The challenge
The maker of shipping containers needed to increase their production efficiency and achieve a high weld quality for custom-built containers.
The solution
ABB installed an automated solution with made up of ABB welding robots that were distributed across the base frame, front and back end, and general assembly areas. The welded parts have consistent shapes and the seam width is stable, thanks to the excellent repeatability and motion control of ABB robots. Moreover, automatic welding reduces the occurrence of pores, making the welding seam of the container more aesthetic.
The application
Automatic welding application using ABB’s Multi Move controller and Connected Services for optimized robotic operations.
CIMC produces a wide range of containers, including dry cargo and special containers, that are custom-made for different industries at its first automated cargo container manufacturing facility in Fenggang, southern China.
CIMC entered into a strategic cooperation agreement with ABB for a completely automated welding solution that would not only increase production quality but also create a safer working environment for CIMC’s employees.
The automated welding solution adopts 65 ABB welding robots distributed across the base frame, front and back end and general assembly areas. Twenty-four ABB IRB 1410 robots handle the previously manual task of welding the container base frames. Robots in the front and back end areas perform several types of welding including front corner post welding, inner and outer welding, front end vertical welding, and upper and lower ripple welding for the front end. In the general assembly area, eight more IRB 1410 robots are responsible for welding the front and rear reinforcing plates of the bottom beam of the containers.
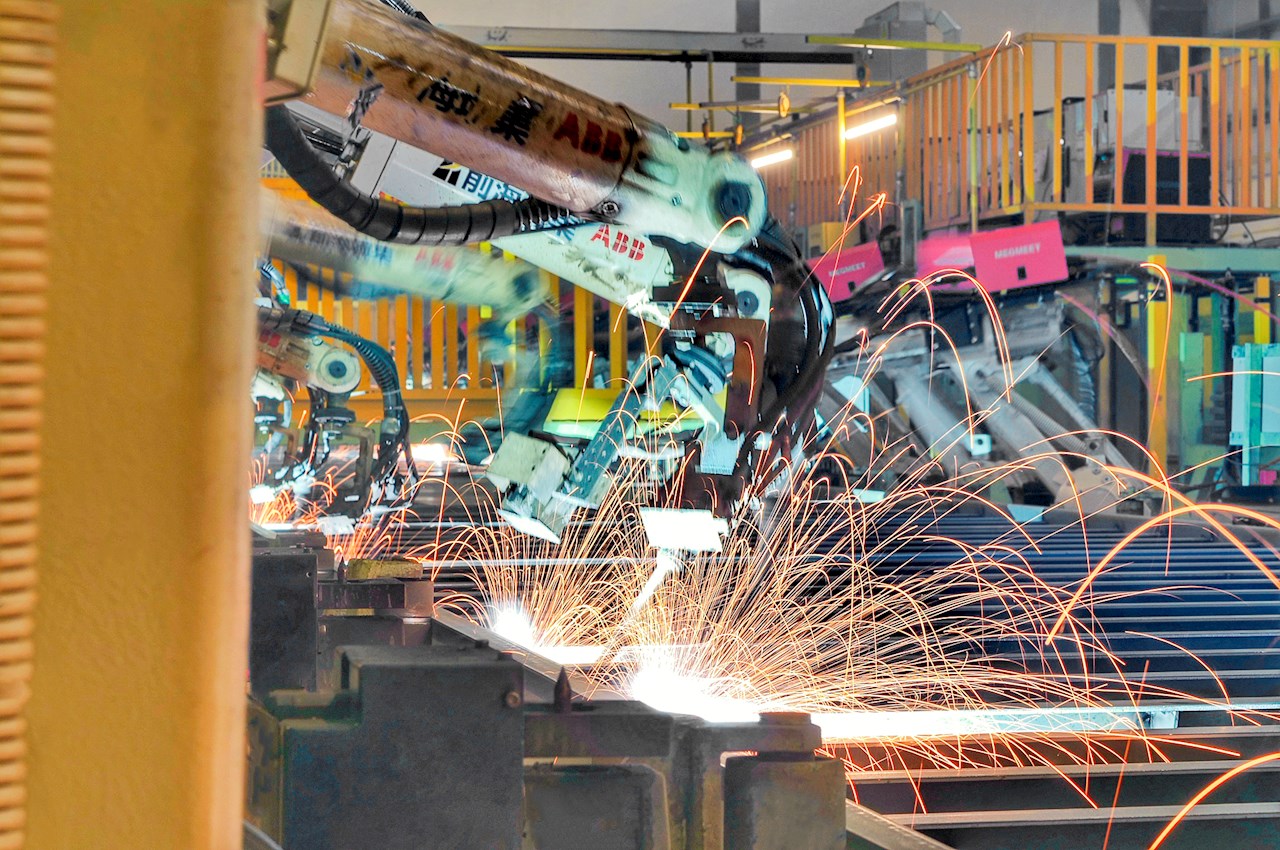
Traditional manual welding comes with many problems including shape deficiency and width change by the welding wire and welding flow. However, in automatic welding the welded parts have consistent shapes and the seam width is stable, thanks to the excellent repeatability and motion control of ABB robots. Moreover, automatic welding reduces the occurrence of pores, making the welding seam of the container more aesthetic.
