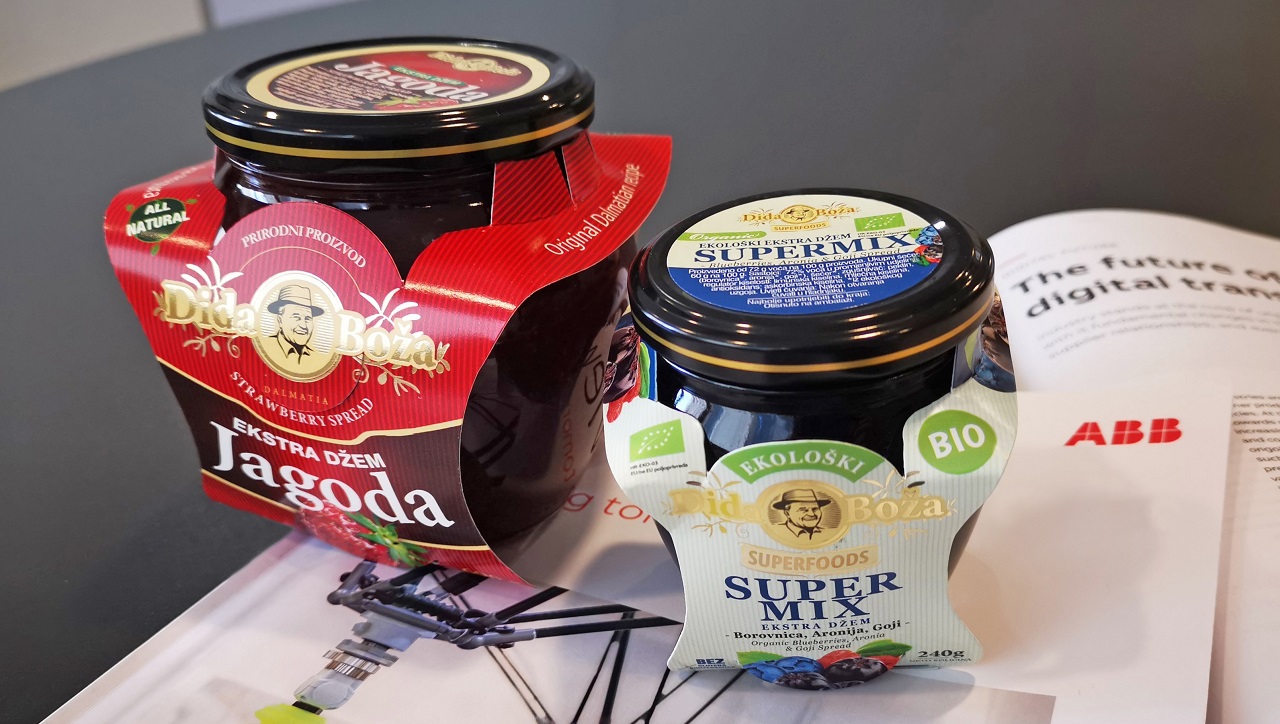
The Hermes international Ltd. food factory in Croatia produces specialty spreads and exports 80 percent of its total production to the USA, UK, EU and Asia.
Hermes International, like all food companies, is highly dependent on process production conditions, such as safety, hygiene, temperature and many others, that can lead to huge unnecessary costs and unpredictable situations if they go wrong. Any kind of process interruption can easily have serious and expensive consequences in terms of lost production time, food waste and quality issues.
The solution from ABB enabled the Hermes factory to improve the reliability and efficiency of the production process, upgrade the working environment for employees, reduce emissions and ensure the quality of raw materials and final products. The ABB technology incorporates reporting and alarming and the analysis of energy resources consumption to optimize production and costs.
Employing ABB Ability EDCS and Ekip UP enables Hermes to monitor energy and drive power peak shaving by managing different loads.
Ekip UP allows power peak shaving totaling 25 percent to 30 percent of average active power during 15-minute intervals, producing constant average power peaks during a whole day, month and year, thus saving up to three tons of CO2 emissions per annum only managing loads. The all-in-one solution embraces local and remote monitoring of values in real time, reporting and alarming and continuous monitoring of storage temperatures with Ekip UP digital I/Os.
“We are very pleased with the solution provided by ABB in Croatia,“ said Hermes International Head of Production Martin Brezovec. “In addition to limiting peaks in the power, we have better control over the consumption of energy sources. The system also triggers an alarm for temperatures in cooling chambers in the warehouse, a factor that highly influences the quality of raw materials and final products. During installation, ABB has proven to be a strong player in terms of collaboration, teamwork and understanding our needs.“
ABB digital solutions allow modifications during the production process and provide complete analytics for energy resources that can help improve productivity while reducing electrical consumption costs.
Implementation of ABB Ability EDCS and Ekip UP at the Hermes International factory is the first ABB project of this kind executed for the food industry in Croatia.
“The implementation of Ekip-Up All-in-One solution and ABB Ability EDCS enables the end user to significantly increase energy efficiency, have visibility of all key data for production and, most importantly, focus more on business continuity”, said Vjekoslav Vorih, Sales Manager, ABB Croatia.