Matti Lehti
Product manager, Onboard Microgrid
ABB Marine & Ports
Onboard Microgrid was introduced in 2019 to provide the benefits of hybrid DC-power systems and electric propulsion to smaller vessels serving inland waterways and short sea shipping. The product enables the entire DC-power system and its controls to be housed in one or two enclosures of very low height and with a limited footprint.
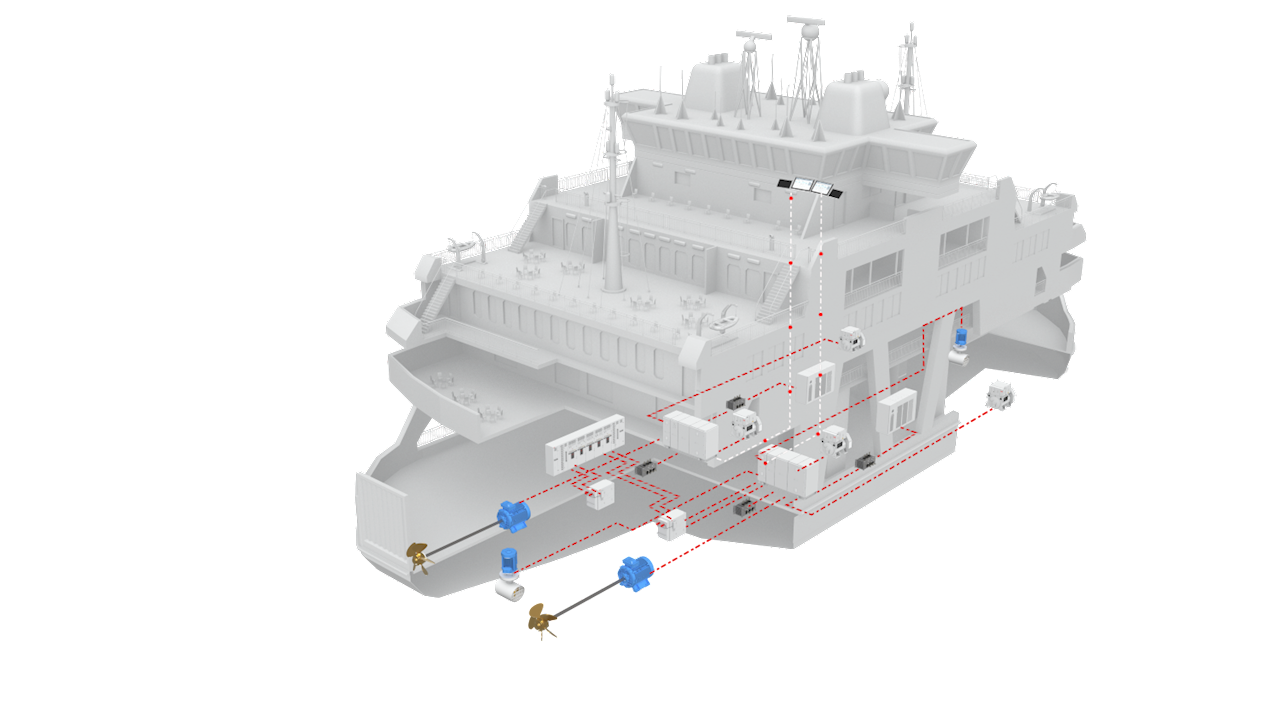
The core of the Onboard Microgrid solution is the drive cabinet OMD880LC, which houses an electric propulsion drive, AC-distribution power supply, and four optional power sources or consumers, all connected to a common DC-bus. These may be configured as diesel generator, shaft generator, shore connection, battery energy storage or variable speed motor drive for thrusters or other consumers. Frequency converter modules in the drive cabinet are ABB HES880-type. The water-cooled HES880 is designed for harsh environments in applications like marine propulsion, mining machinery and other heavy equipment. Maximum propulsion power from a single inverter module exceeds 600 kW, and higher power or redundancy may be achieved by utilizing two units to run a propeller. The system is well suited for double-ended ferries, yachts, sailing yachts, pushboats, tugboats, workboats, river vessels and PTO/PTI-systems.
