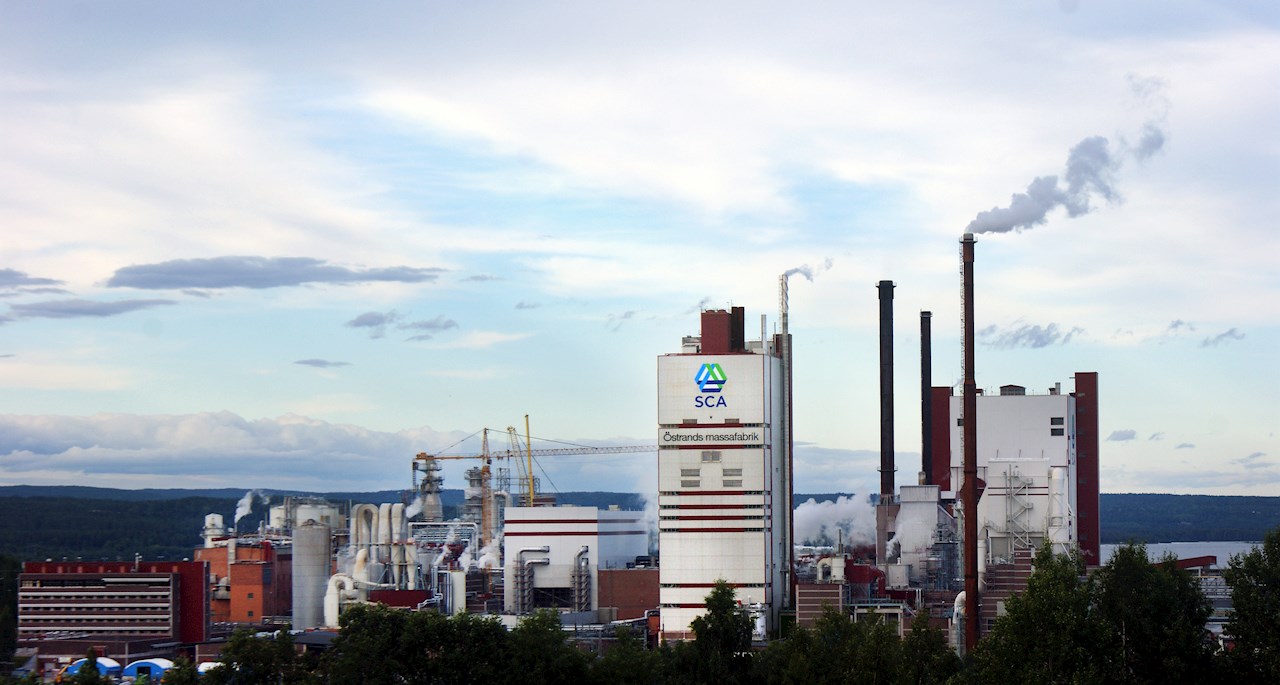
In addition to having the world's largest production line for bleached softwood sulfate pulp, all of the mill's processes are now fully controlled by an automation platform that has common standards. The digital solution has been delivered by ABB, which provided a new control system and new operating center for the mill.
As in most process industries, SCA Östrand’s new pulp mill has several different processes that will work on their own. With the help of ABB's automation platform ABB Ability™ System 800xA and Advanced Process Control (APC) solution, SCA has taken this a step further and ensured that the process components will interact smoothly and work together as a whole.
The parent control via APC allows the processes to be read to ensure that the power supply and production processes can be sustained at a continuous high level. At the same time, operators have full control over the system and can control it against various key ratios such as reduced energy and other operating costs while keeping processes within emissions restrictions.
"The new digital control system is a good example of how we can leverage our resources even better to increase our productivity and our margins," says Ingela Ekebro, project director at SCA.