ABB has also fitted several robots at the factory with its advanced Multi-MoveTM controller that allows two robots to simultaneously weld the front corner posts. This not only increases the cost-effectiveness of the entire welding process, but also saves time.
In addition to improving product quality, automatic welding also creates a better working environment for human workers as they no longer have to interact with gas flames, hot metal surfaces or be exposed to noxious fumes. Nowadays, the workers just need to monitor the production panel and learn to operate the robots.
“As a traditional industry, we have been using manual welding, which inevitably affects health even though workers wear protective equipment. However, the use of robots can help us effectively avoid this problem,” said Du Li, the workshop supervisor of CIMC’s Fenggang factory.
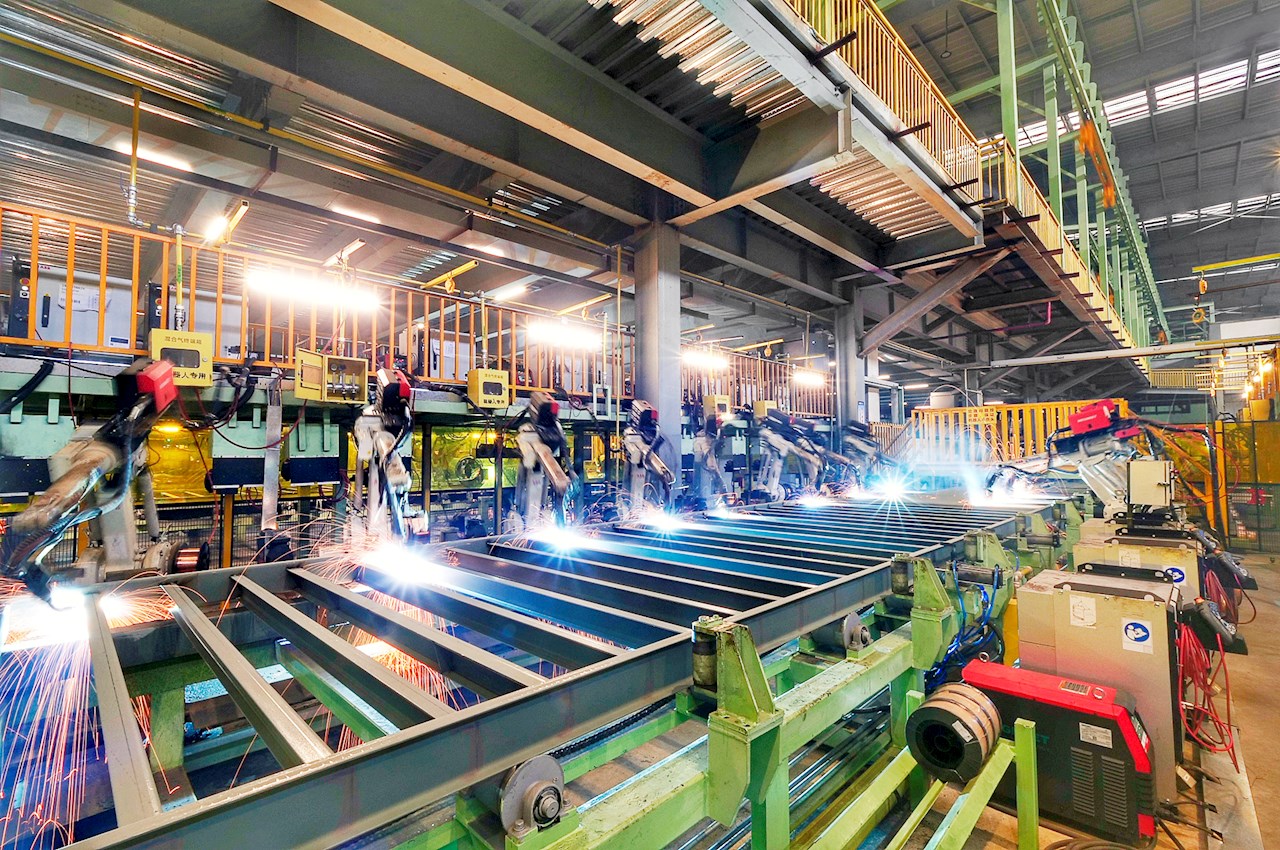
Robots not only make the production automated but also intelligent. Currently, the Fenggang Base is able to manufacture 275 containers per day, with an annual production capacity of 100,000 containers. These containers are ordered by different customers, with different specifications and process requirements. The flexible ABB automatic welding solution has many preset functionalities that have been installed on the robots, enabling the system to make rapid changeovers, seamlessly.
To help protect production against any unforeseen issues, ABB will also provide the Connected Services suite to help CIMC monitor the status of its robot fleet in real time. Connected Services will allow the company to upload manufacturing data to the cloud and take preventive maintenance steps to boost its manufacturing capabilities by safeguarding against production downtime.
“The application of robots in the Fenggang Base is only the first step in the upgrading of the CIMC’s container plants. Based on the Connected Services, we will focus on smart factory, data acquisition, data connection and platform construction as the next steps,” said Mr. Tan, the manager of Longteng Project, CIMC.
“Fenggang Base is a model plant for the renovation of our other plants.” Following the Fenggang Base, ABB has also provided other subsidiaries of CIMC with automatic welding solutions, to assist them in achieving more advanced and more intelligent upgrading of production lines,” Mr. Tan added.