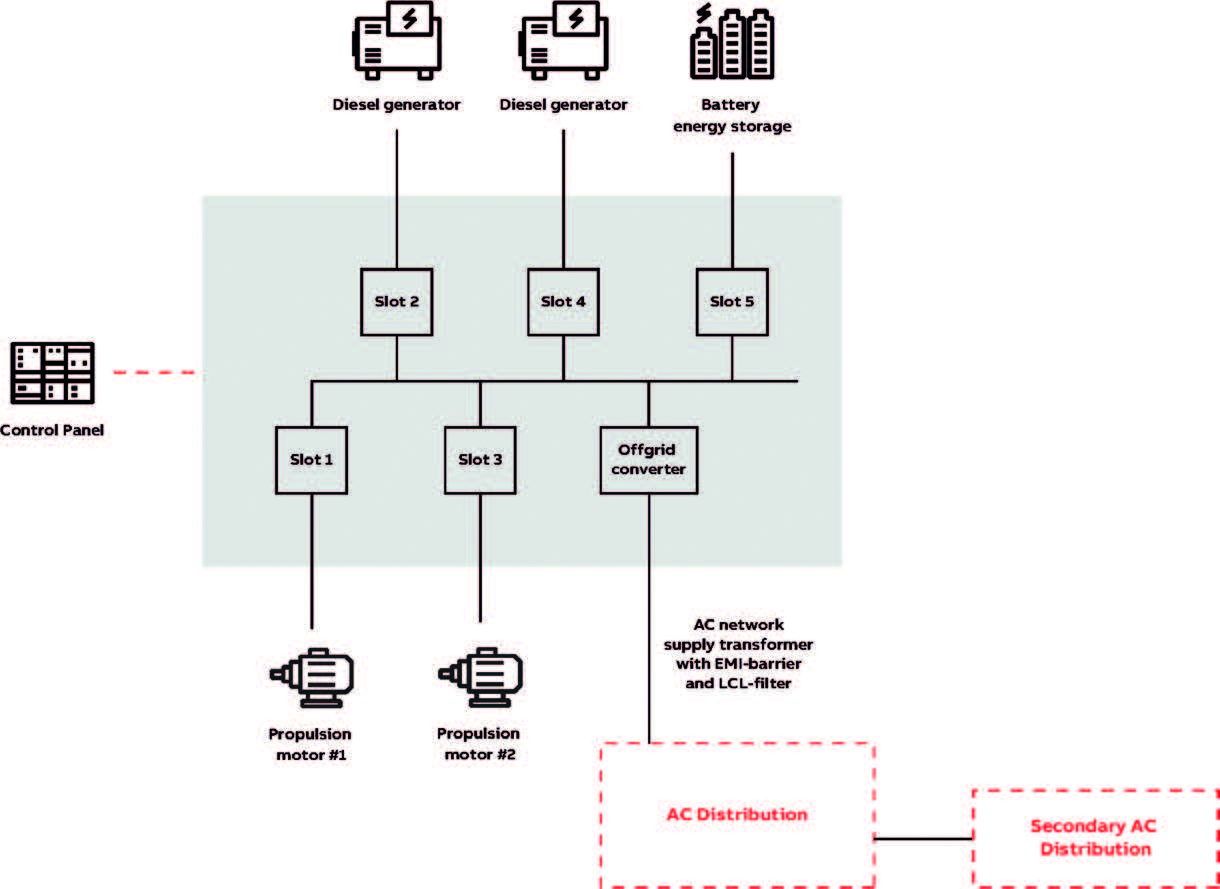
The integrated control system includes all functions required to operate the vessel’s machinery through a single HMI. Power and energy management functions support diesel generator sets, battery energy storage systems, shaft generator and shore connection as energy sources. These may be connected to a single OMD-unit or shared with two units.
The control system supports up to four selectable operating modes, depending on power sources. Diesel generator sets can be operated utilizing configurable running order and automatic start / stop power limits. In hybrid mode, the system uses energy storage to optimize loading or even out engine load variations.