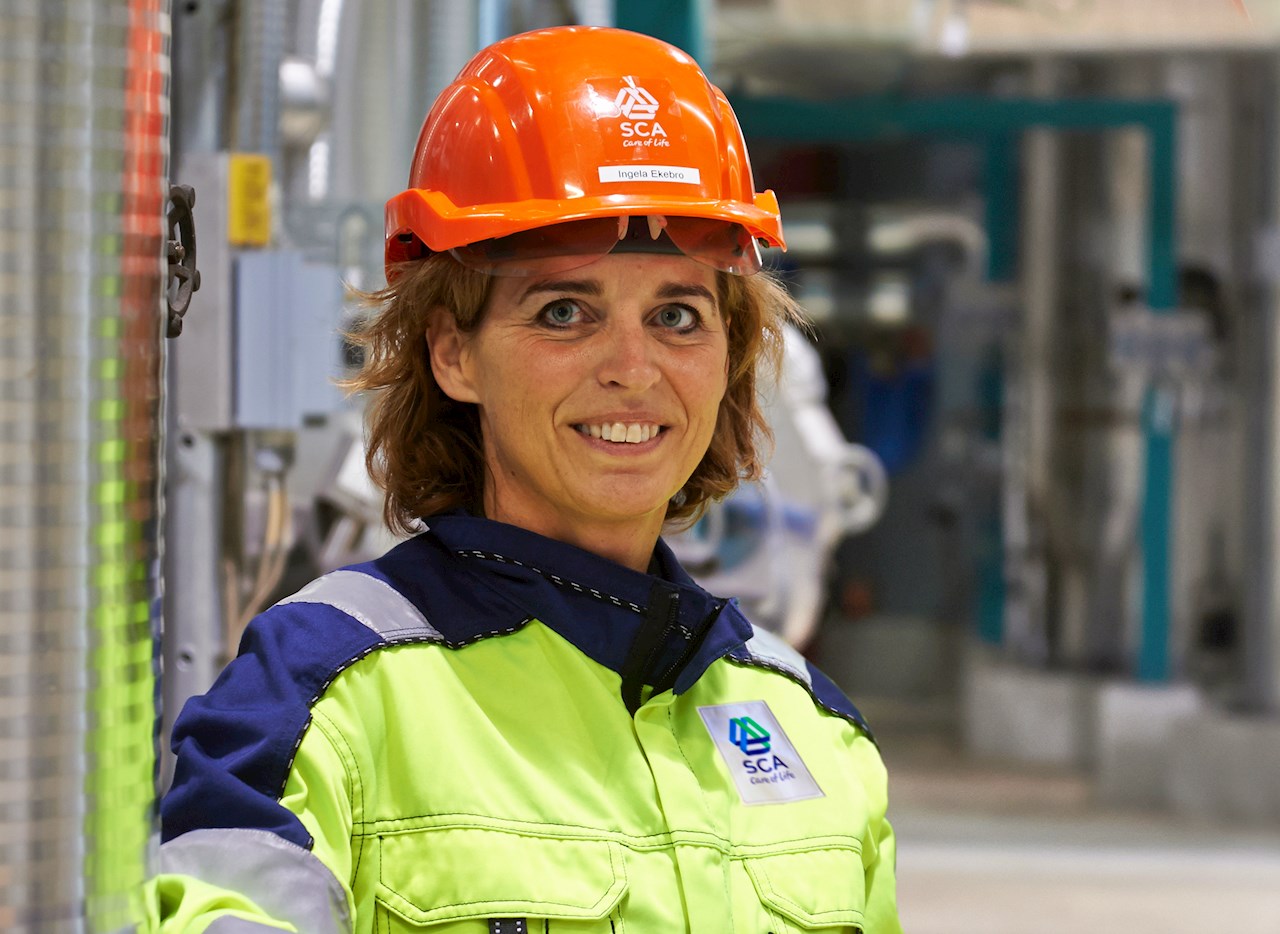
SCA Östrand’s new pulp mill is one of Sweden's largest industrial initiatives ever. When the mill, which was launched in June, is at full operation at the end of 2019, it will produce a million tons per year, of which 900, 000 tons will be bleached softwood sulfate pulp. Since the automation system is such an important cornerstone that affects all parts of the mill, ABB’s solution was chosen to get a unified platform and quickly get started with the design. An automation platform for the entire mill with common standards, components and procedures facilitates this speed, both at start-up and throughout its life cycle.
