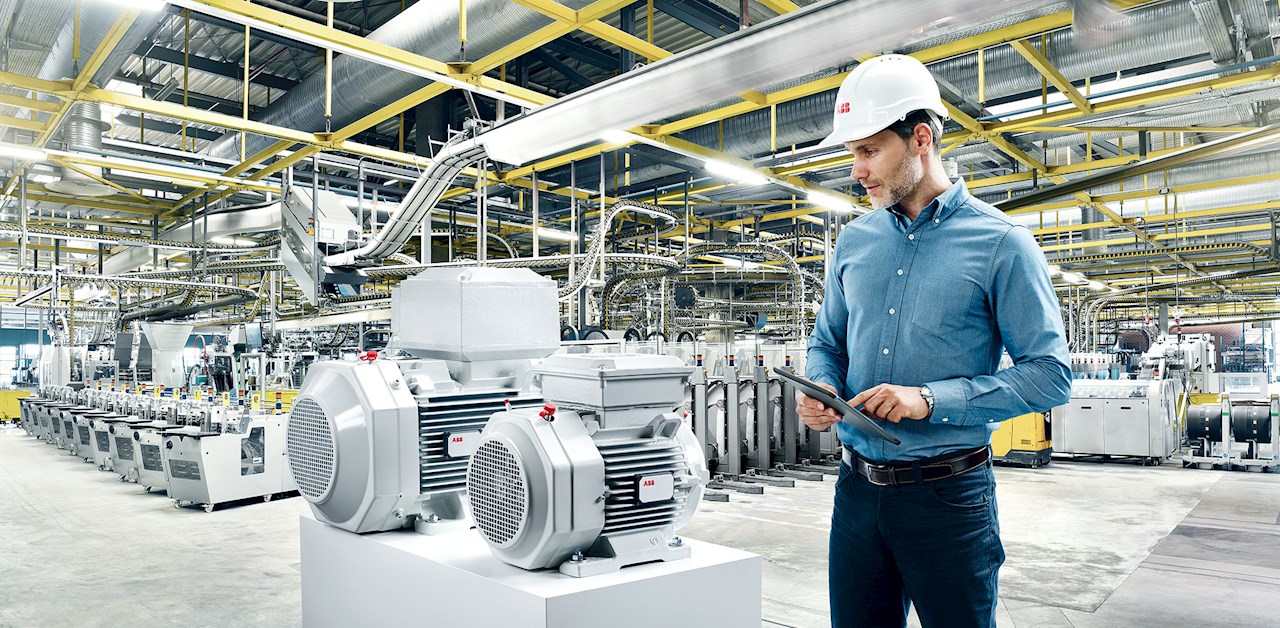
The ABB AbilityTM Smart Sensor condition monitoring solution allows operators to reduce downtime, extend motors’ life or improve energy efficiency. Unplanned stops are reduced or eliminated entirely, and maintenance schedules can be easily planned. Taken together, these factors result in higher productivity and significant cost savings for organizations. The simplicity and low cost overhead make smart sensors a viable option on a large scale.
Transforming the real world
Two recent examples vividly illustrate these benefits. The water utility of Singapore, the city-nation of 6 million, has one mission: to make sure that the rapidly growing metropolis – with few natural water sources and limited land mass – has a steady supply of clean water. This is a challenge, with water demand set to double in the next four decades over its current consumption of over 400 million gallons a day. With high operational costs, rising energy usage and a nationwide manpower shortage, Singapore needed to think beyond convention.
ABB and the Public Utilities Board (PUB), the water utility, conducted a successful pilot, which involved installing smart sensors on the PUB’s motors and pumps. “The sensors gave us real-time data that allowed us to reduce troubleshooting time, as well as manpower and paperwork. Our operators now have key operating parameters at their fingertips and receive real-time alerts of equipment problems,” said Jiawei Ng, PUB senior manager for infotech and digital transformation. ABB then installed an integrated solution with 22 smart sensors, remote condition monitoring, and Augmented Reality glasses (Microsoft HoloLens) to assist with maintenance and training. It also installed six ABB Ability-powered digital powertrains, which integrate sensor and drive data with cloud-based analytics along the entire chain of plant equipment, from drives and motors to pumps and bearings.
The ABB Ability™ Digital Powertrain condition monitoring portal allows customers to easily configure their powertrains and monitor key health and operating parameters via a single portal. “The Digital Powertrain alerts us to warning signs of failure, which helps reduce maintenance costs for my plant,” Ng says. “ABB is an important partner in PUB’s transformational journey so that our country can have a sustainable supply of clean, beautiful water, not just for today but for many generations to come.”
In another part of the world, Norway-based Yara International, a manufacturer of nitrogen-based fertilizer and other agricultural products, was faced with the challenge of maintaining a high level of efficiency in every area of production. Given that their plants have 400,000 low voltage motors installed, this needed an innovative solution that was affordable on a large scale.
ABB partnered with Yara to install the ABB Ability Smart Sensor condition monitoring solution on its motors. Thanks to this technology, data-driven insights of the condition of plant equipment could be gathered, allowing operators to take proper action before a breakdown occurred. This also saved on trips to the plant, another factor that impacts operational efficiency. Above all, maintenance can now be planned according to real-time needs, bringing Yara International one step closer to full condition-based maintenance of its plants.
“ABB’s solution helps us focus on resources where they are absolutely needed. The ultimate benefit for us is higher productivity and efficiency, increased energy savings, and a higher quality product for our customers,” says Perry Jaspers, Process Owner, Electricity and Automation, for Yara International.
Learn more about the ABB AbilityTM Smart Sensor here: www.abb.com/smartsensor