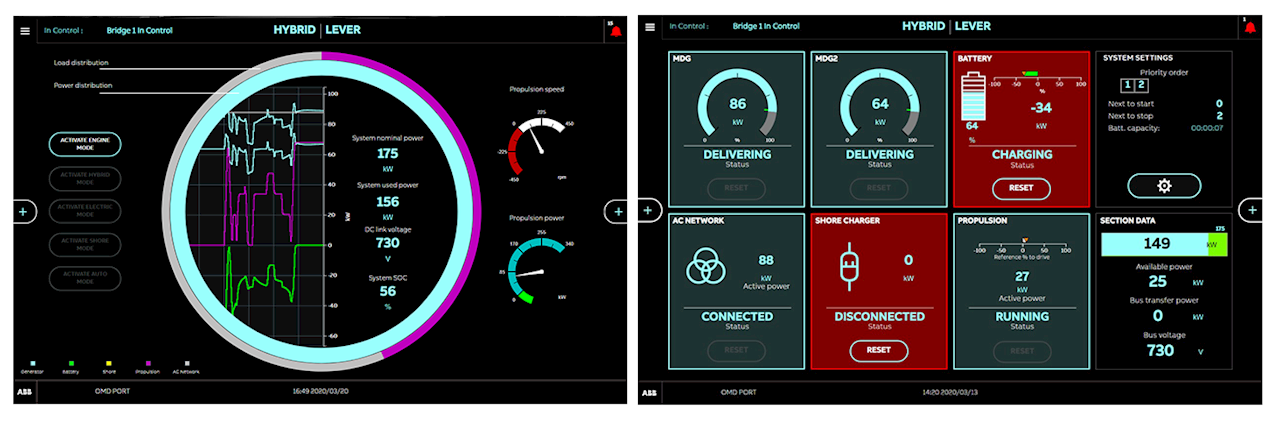
The control system also provides the possibility for automatic selection of mode, based on defined conditions like battery state of charge, propulsion power and shore power availability. This feature enables e.g. hybrid ferry operations with a minimum need for operator actions.
Mode | Description | |
Engine | One or more generator sets providing power to the network | |
Hybrid | Parallel use of generator and battery | |
Electric | Power from batteries | |
AC shore | For ship’s electrical consumption and battery charging |
Mode |
Engine |
Hybrid |
Electric |
AC shore |
The propulsion control system supports one propulsion drive in each OMD880LC-unit. This may consist of one or two motors and inverter modules. The propulsion motor may be connected to an azimuthing thruster or shaft line with either direct or geared coupling. The control system has built-in support for two control locations. For more complicated control schemes, it can be connected to a separate remote control system.
Supply and control of AC-power generation is also integrated into the OMD880LC. Each drive unit can provide more than 300 kVA 50 / 60 Hz power for standard AC consumers. A dedicated output transformer is used to adapt the voltage level and network type to vessels needs, and to ensure proper EMI filtering.
Where there are two installed units, the system controls supply breakers and bus tie breakers at two voltage levels, e.g. split buses for 440 and 120 VAC.
Onboard Microgrid in a double-ended ferry
The illustration below shows the control system setup of a vessel with two propulsion drives, diesel generators, energy storage systems and shore connection. In a double-ended ferry, the two remote control positions are located in the bridge consoles at either end. Both bridge consoles are equipped with an HMI panel for each drive cabinet, propulsion RPM-levers and push-button/lamp-panels for essential propulsion functions.