Another advantage of the new mill is a single operating center. ABB has supplied the central control room with seven Extended Operator Workplaces with an integrated solution that provides the operator with a clear process overview, as well as possibilities to personalize ergonomics and the work environment in every aspect, from working posture to sound and lighting.
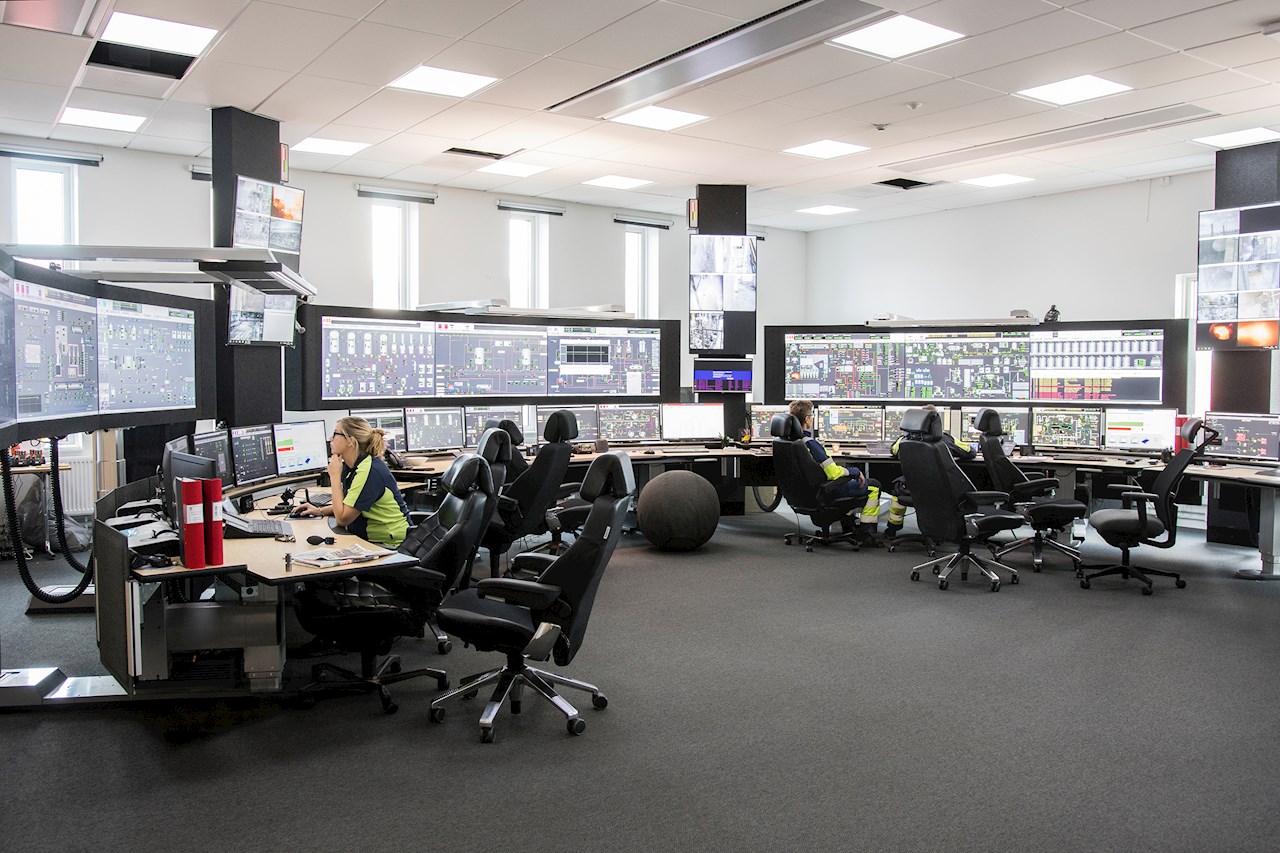
"The joint operation center with a common interface allows operators to have a good understanding of the whole, which gives even better conditions to optimize the overall flow and facilitates training," says Ingela Ekebro.
In addition, ABB also delivered a digital solution for process simulators that allowed operators to simulate both their own and overall processes in advance.