Summary
The application:
Processing of COVID-19 test samples
The challenge:
Test centres in Singapore needed to dramatically ramp up the rate of COVID-19 sample testing to meet the government’s target of processing 40,000 samples a day. There was also the need to avoid the injuries to staff that can occur from carrying out repetitive movements over a long working day
The solution:
ABB SCARA robots operating in a cell allowed samples to be processed four times faster than using manual methods. They also removed the need for people to carry out repetitive tasks, avoiding the risk of injury while also ensuring the health of staff by protecting them from possible exposure to viruses.
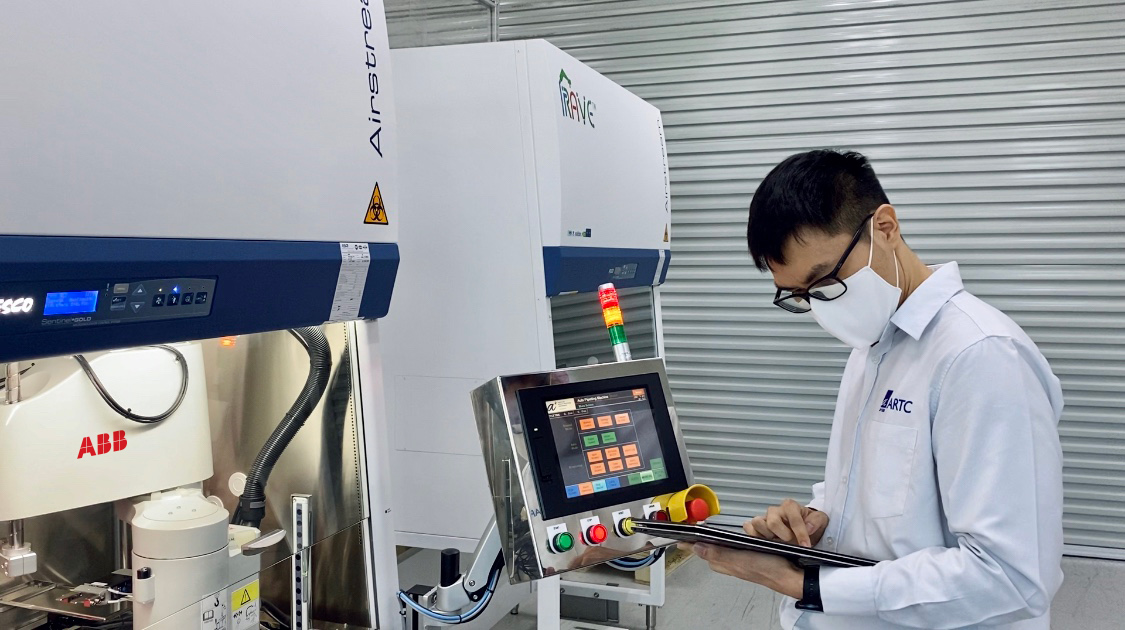
ABB SCARA robots are being used to deliver high-precision performance as part of a new automated laboratory system being deployed in Singapore to help in the fight against COVID-19. The system, known as the Rapid Automated Volume Enhancer (RAVE) uses the robots to automate several of the laborious tasks involved in sample processing, enabling up to 2,000 samples to be prepared in a single day, around four times faster than manually-based routines.
To help limit the spread of COVID-19 in Singapore, the Government has set a target of increasing the rate of daily testing from 20,000 to 40,000, with the ability to deliver results within 24-hours to help avoid people quarantining themselves unnecessarily. With laboratory staff already stretched, the decision was made to find an automated alternative that could help to increase the capacity for testing.
Housed in a bio cabinet measuring 4ft by 4ft, the RAVE system prepares 96 samples at a time ready for testing by a Polymerase Chain Reaction (PCR) machine.
The system was co-developed by the Agency for Science, Technology and Research’s (A*STAR) Advanced Remanufacturing and Technology Centre (ARTC) and the Singapore Institute of Manufacturing Technology (SIMTech), as well as the Diagnostics Development (DxD) Hub, a national platform hosted by A*STAR. To ensure that two SCARA robots could operate efficiently in the confined space within the bio cabinet, ABB created and ran a simulation using its RobotStudio® offline programming software.
“A key challenge was to ensure that the two robots could move without colliding or getting in each other's way,” says Ravikumar Singadi, Head of ABB’s Robotics and Discrete Automation business in Singapore. “To show that our robots could meet the requirements of the application, we first ran a proof of concept in the presence of the ARTC project managers using one robot, before doing a second test with two robots to demonstrate their ability to work together.”
With the concept fully pre-tested and refined in RobotStudio, the project was able to be successfully realized and ramped-up quickly, without the need for major adjustments or corrections in the laboratory environment.
Sampling stress removed
Aside from the greatly accelerated rate of sample processing, a major benefit of the automated system is its potential to eliminate physical strain on laboratory staff and the risk of errors arising from performing the monotonous and repetitive tasks inherent in sample processing.
“In a manual process, someone has to perform each stage over and over again for up to eight hours a day, presenting the risk of potential errors caused by strain and fatigue,” says Ravikumar. “Reaching the Singapore Government’s target of conducting 40,000 tests a day would put huge pressure on laboratory staff if every part of the sampling and testing process had to be conducted manually. By helping to automate the sample preparation stage, our robots can help to remove much of this pressure whilst ensuring that every sample is processed quickly and without potential errors that could lead to tests being invalidated.”
Furthermore, with the robots now carrying out the mucus extraction and handling within the confines of the bio cabinet, human operators are protected against the risk of exposure, helping to allay concerns expressed by many about handling mucus samples throughout the day.
“The great thing about the RAVE system is its ability to be readily applied to help research other diseases, either those we know about or new strains that could cause future epidemics or pandemics,” says Ravikumar. “In each case, removing human operators from the need to handle samples can help to remove the anxiety around becoming exposed to potentially deadly viruses.”
Automating the fight against COVID-19
ABB initially supplied four IRB 910 SCARA units, including simulation and programming support, used in the pilot testing cell. After a three-month development period, RAVE was unveiled in July 2020. Since then, a total of 31 cells have been ordered, each with two ABB SCARA robots, with delivery due for mid-December.
“We are honoured to be able to apply our industry-leading robotics technologies to help Singapore’s medical ecosystem tackle the urgent challenges involved in halting the spread of COVID-19,” says Sami Atiya, President ABB Robotics & Discrete Automation. “Working with the engineering and biomedical knowledge of the agencies involved, we are increasing Singapore’s testing capacity by automating key laboratory processes, with our robots undertaking a range of repetitive and dangerous tasks to improve laboratory conditions for employees, reducing the risk of contamination and fatigue.”
This project is just one of a number of examples of how ABB’s robots are being used to help in the fight against the COVID-19 pandemic. ABB’s YuMi dual-arm collaborative robots, for example, are being used in projects in Thailand and Italy to help speed up sampling and testing processing and enable skilled laboratory staff to be redeployed to other tasks.