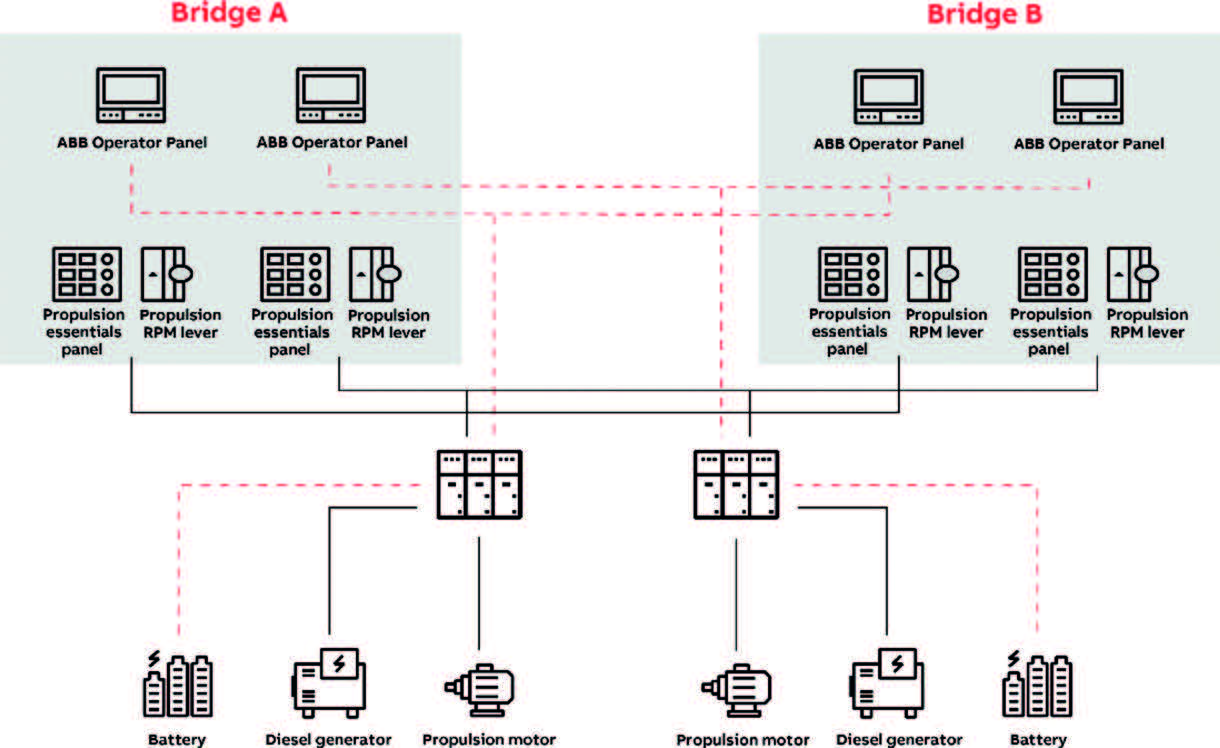
The necessary control and monitoring signals for electric power generation, propulsion and AC-network are all handled by the standardized Onboard Microgrid control system, considerably decreasing the amount of project-specific integration work.
The dimensions of one OMD880LC-unit are 2.1 x 0.8 x 1.3 meters, making it suitable for very low clearage spaces, and the water-cooled cabinet can be placed freely in engine room. In addition to the drive unit itself, space is needed for cooling units, AC-switchboards and transformers for AC network and shore connection. Shore connection systems and battery energy storage solutions are as such not part of Onboard Microgrid, but the system is designed to connect to and control both systems.
Use of DC-bus and electric drives makes it possible to adapt the same hardware in several configurations. In its simplest form, Onboard Microgrid can be used as traditional diesel-electric drive train without energy storage or shore connection systems. In this form, it provides advanced propulsion control and power management functions for a multi-engine electric propulsion plant.
The standard Onboard Microgrid integrated control system supports two-directional operation. The key feature is double-ended mode propulsion control, which sets the power of the forward propeller as a function of aft propeller power. It also considers the direction of the vessel based on control location and allows the operator to de-activate the mode at any time.
Onboard Microgrid with battery energy storage in effect turns a diesel powered ferry into a hybrid vessel, with the possibility of optimizing engine load and operating in zero emission mode. Energy storage power and energy capacities should be optimized to match engine power and the operational profile of the vessel. One possible use case for a ferry would be zero emissions during harbor stays and maneuvering. Batteries are recharged during the voyage, and the charging power is adjusted to run diesel engines at optimum load. Lower power requirements during maneuvering and time in harbor can be covered by stored battery energy.
Shore connection adds new possibilities for operation of Onboard Microgrid and battery energy storage. In its simplest form this can be a low power supply enabling cold ironing, and possibly slow charging of onboard batteries. It can also be an automated high-power fast charging system for full electric zero emission operation.
Integrated system platform
Onboard Microgrid was designed to make shipbuilding and system integration easier. The compact package with DC distribution and all main drives and associated controls within a single unit means savings in engineering and construction. The benefits include a smaller number of components to install, fewer cables to pull and connect, and fewer interfaces to design and test.
