This has made the process much easier because Straub Cosmetics did not need to familiarize themselves with the device parameters. Moreover, the remote technical support led to cost savings since onsite expert deployment wasn’t required.
A technician does not always need to be called for every action that may be required on a drive. This is particularly true when only a few parameters have to be changed or a simple action is needed to resolve a minor failure. In many cases, ABB Ability™ Mobile Connect provides a simple and quick solution, and requires only two things on-site: a smartphone with ABB’s Drivetune mobile app installed and a control panel with a Bluetooth connection on a compatible drive.
Reduced time and less chance of mistakes
Straub Cosmetics recently experienced the added value of this service when the replacement of an agitator drive was needed. Lamb, ABB’s partner, supports Straub’s cosmetic manufacturing processes when technical questions arise, and they suggested using this opportunity to get support via a smartphone. The Mobile Connect solution goes beyond classic telephone support: it allows chats, sharing images and backups, viewing parameters online and sending support packages, making the partner’s technical support process quick and efficient. The pivotal point is the drive’s Bluetooth control panel: the maintenance engineer can access it with a smartphone to give a remote support expert access to the status of a variable speed drive.
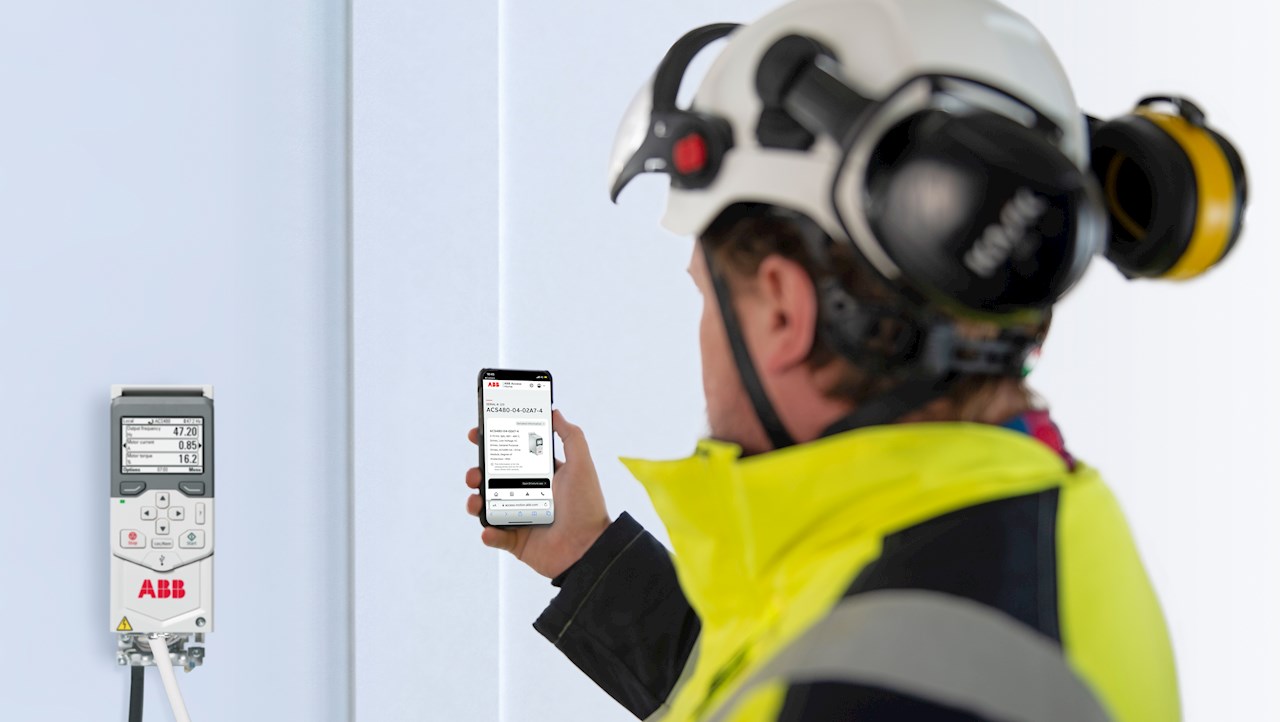
Andreas Dürr, electrical engineer at Lamb, explains: “Previously, we've had only two options in the event of service calls: contact by telephone or onsite servicing. For the former, the customer had to read out which parameter values were set in the old drive. That’s time-consuming both for the customer and technical support. The customer then had to enter the parameter list manually. This approach can lead to mistakes if there is a misunderstanding over the phone.”
The second option has always been the onsite deployment of a service technician, which results in additional travel expenses. And of course during the pandemic years 2020-2021, many companies did not want to have external staff onsite.
Easy parameter adjustments
ABB Ability™ Mobile Connect platform was used for the first time at Straub when a larger motor was required for an agitator. As part of the retrofitting, the existing ACS480 ABB drive was replaced by a more powerful unit of the same series.
To set the right parameters in the new drive, ABB’s partner Lamb used the Mobile Connect platform to retrieve the parameters from the old drive. Motor data was imported into the parameter set, with current, rotation frequency, and torque limits adapted to the application. When working with Mobile Connect, the onsite system maintenance engineer always has the final say for any setting changes to ensure safety and continuity of the production process. The parameter set suggestion was then checked by Straub’s maintenance engineer and copied into the new drive via smartphone.
“The solution is easy to use and doesn’t require any lead time. The costs for service calls are therefore lower,” summarizes Straub.

Remote access to ABB expert knowledge anywhere, without delay
ABB Ability™ Mobile Connect is an advanced function of the Drivetune app, enabling remote access to drives on a case-by-case basis. The app can establish a direct connection to the support line run by ABB or by the service partner in order to prevent failures and to ensure increased productivity. The solution provides access to experts via smartphone with the option of exchanging voice and chat messages, images, videos, and data. This also includes the creation and transmission of parameter backups and support packages with adapted parameters to accelerate commissioning or troubleshooting.
Author
Michael Spuck
Product Manager, Drives,
ABB Motion Germany