Owners also benefit from a truly integrated system. A robust water-cooled DC-system provides high reliability and long lifetime. Use of single frequency converter type and a single control system for all main drives reduces spare part stocks and simplifies troubleshooting. Finally, for the operator, the Onboard Microgrid user interface enables control and monitoring of electric power generation and propulsion systems through a single, intuitive HMI.
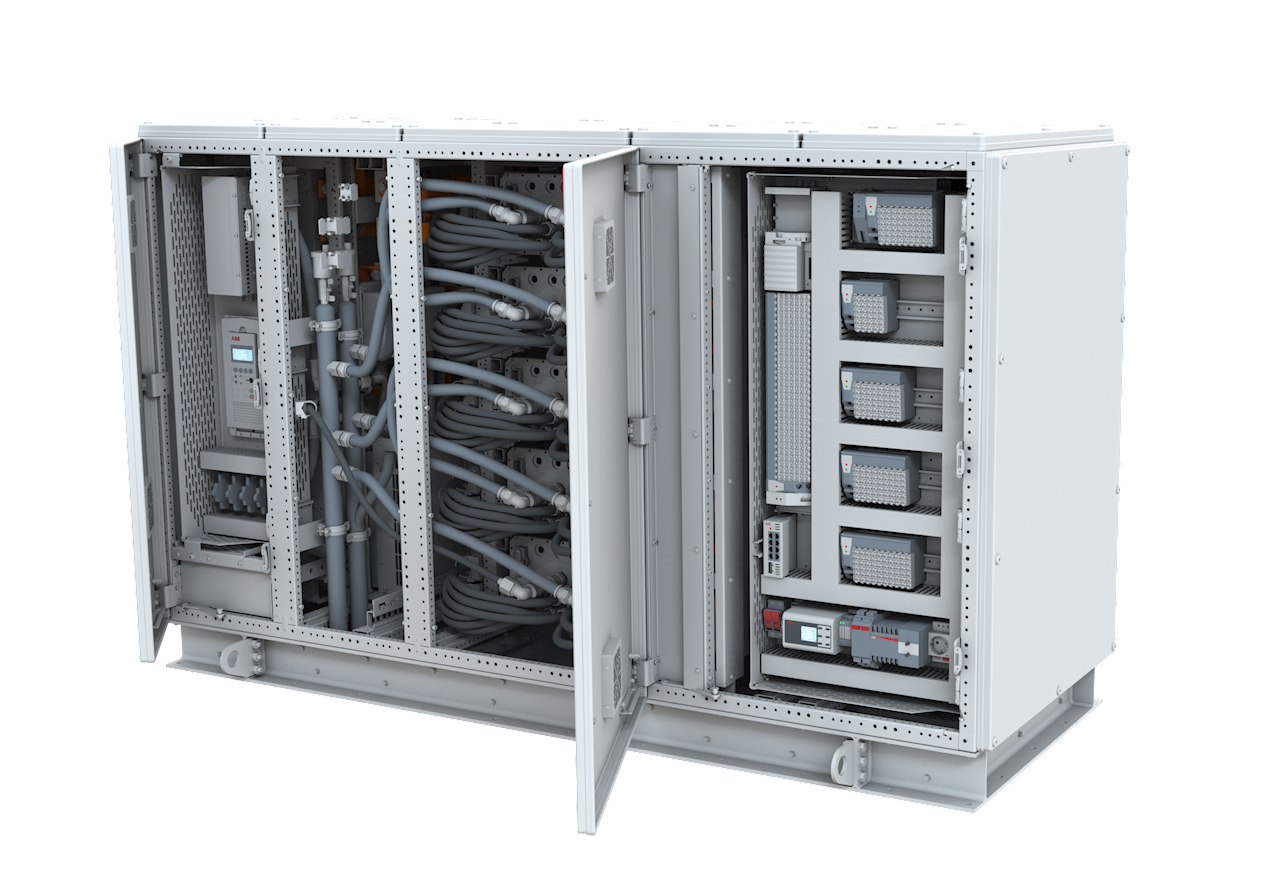